Shreyans Industries Limited, one of the first agro-based mills in India, has come a long way since 1979 in perfecting the agro-based papermaking technology through continuous, step-wise technology modernization efforts.
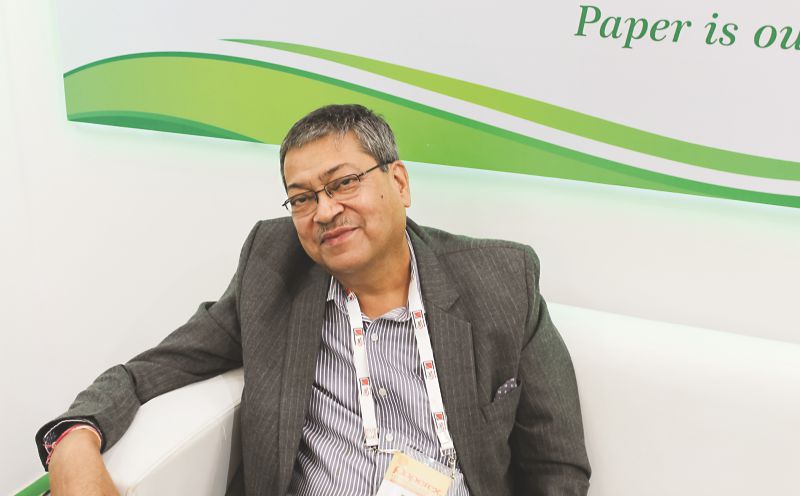
The company has two paper manufacturing units located at Ahmedgarh and Banah in the state of Punjab. Over the years, the mill has undergone a number of modernization-cum-expansion schemes to manufacture good quality writing & printing paper from agro-based raw materials. Paper Mart recently interacted with Mr. Anil Kumar, Executive Director & CEO, Shreyans Industries Limited to have his views on how Shreyans has been able to stay in competition over a course of time. Mr. Kumar also expressed what environmental compliance means to a mill like Shreyans and covered other topics such as the prospective growth of the industry and the effects of paper imports on the Indian market. Excerpts:
Paper Mart: Being an agro-based mill, Shreyans has never shied away from investing in right technology at right time. Tell us a short story of your technological journey as a paper maker.
Anil Kumar: As far as technology is concerned, we have come a long way from starting with an imported, second-hand machine, which was chain-driven and with open head-box. We had a management, which was always keen on technology upgrdation but was shackled with economic constraints, which necessitated small, stepwise improvement.
We started from changing the chain drive to geared drive and to silent drive ultimately. Most of the machines, especially the small machines, were equipped with open draw system between wire and press section. We were one of the first in small agro based mills to go in for a bi-nip press system thus closing the draw between these sections. This modification was carried out by M/s Servall Engineering in collaboration with Holder Pamac of UK. Simultaneously, we replaced our open head box by a pressurized head box supplied by an indigenous supplier. This modernization which we took in 1988-90 helped to speed up the machine to 350 m/minute from a mere 130 m/minute, inspiring us to continue further in this direction.
In Pulping Section also conventional rotary spherical digesters were used for batch pulping of straw. The entire system was very labour intensive resulted in uneven cooking from batch to batch due to basic nature of operations. Continuous digester technology was available for different raw materials but was never tried on wheat straw and otherwise also most of the suppliers were Europe based and cost of continuous digester was prohibitive. We, once again, partnered with a local supplier and put up first successful running continuous digester on wheat straw which changed the way straw pulping was done in the country.
On the effluent side, Shreyans from the first day had the best possible ETP in place. When the system proved inadequate with the growth of the mill, we upgraded it by using technology from NEERI [National Environmental Engineering Research Institute].
All agro based paper mills in the country were set up without a chemical recovery system with a belief that chemical recovery system is not possible for straw based black liquor. This position was also accepted by the authorities. However, due to very high pollution load where entire black liquor was going along with the effluent, the final treatment was very difficult, if not impossible. Gradually pressure from Government agencies was building up on these mills and there was even a talk of closing all agro based mills in absence of a suitable chemical recovery system.
