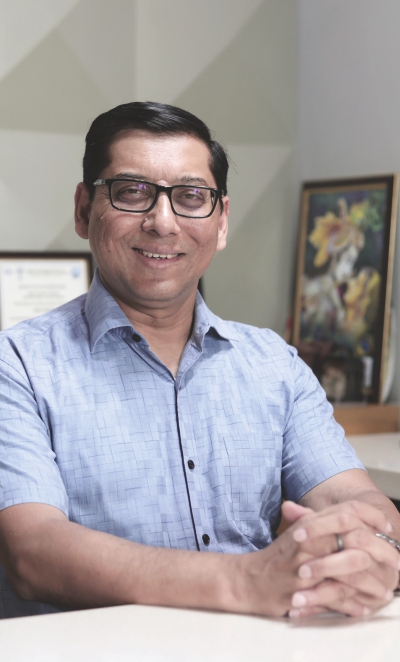
In 2021, Naini Papers in Uttarakhand, India, started up its new Valmet cooking, fiberline, recausticizing and lime kiln equipment. Although the project faced challenges due to the Covid 19 pandemic, the excellent cooperation between Naini and Valmet overcame these hurdles with a bit of creative problem solving. The new line has now been successfully producing high quality pulp since the very smooth startup. Initially designed to make approximately 300 tons bleached hardwood pulp per day, production capacity was quickly upgraded and now the plant is easily able to make 370 tons per day. Naini chose Valmet in 2019 as the main supplier of the key process technology for making bleached hardwood kraft (BHK) pulp. Mr. Pawan Agarwal, Managing Director of Naini Papers, explains the rationale for the investment in wood-based pulping, after having always relied on non-wood fibers in the past.
Naini chose Valmet in 2019 as the main supplier of the key process technology for making around 100,000 tonnes of bleached hardwood kraft (BHK) pulp per year. The main aim of the expansion was to have BHK pulp to augment the non-wood agro-based fibers that Naini had been using earlier. In addition, Naini was targeting environmentally friendly fiber production that also gave both low effluents and low operating costs.
Concern about Shortage of Non-Wood Fiber Sources
Mr. Pawan Agarwal, Managing Director of Naini Papers, explains the rationale for the investment in wood-based pulping, after having always relied on non-wood fibers in the past. “We were an agricultural fiber based papermill since we started 25 years ago, mainly using bagasse and wheat straw as the main raw materials. But we were seeing less availability of these agro raw materials, and we realized that there might eventually be a major shortage of bagasse and wheat straw. Thus, that was our primary reason for building this line. In addition, we also wanted to raise the overall quality of our products and extend our product portfolio, and to do that wood was a good alternative. Finally, we wanted to add a new paper machine based on wood pulp, so putting these aims together, it made good sense to add this hardwood pulp line.”
The cooperation and teamwork between Naini Papers and Valmet has been excellent, says Mr. Agarwal, as he anticipated it would be. “We selected Valmet purely on the basis of merit, as they have some very good references in India and abroad as well. We visited some and saw the technology running well, and we were impressed with the performance of existing Valmet fiber lines. Therefore, we chose Valmet as a natural partner for this fiberline. I must say that the start-up was beyond our imaginations.”
Watch: JMC Paper Tech Launches New Subsidiary JMC Papers
Smooth Project Management and Start-up
Mukesh Tyagi, Technical Director at Naini Papers, is extremely pleased with the overall execution of the investment. “I have never seen such smooth commissioning of a large project. All the parts – the fiberline, recovery, lime kiln and recausticizing – have been really nice experiences, based on excellent communication between the teams. We had no problems during the execution and commissioning and I can honestly say that I actually have no negative feedback about the cooperation with Valmet, because we got everything we asked for. Even overseas engineers came promptly whenever we felt it was needed, which we really appreciated”.
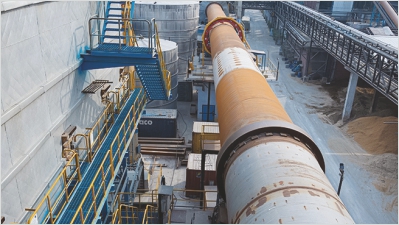
Looking specifically at the recausticizing operation, Sanjay Bhore, Senior General Manager of the recovery plant, is also highly satisfied with the way the equipment is performing. “One of the best solutions from Valmet for our recausticizing project is the Opti Disc Filter, which is the first one ever adopted in the agro-fiber business. So initially there was some concern about how well it would work, but we had confidence we would succeed. I can say that the support provided by the Valmet team has been wonderful. And the Opti Disk filter is performing extremely well here. We understand that normally the filter cloth must be changed after 6 months, but we are running smoothly and have not changed it for 14 months. So, the equipment is working very well.
Freshwater consumption was a critical parameter for the project and with the target to be less than 9.5 m3 per ton of pulp, due to water restraints in the area, explains Mr. Agarwal. “And I’m happy to tell you that we have achieved close to 9, so it is better than what we had targeted. And now we are planning to bring it down further.”
