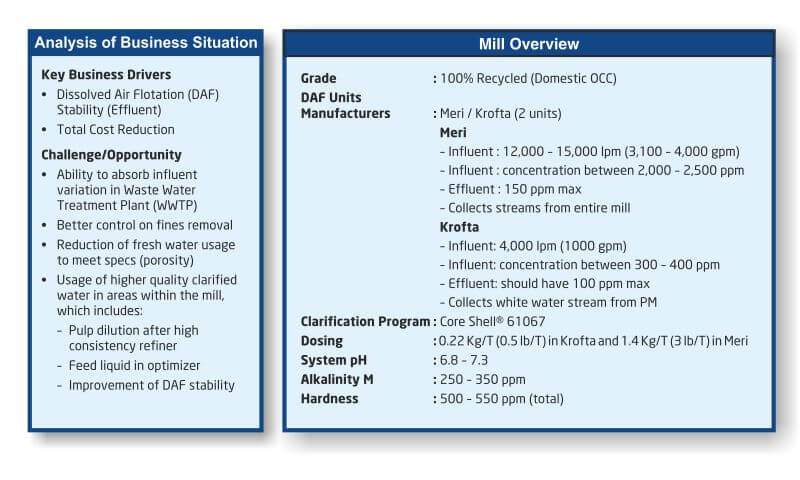
Business Situation
Nalco had successfully installed PARETO Optimizers on the process side (Paper Machine) at a customer site. The offering effectively balanced the interrelated and dependent variables of hydrodynamics, chemistry and water management. Due to this success, the Nalco team at the mill and Customer Management decided to explore new opportunities in trying to integrate the process into the waste water treatment side. The idea was the involvement of a new stage – improving the mixing between polymer (cationic latex high molecular weight) and influent, aiming for stability in dosage as well as ensuring that optimal chemical efficacy was achieved.
PARETO Mixing Technology is a custom-engineered post-dilution and injection port system, which enables post-dilution of concentrated flocculant solution immediately prior to the injection point. PARETO Mixing Technology delivers multiple benefits that can be categorized into two categories –process efficiency and product quality.
Background
There are two basic flotation processes: dispersed air flotation and dissolved air flotation. In dissolved air flotation, minute gas bubbles are formed by the precipitation of air from a supersaturated solution. Generally, the bubbles are a smaller size of 10 to 100 microns.
Polymers improve flotation by increasing the size of the particles in the waste. The coagulants neutralize the electrical charges surrounding the particles, allowing them to agglomerate. The flocculant bridges are the agglomerations forming a large structure for the absorption and trapping of the air bubbles. The most effective polyelectrolytes have either been moderate molecular weight coagulants or very high molecular weight cationic flocculants.
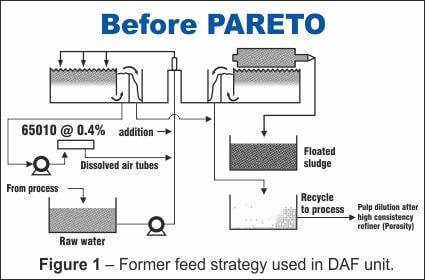
Program Design
In a conventional T-Jet injection system for these chemical aids, the chemical is inverted to a specific concentration in order to get the best inverted polymer. Then, it’s diluted with fresh water prior to the feed point in order to obtain the best interaction with influent.
In this case, the polymer was being inverted to a lower concentration and being fed without extra dilution water. Nalco was able to invert the polymer properly and add sufficient water to obtain a much better mixing.
The main concept is that if someone is injecting the inverted polymer into a process stream pipeline, full distribution of the product stream at a desired distance downstream will be achieved.
The PARETO Mixing Technology offering consists of a customengineered solution for unique applications, and is comprised of preliminary screening tests, a MixJet™ analysis, free comparison to alternative feed methodology, custom CFD calculations, the novel PARETO technology Optimizer, complete engineered delivery systems and additional optional physical simulations (upon request) that can further define optimal feedpoint selection.
Nalco sales engineer not only determines the relevant process parameters but also works closely with customer to determine what are the objectives of an installation in terms of water, energy or chemical savings or operational efficiency and/or finished product quality improvements.
