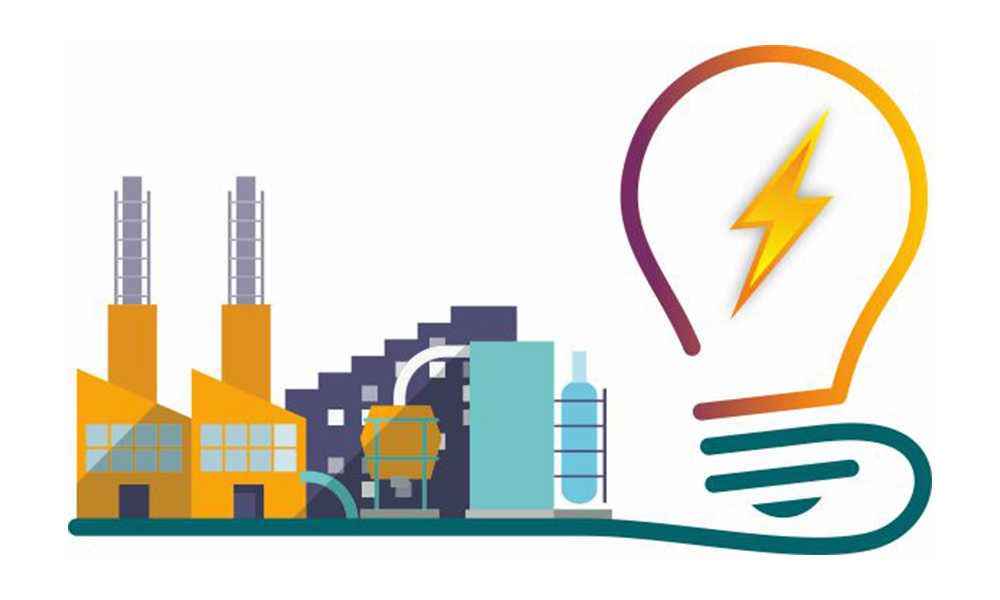
The fifth largest consumer of energy, the global pulp and paper industry accounts for 4 percent of the entire world’s energy use. In India, the average energy consumption of a typical paper mill is around 34.3 GJ/ton paper – that also includes energy consumption for wood chipping and pulping. There are around 800 pulp and paper mills in India.
Shortages in energy availability and increase in energy cost have heightened the need for energy conservation in the paper industry, but ushering in long-term energy-efficiency improvements in paper production calls for completely new process designs and processing techniques, which translates into new investments in energy efficiency projects – something that small paper mills cannot afford to make. Some of the big paper mills in India have gone for energy efficiency reductions because they know that energy constitutes around 16 percent of their total operating costs and that such reductions can make a big difference to their bottom line. They are also aware of the fact that investing in energy efficiency can yield considerable benefits from reduced water and associated chemical use, improving energy and water security for the plant.
Paper Mills in USA and Europe – Even Greater Energy Savings Are Possible
Through energy efficiency measures, pulp and paper mills in the USA and Europe are reducing their energy use even while increasing production. But that does not mean that further reduction of energy use is not possible. A case study was conducted by the University of Illinois at Chicago’s Energy Resources Center and Industrial Assessment Center. Energy assessments of ten paper and paperboard manufacturers in the Chicago metropolitan area were conducted to find out ways to conserve energy. In the study, each of the ten plants consumed both electricity and natural gas for powering primary manufacturing equipment, secondary support systems, and supplemental equipment. Energy usage among the then plants varied greatly, and was highly dependent on the product produced, age and condition of equipment, operating procedures and production orders. This study concluded that even greater energy savings are possible and that savings of up to 15 percent of a plant’s total energy budget are feasible. The seven energy-using systems that were examined – compressed air, motors, boilers/heating, steam leaks, waste heat, lighting and insulation – offered significant natural gas and electricity energy conservation and cost savings opportunities for all ten plants surveyed. Although the study focused on only ten plants, the energy-conserving opportunities it discovered can be implemented in pulp and paper plants across the globe.
To improve energy efficiency, the pulp and paper industry in the European Union has invested in combined heat and power (CHP) generation and – in Europe – now produces almost half the electrical energy it consumes. Due to efficiency improvements over the last 30 years, direct CO2 emissions have decreased while pulp and paper production has increased. Potential breakthrough technologies are being tested to demonstrate market viability and increase efficiency even further.
