The leading manufacturer of writing-printing and duplex board is eying the growing packaging paper segment with a new expansion project. The company is planning to venture into low GSM kraft paper at reasonable prices to serve the growing domestic and overseas market in the kraft segment.
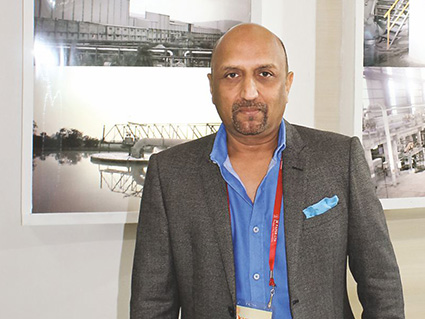
Mumbai-based NR Agarwal Industries Ltd, since its incorporation in 1993, has come to be one of the most recognized, recycled-based paper manufacturers in the western Indian region with four manufacturing units at Vapi and one unit at Sarigam in Gujarat. Paper Mart recently had an interaction with Mr. R.N. Agarwal, Chairman & Managing Director, NR Agarwal Industries Ltd. where he divulged his plan to possibly setup a new kraft paper unit. Mr. Agarwal also said few things on the need of continuous capacity addition in packaging, import being not a big deterrent for the paper industry’s growth, environmental compliance, and the prospects of growth in the packaging segment. Excerpts:
Paper Mart: We would like to know about some of the new or recent developments at N. R. Agarwal Industries.
R.N. Agarwal: We at the moment are producing 500 TPD of writing-printing and duplex board, grey-back and white-back, which is entirely recycled-based. Our existing combined capacity is 350,000 TPA. Besides, the company is envisaging a new 500 TPD kraft paper unit for which it already has surplus land. However, the project is still in its planning stage and would be finalized in the next 6 months in all probability. NRAIL has the entire infrastructure in place in terms of land and power as our existing captive power unit is capable of accommodating the needs of the new project. As per our estimates, if the company goes ahead with the project, the product would start by the end of 2019. After the expansion, our capacity would enhance to 500,000 TPA.
Overall, I feel the paper industry in the next 2-3 years is looking forward to some very good demand increase. Moreover, there are some changes in the Chinese market which have restricted their own production and curtailed their imports of some of the waste paper varieties which is good news for Indian waste paper consumer mills. Looking at all these factors, I am quite bullish about the paper industry for the coming years. With the future expansion plans, our ambition is to be among the top five paper mills in India.
PM: As you just said you are planning to start a new kraft paper project. Would you please brief us more about the project and the decision behind it?
RNA: As I mentioned earlier, the kraft project is being looked at as possibility and we would finalize on the same only in the next 6 months. The rationale behind considering kraft as an option is that I foresee a very good demand for packaging sector, especially the brown-grade because of the growing e-Commerce business and other growth drivers. We feel that we would be able to successfully market our paper. If we produce kraft paper, we will have a basket of three major products, i.e. duplex board, writing-printing, and kraft paper.
Currently, we are assessing the possibility and feasibility of scouting some Chinese machinery along with critical components to be sourced from Europe for the new project. Being in the paper business for the last 40 years has fetched us an extremely good in-house expertise. We therefore feel kraft would be a very easy entry for us as we are successfully producing duplex board and writing-printing.
PM: Are you comfortable with the kind of capacity addition which is happening in the multi-layered board or kraft paper?
RNA: I feel that India has got a tremendous growth potential and new capacities are only coming up to meet the demands generated by the growth. However, along with capacity expansion, efficiency is also important. Of course, only the efficient players will survive in longer run. Some of the units which are not efficient may face trouble surviving in this competitive environment. Further, I don’t feel that the capacities are so abundant that they will create a downward trend in the market. The additional capacities are getting absorbed by the simultaneous growth in the sector.
PM: What grades do you produce in writing-printing?
RNA: In writing-printing, we are producing three grades with brand names Classic, Maxima, and Excel. The Classic has a score of around 80 on the brightness scale, Maxima 85, and Excel 88-90. These are the three grades of Maplitho which we produce in writing-printing. We have yet not diversified into copier paper but may look at the same in due course.
PM: Energy and water conservation for large mills is an important issue, especially when the pressure is from the society as well as the governmental side is increasing every year. The readers would like to know your take on this.
RNA: We have always been conscious about the environment. Since the last 2-3 years, we have further enhanced our commitments towards the environment in view of the deteriorating quality of climate around the world made aware by various international climate summits and of course by the environmental norms being tightened in every nation. Also, with the alarming situation in China, one has to be more alert. Now everyone understands the salience of being environmental-friendly as the very survival will depend upon it.