“One of the best solutions from Valmet for our recausticizing project is the Opti Disc Filter, which is the first one ever adopted in the agro-fiber business.”
Valmet’s Strong Indian Presence, and Top-Level People and Equipment, Were Critical
From Valmet’s viewpoint, Varun Jain, Director, India Region, explains that there were several important factors that supported the excellent success and cooperation between Naini and Valmet.
“In this project we were able to utilize our very strong presence in India and our local supply capabilities, which we of course combined with our state-of-the-art fiber processing and kraft recovery technology. And perhaps most important of all is the world-class technical knowledge that Valmet’s experts possess to get the equipment started and keep it running smoothly and profitably.”
The upgrade to 370 bdt/d includes batch cooking and fiberline equipment from Valmet with a digester plant consisting of four conical bottom digesters, and a fiberline comprised of eight Valmet TwinRoll presses, screen room, a 4-stage bleach plant, MC pumps, mixers and tower scrapers, as well as the basic engineering and site services. The recausticizing delivery also includes the OptiDisc™ WL unit, mentioned earlier.
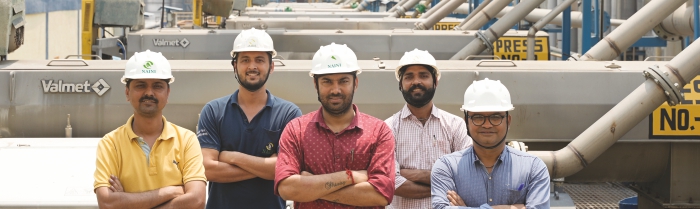
The new long wet lime kiln has a design capacity of 200 tons per day, with a chain system for drying of the lime mud inside the kiln. The kiln has a burner system designed for either firing producer gas in combination with furnace oil or alternatively firing 100% furnace oil. Producer gas is a low temperature, low grade gas produced in a coal gasifier.
Reliability is the Biggest Benefit
Mr. Agarwal, Managing Director, considers reliability to be the best benefit that Valmet’s machinery brings. “I must say the reliability of the equipment is impressive. The uptime is good and fortunately we haven’t had any big shutdowns, nor any big maintenance issues. The overall technology is well proven, and Valmet is continuously making improvements on this technology, and it shows.”
Covid challenges were, as one would expect, a hindrance during the execution phase, especially the commissioning. But Valmet and Naini together devised a plan for having regular online meetings, which fortunately had matured by that time, allowing the teams to interact closely on each and every issue, not physically but online. There were some hiccups but nevertheless the start-up was smooth, says Mr. Agarwal.
“We really didn’t feel that we were missing the physical presence of Valmet team, because of those frequent online meetings. And I would like to emphasize that Valmet was always very supportive whenever we asked for a meeting, they were there, and we were never asked to wait or delay a particular process. So, it was quite smooth and covered so many things, and exciting to commission such a big plant online, with online support.”
Also Read: Star Paper Mills Plans for Technological Upgrades and Capacity Enhancements
Automation keeps Fiberline Running Well
“We have had very good experiences with the new cooking plant. It started with zero spillage and no problems with pulp quality,” says Mr. Kuldeep Maheshwari, General Manager – Fiberline. “We feel that the preheating of the chips was a key factor that helped a lot in giving uniform pulp cooking and quality. We really haven’t had any big challenges in the cooking plant, it is running well.
Automation on the fiberline has played a very valuable role in the operations as well. From day one full automation has been used and helped with the smooth commissioning. “The automation has been extremely beneficial and from the beginning we have run on 100% automation, which is great. And when needed we of course had support from the Valmet team which were always ready to help us.
Naini Papers Installing a New PM as well!
The Naini Group of Industries was founded in 1982 and Naini Papers started in 1995. It is one of the few premier paper manufacturing facilities in India, offering high quality writing and printing papers with excellent physical and optical properties.
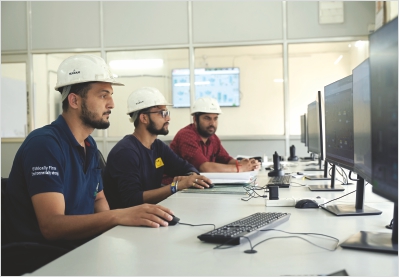
The company has recently ordered a new specialty paper machine, PM 3, from Valmet. Like the fiberline, PM 3 will also be state-of-the-art machinery with some new technology being put in place. The paper machine project is ongoing, and commercial production is expected to start sometime in March 2025, says Mr. Agarwal.
Naini Papers’ MD concludes by again praising the smooth start up of the BHK pulp line. “I must say that the start up was beyond our imaginations. I remember I was travelling from London to Delhi, and I was in touch with my team at 23.30 o’clock when they started the fiber line. And at 02.00 o’clock we were making good pulp. It couldn’t be any smoother than that.