It may be mentioned that two main kinds of process are used to make pulp from virgin wood – chemical and mechanical. In Europe, about 18 percent of all mills produce both virgin pulp and paper on the same site. Integrated pulp and paper mills can be more efficient than stand-alone mills. Paper can also be made from recycled fibers. Europe has one of the highest recycling rates in the world (71.7 percent in 2012). In paper and paperboard production, the global average for recovered paper used by mills was 56 percent of total production in 2011, up from 46 percent in 2000.
Metsä Board – Fossil-Free Mills by 2030
Special mention must be made of the efforts Metsä Board is making to improve its energy efficiency. Metsä Board, a leading European producer of premium paperboards including folding boxboards, food service boards and white kraftliners, recently published its sustainability targets for 2030. One of the company’s targets is to achieve fossil-free mills by 2030 with zero fossil CO2 emissions. The target includes both emissions from the company’s own energy production and purchased energy. Currently, 82 percent of the energy used at Metsä Board mills is fossil free. Metsä Board is also aiming for a 30 percent reduction in water use per product tonne and a minimum of a 10 percent energy efficiency improvement by 2030 compared to the 2018 level. These will also play an important role in reaching the fossil-free-mills target.
Metsä Board has carried out a prefeasibility study on renewing the Husum pulp mill in Sweden in phases. In the first phase, the existing two old recovery boilers would be replaced with one new recovery boiler and the old turbines replaced with one new turbine. Metsä Board will launch a pre-engineering phase for the investment in recovery boiler, which includes the necessary regulatory processes, the technical design and a competitive tender for the main equipment. The planned investment in the recovery boiler will reduce the energy costs of the mill, improve the reliability of production and decrease the duration of the annual maintenance shutdown. Its own electricity generation, entirely based on renewable biomass, will double and increase the self-sufficiency in electricity of the integrate to over 80 per cent. In addition, the use of fossil oil in the integrate will reduce by approximately 5,000 tonnes per year.
Papermaking Technology
Over the years, papermaking technology has developed significantly in the western world. It has enabled paper manufacturers to make improvements in the quality and strength of printing paper. However, the higher energy requirements for producing these higher quality papers have reduced or offset some of the energy-efficiency gains. Notwithstanding, the industry is in a unique position to improve energy efficiency and reduce CO2 emissions – mainly because it already makes extensive use of biomass fuel and recycles heat energy to generate power. The industry could even become a significant supplier of energy – something that would facilitate the replacement of less efficient machines with new ones, which can be rather costly. Undoubtedly, boilers and the drying of the paper (the most energy-intensive part of paper production) are the main areas for improvement within a paper mill. The industry should focus mainly on finding ways and means of making its technology more energy efficient.
Paper Production and Energy Consumption in India
The consumption of steam and electricity per tonne of paper production in India is around 11 to 15 tonnes and around 1,300 to 1,700 kWh. The average specific energy is placed at around 50 GJ per tonne of paper, which is nearly twice the North American and Scandinavian standards.
The major factors that affect energy consumption in the Indian pulp and paper industry are low level of capacity utilization, quality and type of paper produced, number and multiplicity of machinery, paper machine runnability and down time, finishing losses, boiler type and pressure levels, level of cogeneration, and power generation.
The cost of energy is estimated to be 16 to 25 percent of the total production cost of paper, and the component of energy cost is expected to increase over other inputs in near future. Energy consumption in paper mills varies in accordance with the type of raw material and technology in use. Coal and electricity are the main sources of energy used in paper production.
The industry is likely to consume approximately 730 PJ per annum of energy in 2020 and 1702 PJ per annum in 2030. It is expected to contribute 76 million tCO2 per annum and 164 million tCO2 per annum of GHG emissions in 2020 and 2030, respectively.
The Indian paper industry has been able to reduce its energy consumption by 20 to 25 per cent in the last ten years or so. The reduction in energy and GHG emission intensity can be attributed to the adoption of energy efficiency measures in the industry and migration to advanced technologies in the process areas. Also, the Perform Achieve Trade (PAT) scheme of the Government has encouraged the industry to change. Tamil Nadu, for instance, now expects industry to use about 6 per cent of energy requirement from the solar-energy sector. But the need for greater energy efficiency still remains. To put it in the words of Sanjay Singh, Divisional Chief Executive, ITC PSPD, “while paper as a commodity will always be in demand in some form or the other, the focus has been to improve internal efficiency in production and bring down reliance on fossil fuels and focus on renewable energy.”