We were approached by an indigenous supplier with a proposal that one Ender’s Process technology has been developed in USA, which is running in a few bagasse based mills but has never been tried in a wheat straw based mill. This technology could be imported into the country and USAID is willing to support the transfer of technology. Shreyans took a lead and first ever successfully running chemical recovery system was set up in the year 1995-96. There were lots of teething problems faced by us and we were discouraged by a few technocrats who believed that this system would be a failure. We made certain technical changes in the technology and also set up a raw material wet cleaning plant where certain contrary chemicals like chloride in wheat straw could be washed away and the technology became a success. This technology has become a mainstay for many of small sized agro based mills in the country who have replicated our experience.
Our philosophy has been to keep on doing something, taking small steps, which we can afford and which if fail we wouldn’t regret. This would not become a do or die kind of a situation, and we could always go back to what we were doing earlier. I was lucky to have an extremely good technical and stable team. We are not the best paymasters, but we are a good employer. As a result, we have people, right from workers to staff, working with us for more than 30 years.
PM: Did Shreyans apply the same kind of continued improvement on the product front as it did on technology front? What products made you click from time to time?
AK: When Shreyans started, agro-based paper making was an entirely new thing, never tried before anywhere. The Western countries never used agro-residues. There were few examples in China, but for India, it was a new concept born rather out of a compulsion than just a choice. We were short of forest resources and recycling then was not very common in the absence of deinking technology. It was a compulsion to use alternate fibers. The technology however was very raw and nascent, and it only evolved over a period of time.
I would like to share a very interesting statistics prepared by a very well known consultant. When we set up the plant, a yield of 32 percent was the norm given in that particular project report, i.e. each tonne of straw giving a yield of 320 kg pulp. Gradually, bettering the norm, we have reached at a level of 46 percent yield, which many for some time thought as false claim, but which has now become a general norm for agro-based mills. Credit of course goes to Shreyans as the first mill to go up to that level. Even a wood pulp based mill could not claim 46 percent fiber yield on a bleached variety.
On the product development side, the steps in quality improvement have been continuous but saying categorically would be difficult as most of our paper goes without any specific brand name into the market, the overall brand being only Shreyans. First major step however was shifting from normal cream wove to high bright paper, which became very popular in the market. In the next step, we thought of the surface-sized paper. Again, we had this in mind that spending large amount may not be possible for us on a size press. In 2016, we finally came up with surface-sized paper. Shreyans as a brand has very well been accepted.
PM: Please tell us about the USP of Shreyans Paper.
AK: Other than the product, my USP in the market is my fair dealing. You can talk to any of my dealers and they will invariably say that dealing with Shreyans has always been a pleasure for them. Our commercial deals are very fair. Most of our dealers don’t have to specially visit us to settle their account because there are no disputes involved. Besides, we keep our commitments. Irrespective of the market conditions, there is no backing out of the deal or prior commitments.
I think my competitors making better products with the increase in sizes and latest investments. But I think in totality, we give a much better package to our customers than the others.
PM: What is the mantra of retaining such a good technical team for a long time, some you say for over 30 years?
AK: When I was talking about the USP in sales and marketing, I think that applies to my manpower also. We have been a very excellent employer by being empathetic and making ourselves among one of our employees. We have workers who are with us from 1981-82 when Shreyans actually started operations; they joined us and retired from Shreyans only. People who have joined from other industries and have changed at least 5-6 jobs earlier also retired from Shreyans only. We treat them as a part of our family and treat them fairly. That’s the biggest USP.
The problem comes when a person feels that he has been cheated or treated unfairly. Besides, we have empowered our employees. That has led to our success as well. This technological implementation would not have been possible if our employees didn’t have the sense of security against the repercussions of the failure. Failures are kind of taken in good spirits. The employees are empowered to take the decisions. If they mean well then results would come. We are done away with the fear of failure in our organization.
PM: Amid prevailing market conditions, how has Shreyans performed in the last few years? Do you have any capacity or product expansion plan for the near term?
AK: Unfortunately, we have been situated in a location which has been declared as a dark zone as far as water availability is concerned. In Punjab, as you know, due to high agricultural pressure, especially the paddy crop, which is not a natural crop to the state, the groundwater situation has become very bad. Therefore, major expansions may not be possible. However, as done in past, Shreyans would continue taking small yet concrete steps towards upgrading technology and conserving water at the same time. Our water consumption level today is almost on the same level which has been proposed to be implemented two or three years down the line by Ministry of Environment.