We are now taking extra care and have allocated additional budget towards upgrading our technology and adding efficient equipments to ensure that our consumption in terms of power and water is reduced. We have invested in a very high-efficiency pump which has helped us curtail our power consumption. In fact, we are on the verge of commissioning the RO project in our writing-printing plant wherein we are aiming at cutting down at least 25 percent of our water consumption – not only less consumption but also less discharge. Subject to the successful implementation of the project, one day we will achieve zero discharge too in writing-printing. This will be a very big thing for us. Today, our water consumption for the wastepaper based industry is around 15 kl per tonne of paper, which I think is significantly low as compared to the overall paper industry. Our power consumption is 750 units, which again is very efficient number for a recycled-based mill.
We are situated in an industrial area and have the facility of discharging our water to a common effluent treatment plant. They in turn give it secondary treatment and discharge it to the sea. Our plant is very strategically situated and does not face issues in terms of pollution norms.. In spite of the discharge norms being at the level 1000, we are achieving a COD of 500. We are looking at achieving a COD of 250 and maybe discharging directly into the sea as well. That will reduce our cost along with being beneficial for the environment. We face less pollution compliance pressure compared to the agro-based or virgin-based mills but then looking at our recycled-based peers, we are making every effort to further reduce our water consumption and diligently stick to every discharge norm. In case of smoke and boiler emission, most of the units have been given SPM of 150, but we are discharging at an SPM of 50, which is the best figure for the air discharge norm.
PM: Import of late has become quite a contentious issue among the Indian pulp and paper industry stakeholders. What do you think on the matter?
RNA: The paper industry has always been competitive and has countered imports, be it writing-printing or any other segment. In the last six months or one year, definitely, there have been more imports. Yet, we have successfully been able to sell or compete with the price at which the imports are coming. Now, with this situation in China (the ban on waste paper import), there has been USD 40-60 increase in writing-printing or maplitho grades. Even in the copier segment, there has been some price increase. It’s not that imports are coming very cheap. I personally don’t think that import is going to be a big threat. We have to just be competitive and become efficient players to survive. If we are efficient, we will be able to compete with the import prices also.
PM: As your installed capacity and future capacity is going to be significantly based towards packaging, what is your outlook of the packaging sector in times to come and production requirements in the future?
RNA: As I said, there is already a sizeable packaging production. India is having a total production of around 14.5 million tonnes of paper out of which packaging sector constitutes almost 50 percent, which is around 7-7.5 million tonnes. The base is substantial and the growth is also going to be in tandem with the GDP growth which is around 7-8 percent, which with a little change of situation in China, might reach double digits as well. If you take an 8-10 percent growth based on 7-7.5 million tonnes, the overall packaging growth seems to be quite significant and would warrant a lot of capacities to be added up annually to serve the consequent demand.
In this situation of continuous capacity demand, whoever would be able to set up a plant or expand the existing ones at right time would take advantage of the good times, with the efficient players making additional profits. I feel there is good future for packaging. With the expansion of e-Commerce business, the kraft segment definitely will have further growth chances. The packaging sector’s growth is inevitable as packaging can’t be replaced by other things, and as biodegradable packaging material is picking growth, paper packaging will surely enjoy an edge over other materials.
PM: Is there any significant technological investment in the existing capacity?
RNA: The technological upgradation has been continuous. The deinking plant that we have in our new writing-printing project is the-state-of-the-art. We purchased it brand new from Voith. It has a drum pulper and special dispersals, which are not only efficient but give us very good quality. Hence, we are able to get near virgin quality pulp. Further, we continuously upgrade the technology in terms of pollution, energy saving, quality savings, and productivity enhancement. The paper industry in India is now adapting to internationally-acknowledged papermaking technology and has the potential to spend money to upgrade the same.
PM: Any plans for some product introduction in writing printing or any other grade?
RNA: We are currently not looking at any further expansion in the Writing Printing segment as we already converted our Newsprint unit into Writing Printing, thereby enhancing our WP production from 108000 TPA to 162000 TPA.
PM: Any new strategy on the market side?
RNA: We are exporting 10 percent of our products and I feel our export potential is much higher. NRAIL therefore is continuously looking for new markets. Earlier our exports were only to Sri Lanka and Gulf markets but now we are also catering to Africa and Europe with inquiries coming even from China. That way we are looking at new markets and new products continuously.
Our core has always been Paper. We would want to continuously expand and take advantage for the next 3-4 years, which are very bullish for the Paper Industry and all the players in the industry should be geared up for this.