The pulp and paper industry in India must continue to focus on increasing energy efficiency, adopting the best available techniques (BAT), enhancing recycling and supporting R&D efforts to develop more efficient processes and technologies. The industry can contribute to sustainable energy supply as well. It can, for example, feed excess heat and electricity into the grid.
It may be mentioned that the concept of pulp mills as integrated biorefineries that produce low-carbon energy commodities – including bio fuels for transport – from Black Liquor alongside their pulping activities is steadily gaining in popularity. Many pilot projects are under way in this area. The pulp and paper industry in India has reported an improvement in energy efficiency, but is that enough? That is the question.
(The facts and figures appearing in this article have come from various studies, surveys and reports published in the last five to six years from now.)
Opportunities for Improvement in Energy EfficiencyTo meet the growing demand for paper, new capacity addition, efficient water management and improvement in energy efficiency are required. Energy-efficiency improvement is all about using less energy for producing the same amount of service or useful output without affecting the level of service or useful output itself. Let us take a look at the opportunities for improvement in energy efficiency. Installation of Shoe Press in Paper Machines: Shoe presses are able to press the sheet to very high dryness levels. Typically this means 4 to 7 points of dryness higher than the roll press it replaces. Shoe presses are able to preserve sheet bulk while pressing to high dryness values. Depending on the grade and press configuration, a shoe press can create dryness values 2 to 5 points higher than typical roll press configurations while maintaining bulk. Oxyfuel Burning in Lime Kiln and Black Liquor Boilers: Oxygen-enriched combustion increases efficiency and productivity. Installation of Extended Delignification System for Cooking of Wood: The latest technological advancements in pulping have led to the adoption of extended delignification pulping process. The extended delignification pulping process is energy efficient and environment friendly. Optimize Dispersion Energy According to Requirement: The fillings in a kneading disperger are much coarser than the fillings in a disk disperger. Control of the transferred dispersing energy for the kneading disperger is by adjusting the entering stock consistency. For the disk disperger energy control is by adjusting the spacing of the rotor/stator elements. A paper mill in India has reduced the energy input in the dispergers by installing disperger disks of less intensity. Installation of Centralized Compressed Air Generation System: Compressed air systems are one of the most expensive of all plant utilities. Most systems typically have efficiencies in the range of 15 to 25 percent. One of the ways of improving this efficiency is by the proper selection of the compressor for a particular application. Firing of Black Liquor at High Concentration: Most North American pulp mills fire liquor in the recovery boiler at dry solids level in the range of 68 to 75 percent. Valmet pioneered the concept of high solids firing where the dry solids level as fired in the recovery boiler is in the range of 78 to 85 percent. Many benefits come from firing higher solids liquor in a recovery boiler. Installation of Advanced Process Control Systems: Implementation of advanced process control technique is highly advantageous. The advance control techniques push the processes to their constraints and extract the maximum from the process unit without compromising on product quality and safety. For a model plant of 200 TPD, the savings that can be achieved are 1,947 MTOE. Installation of High Pressure Cogeneration Systems: The Indian pulp and paper industry has installed capacity for power generation of over 1500 MW. The combination of significant and steady process steam demand, high on-site electricity demand, high annual operating hours, and on-site generated fuels (i.e., wood waste and black liquor) has made Combined Heat and Power (CHP) an operationally and financially attractive option for many mills around the country. Despite the widespread use of CHP systems in the Indian pulp and paper industry (large and some medium mills) much potential for CHP remains. Installation of Back Pressure Turbine in Place of Pressure Reducing De-Superheated Steam: The back pressure turbine is used for supplying process steam to facilities in private-use power producers. This type of steam turbine