We have two divisions and we keep on modifying machines to increase the speed and efficiency. In the last 3-4 years, the paper market has been good, which is even reflected in the margins. At the same time, quantum jump came to us by the installation of shoe press, the addition of the state-of-the-art head box, and changing the drive system where we could speed up the machine by almost 20 percent. Those have been the contributing factors. Besides, cutting down our processing cost and making our product more environment friendly have also been factors in improving our margins.
PM: How paper industry should take its stand on environment?
AK: There are two things. Firstly, no one can deny the pressure from the government. If you have to survive, you need to comply with the regulatory pressure. Personally, I would say, don’t manipulate your operations. Some people say that they are complying with the norms, which they are not actually. However, Shreyans’s philosophy has been that compliance means being truly compliant for attaining self-happiness or self-worth rather than being compliant just to satisfy regulators or others. It is easier to satisfy the regulator but it is difficult to satisfy the society around you. Suppose, my air pollution result on paper is showing that I am within the norms but my neighbor says that your smoke comes into our house, showing there is lack of actual compliance. Today, all my discharge parameters are significantly below the norms prescribed. Even all my effluent is used for irrigation and is not going into any water body. So, in a broader sense, I am water neutral, meaning the water I use is again used for irrigation.
PM: As imports have lately been a contentious issue, what is your take on it?
AK: We are living in a free world where you cannot restrict or ban imports. It is global village concept. But, yes, giving an undue advantage to a particular area who have inherent advantages over local conditions does harm us. Similarly, talking about the ASEAN countries, their cost of production is much lower because the fiber is cheaper, energy is cheaper, and interest cost is significantly lower – the three main ingredients going into the cost. It is a highly capital-intensive industry. On the top of it, they are suffering from overcapacity. They don’t have enough domestic usage. They have to export. The unbridled exports do result in dumping to some extent. You may say that most of the dumping is either in A4 size or in coated varieties, which may not have any direct effect on mills producing other verities. For example, we don’t produce any of these, so there is no direct impact on me. However, there is a cascading effect because if lots of A4 sizes come into the Indian market, the Indian manufacturers who are producing A4 may switch to some other variety, competing with the existing mills in that category.
Going back on FTA may not be possible however we may wish it as international conditions and our relations with ASEAN and many countries wouldn’t permit the government to do so. However, on the positive side, DIPP has recently mooted an idea that the A4 size paper sold in the country should be BIS marked. No paper should be sold without BIS mark. This might put a check on some shady imports because BIS mark has to be taken. Authorities are also looking into dumping of coated paper variety paper in the country and anti-dumping duty or safeguard duty is being mooted.
PM: What do you think on the growth of the paper industry?
AK: The paper industry in macro terms will keep on growing as there are growth drivers which are intact. For example, on packaging fronts, as manufacturing starts to pick up, it will lead to more packaging, and vice versa. E-tailing is I think the biggest driver for packaging. People are demanding better packaging for their products, not only the standard packaging. Packaging sector, of course, would be a big driver for the growth of the paper industry.
Tissue paper in terms of percentage could have much higher growth rate because base is quite small. Growth and printing and writing would have its own limitations because of more and more e-governance coming in force. Having said that the biggest driver for printing and writing sector would be education sector. If we have to achieve goal of education for all, significant portion of this journey would be through paper based education. Most of the schools in rural areas or small towns would remain paper based in their teaching, therefore, more and more note books and printed text books will be required. Otherwise also after having experimented that e-learning people have started realizing that retention power of students increases when education is being imparted through paper medium rather than e-medium. Considering these factors, the minimum growth of 3% to 4% in this sector will be there and steady for many years to come. Increase in A4 consumption is a natural outcome of e-governance and easy printability. We are lucky that paper industry on demand front is comfortably placed. All varieties put together, 1 million tonnes per year is an additional demand which is coming in. As far as we are concerned, we would love a leap in production, but we don’t have any such plans as of now.