Key Performance Indicators
• Influent ppm
• Influent flow
• Polymer flow
• Effluent ppm
Program Results
Benefits of the Process:
DAF Efficiency:
• Less effluent variability
• Improved solids removal with the same flocculant dosage
Stability of Clarified Water:
• Utilized 75 percent less of the fresh water
• Clarified water used in other processes such as Pulp Post Dilution
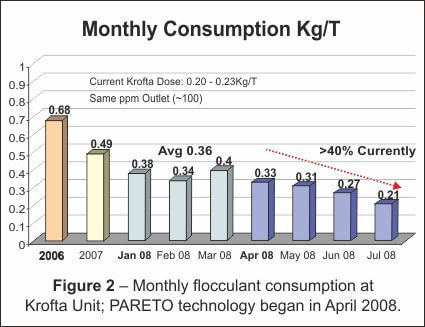
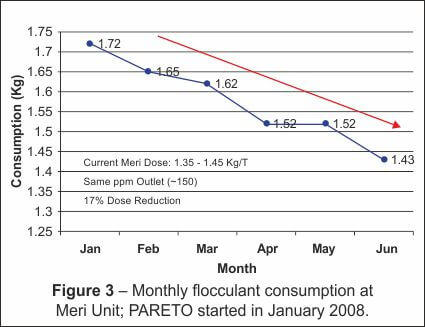
Runnability:
• Better control on forming table (water line); paper sheet moisture uniform to press section
• Ability to keep critical properties in main grade (sack paper), like porosity, by having less fines in the short loop
• Used to drain silo; was utilizing fresh water once/week, now only once/month
If one or more of the following statements applies to your company, PARETO Mixing Technology could be of benefit:
• Use of single point injection systems; or poor system designs, including quills
• Use of static mixers
• Use of applications with feedpoint too close to reaction chamber
• Have applications that use high amounts of flocculants, coagulants or macrocoagulants
• Experience runnability issues associated with overdosing flocculant, especially flocculantsensitive application
• Use significant amount of fresh water for chemical post-dilution
• Have inadequate post-dilution water, or with quality issues
Conclusion
There was a flocculant dose reduction, (between 17 – 40 percent) due to improvement in mixing efficiency, allowing the company to handle 42 ton/yr less Core Shell and reduce the amount of VOC in the system.
The customer was able to remove fines from this post-dilution stream in order to have better stability in parameters, such as porosity without the need to drain white water in the process and replace it with fresh water.
PARETO Mixing Technology has also shown benefits in terms of On-Machine Efficiency (OME) gains recognized as a result of reductions in wet-web breaks caused by cleaner post-dilution stream. These improvements have also resulted in improvements in finished product quality parameters.
The maintenance of the PARETO Mixing Technology system is fairly simple and safe. The PARETO Optimizer has been designed to be robust, durable, easy to install and easy to disassemble for inspection and cleaning.
Periodical check-ups of the PARETO Mixing Technology system are required in order to observe any changes in pressures and flows from the designed values.
The applied chemistry in terms of molecular weight, charge, structure, program type and how each variable will impact the rate of reaction with the thin stock understood (not sure if under-stood is the right word here) and accounted for in the design stage.
Finally, these variables are balanced with water management to the extent that post-dilution water is optimized for source and demand. These three components are balanced together to ensure that optimal delivery to the paper machine is achieved in terms of cost, operational efficiency and finished product quality.
PARETO Mixing Technology
PARETO Mixing Technology is new to the market, yet is being used by an increasing number of customers in the paper industry. Enhanced system performance through advanced chemical application yields better fiber recovery, and also delivers major reductions in the demand for water and energy. By reducing this demand, there is a direct impact upon the customer’s environmental footprint and performance, and a major contribution to the sustainable development of paper mill operations.
Since the introduction of PARETO Mixing Technology in 2006, 360 units at 66 customer sites have saved nearly three billion gallons of fresh water (~ 11 million m3) and over a 1,000 billion Btu’s (>360 GH-h) of energy. This is equivalent to:
• 212,000 barrels of crude oil
• 17,500 cars removed from roads
• 91,000 tons CO2 released to environment