supplies not only electricity but also the process steam to the facilities. Ultra-low Intensity Refining: With optimized refining, high quality products can be produced using less expensive fiber while reducing both chemical and energy usage. All short fibered pulps benefit from very low intensity refining, for both improved quality and energy efficiency. Low intensity refining also contributes to longer plate life, as each bar is subjected to lower refining forces, thereby reducing its wear rate. Optimizing Energy Consumption in Pressure Screens: Power consumption can be reduced by replacing centrifugal screens with pressure screens. As screening is done with 0.3 mm slot in the pressure screen, quality of screened pulp also improves as compared to that from centrifugal screen. Power consumption in a pressure screen can by reduced by changing the rotor with an energy-efficient rotor. Installation of Heat Pump/Chiller Heat Pump: Energy can be saved by installing vapor absorption heat pumps or chiller heat pumps. Optimizing Blow-Through Steam Consumption: Blow-through steam consumption can be optimized. Some of the valves leading the flash vapors to the heat exchanger are partially open. This creates loss of steam in the system, thereby increasing the steam consumption in the paper machine. Replace Vacuum Pumps with Vacuum Blowers: The efficiency of vacuum pumps is around 40 percent whereas that of vacuum blowers is around 60 percent. The replacement of vacuum pumps with vacuum blowers reduces energy consumption by about 40 percent. Bio-Methanation from Waste Water Discharge of Agro-Based Pulp Mill: The main sources of fiber based on agro feed stock are bagasse and wheat straw. Bagasse contains some residual sugar. Residual sugars and other biodegradable material can be used as a nutrient source for a particular type of microbes which release methane gas as part of their metabolic activity. Wheat straw wash water, which is bio degradable, produces methane gas when treated anaerobically. Methane gas, which has high calorific value, can be used as fuel in the boiler to produce steam and thus power from steam. This saves fuel used for making steam and power. Future Opportunities for Energy Saving Installation of Multiport Dryers to Reduce Steam Consumption in Paper Machines: Multiport dryers can increase paper production rates by 50 percent relative to conventional dryers and by 20 percent relative to dryers fitted with “spoiler bars.” This means that the multiport dryer technology offers paper mills advantages such as reduction of the number of dryers, higher production rate and reduction of energy costs through reduced steam pressure. Black Liquor Gasification: Black Liquor gasification is an emerging commercial technology with a long R&D history. This technology removes the biomass materials from black liquor by gasifying them in a high temperature chamber. Installation of Energy Monitoring System: Energy meters spread across the plant can be linked to one central computer. Real time monitoring of the energy use of any equipment can be done from one location. In addition, the system can generate reports in various forms of energy consumption pattern for any given period of time. The implemented system integrates the data of water consumption, amounts of different chemicals and other raw materials used. Trend patterns from the data stored in the computer system can be generated to evaluate the effects of any particular modification done in the plant. Use of Inorganic Fibrous Fillers in Paper Making to Increase Filler Loading Over 20 percent: It would be technically feasible to replace 40 percent pulp with 40 percent “fibrous fillers.” A mill can thus produce 200 tons/day paper by operating a 120 tons/day pulp mill and a 80 tons/day “fibrous filler” mill. This is compared with the case of 15 percent filler addition being currently practiced. |
“We saved 15 percent of the power we had been using by replacing our 15.5 MW steam turbine with an energy-efficient turbine of 18 MW,”
says M. B. S. Nair, Head (Strategy & Operations), Emami Paper Mills Ltd., Balasore, Orissa.
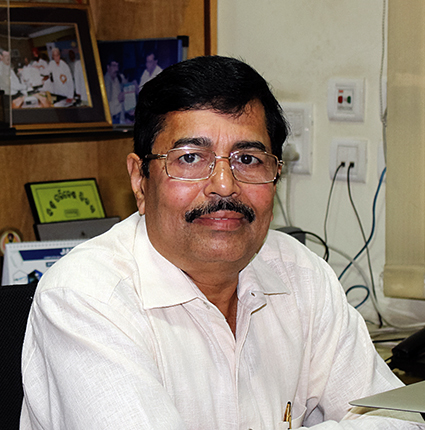
Emami Paper Mills Ltd., Balasore, Orissa.
Paper Mart: Can we regard energy – steam and electricity – as one of the biggest challenges that pulp and paper mills across the world, especially in India, are currently facing?
M. B. S. Nair: In my opinion, the biggest challenges for pulp and paper mills across the globe are:
•Availability of raw material,
•Availability of fresh water, and
•Availability of energy.
PM: What is the potential for energy use reduction in pulp and paper mills?
MBSN: All mills in India have been reducing their energy consumption every year. This is very clear from the data available with Bureau of Energy Efficiency (BEE).
PM: How can this potential energy use reduction be achieved?
MBSN: Further reductions are possible by using energy-efficient refiners, efficient vacuum pumps, and quality drives. But replacements demand substantial investments.
PM: What steps have you taken to reduce energy use in your mill?
MBSN: We have taken many steps to reduce our energy use. We have replaced our old equipment with energy-efficient equipment like vacuum pumps, pulp pumps, drives, etc. We saved 15 percent of the power we had been using by replacing our 15.5 MW steam turbine with an energy-efficient turbine of 18 MW.
PM: Which process in your mill is the largest consumer of energy? Can you name the processes where you have been successful in reducing energy use?
MBSN: The biggest consumers of power are vacuum pumps, drives, dispergers, pulpers, etc. I am delighted to tell you that we have achieved energy reductions in all these areas.
PM: According to a report published in The Hindu on July 18, 2013 (updated on November 27, 2017 ), “the paper industry has managed to bring down its energy consumption by about 20 percent in the last five years. From an average energy consumption of 1700 kWh per tonne, it has now come down to 1300 kWh per tonne.” Do you think the pulp and paper industry in India will see a further reduction in energy use in times to come? Please elaborate.
MBSN: The specific energy for paper production varies with the type of raw materials used – wood, bamboo, bagasse, straw and recycled waste paper – and the GSM. The specific power required for tissue production will be much different from the power required for graphic paper and packaging grades. So, it’s difficult to make a direct comparison. In the last five years, there has been 15 to 20 percent reduction in power use in the pulp and paper industry, greatly due to energy-efficient equipment.
PM: Tamil Nadu expects the industry to use about 6 percent of energy requirement from the solar energy sector. Can the pulp and paper industry across India go for solar energy in a big way?
MBSN: Solar installations are gaining momentum in different parts of our country, as the cost of capital is gradually coming down with technological advancements, especially for storing power (solar generation is limited to day time). However, the overall economics still needs to be improved for larger investments, especially in industries.
PM: Can we say that reduction of energy use in paper mills in the western world is greater than that in Indian paper mills? Do you think mill owners in India should follow in the footsteps of their counterparts in the West?
MBSN: Reduction of energy use in paper mills in the western world is not greater than that in Indian paper mills. By and large, energy reductions in India are on a par with those in the western world. But specific consumptions for smaller capacities are higher in India.
“Technological advancement in the western world is huge. But we are also looking forward to adopting some efficient and relevant technologies in near future,” says Jagdeep Hira, Business Head, Yash Papers Limited.
says Jagdeep Hira, Business Head, Yash Papers Limited.
Paper Mart: Can we regard energy – steam and electricity – as one of the biggest challenges that pulp and paper mills across the world, especially in India, are currently facing?

Yash Papers Limited.
Jagdeep Hira: Yes it’s a concern with regards to the huge component of conversion cost – to the tune of 15 to 17 percent. Having said that, we at Yash Papers don’t see it as a challenge. Instead, we look at it as something that gives us scope for reduction of production cost. Reduction of energy bill has been the subject of quite a few discussions for us. We have several options on bio fuel, but surely the capex has to be designed to handle such fuels so that we do not end up spending more on R&M cost and incidental losses.
PM: What is the potential for energy use reduction in pulp and paper mills?
JH: As mentioned earlier, the potential is huge. The major areas are mix of fuel, internal auxiliary power, condensate recovery, variable drive, and vacuum systems. The way out that team Yash has evolved is reduction at source itself.
PM: How can this potential energy use reduction be achieved?
JH: We see major energy consumption in vacuum systems and refining. A well-designed vacuum system layout can be seen as one of the potential energy-reduction sources. New technologies in refining have cut half of the energy bill; similarly, some time back, innovation of refining aid enzymes led to drastic reduction. Again, adequate condensate recovery can be a great source of reduction. Collection of every drop of condensate is critical, and the company must focus on it.
PM: What steps have you taken to reduce energy use in your mill?
JH: On the capex front, we have installed a pallet-making plant for utilization of bagasse residue pith – to convert it into pallets and use it as fuel. Various initiatives on installation of VFD are underway. We have gone for fine bar disc adoption for refining, which has enabled us to reduce energy use drastically. We have also gone for strength aid additives for energy reduction in refining, and installation of MC pumps and micro plate settlers for water clarification at source to reduce our energy bill for effluent treatment.
PM: Which process in your mill is the largest consumer of energy? Can you name the processes where you have been successful in reducing energy use?
JH: Paper machines are big energy guzzlers. At refining, we have been able to drastically reduce our energy bill through the systems we have adopted; for example, switching over to fine bar selection. We have also used strength additives to compensate on refining. In addition, optimization of speed and pipeline layout has resulted in reduced energy consumption. Further actions have been planned for higher gravity dewatering and higher nip-load dewatering.
PM: According to a report published in The Hindu on July 18, 2013 (updated on November 27, 2017 ), “the paper industry has managed to bring down its energy consumption by about 20 percent in the last five years. From an average energy consumption of 1700 kWh per tonne, it has now come down to 1300 kWh per tonne.” Do you think the pulp and paper industry in India will see a further reduction in energy use in times to come? Please elaborate.
JH: Yes, it’s true. Mills are efficiently operating at 15 to 17 percent and even lesser. Initiatives launched across the pulp and paper industry are looking at a figure below 12 percent. Our target is the same. With these figures, we see net energy consumption below 1100 kWH/MT.
PM: Tamil Nadu expects the industry to use about 6 percent of energy requirement from the solar energy sector. Can the pulp and paper industry across India go for solar energy in a big way?
JH: We have evaluated this at length; and for auxiliary power requirement like lighting and cooling, this surely is energy conservation. For continuous operations, huge battery banks are required, which would prove to be a heavy capex and unviable as compared to the cost of bio fuel. Adding on energy is a two-way requirement: steam and power. The proposal is still under evaluation. It will partly supplement the cogen plant but probably may not eliminate need for steam generation.
PM: Can we say that reduction of energy use in paper mills in the western world is greater than that in Indian paper mills? Do you think mill owners in India should follow in the footsteps of their counterparts in the West?
JH: Yes, it’s true, as technological advancement in the western world is huge. But we are also looking forward to adopting some efficient and relevant technologies in near future.
“The potential for reduction is very site specific. A world-class facility could be performing exceptionally well, while energy intensity increased slightly due to normal variation. However, most facilities can improve their energy intensity,”
says Mike Younis, Director of Energy Optimization for Georgia-Pacific’s Consumer Products Business.
Paper Mart: Can we regard energy – steam and electricity – as one of the biggest challenges that pulp and paper mills across the world are currently facing?
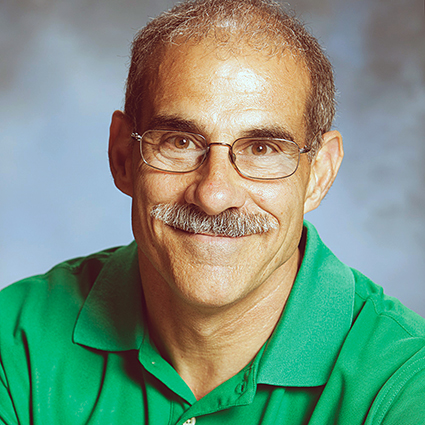
Georgia-Pacific’s Consumer Products Business.
Mike Younis: Energy is a challenge for the pulp and paper industry. In many cases, energy is the third highest driver of cost behind fiber and labor. The low natural gas price in the U.S. has actually made energy optimization more difficult to achieve due to the erosion of financial returns. However, there are other drivers for reducing energy use that must be considered. Much of society is concerned about greenhouse gas emissions. To maintain the right to operate in the communities, we must avoid excessive emissions. Customers are also responding to climate concerns. The Walmart Gigaton Challenge and Carbon Disclosure Project are just two examples of those concerns. Much of the energy consumed by the pulp and paper industry is biogenic. We need to optimize both the renewable energy inherent in our industry and purchased energy such as fuels and electrical power.
PM: What is the potential for energy use reduction in pulp and paper mills?
MY: The potential for reduction is very site specific. A world-class facility could be performing exceptionally well, while energy intensity increased slightly due to normal variation. However, most facilities can improve their energy intensity. In the last two years, three of Georgia-Pacific’s Consumer Products mills have been recognized by the U.S. Environmental Protection Agency’s ENERGY STAR® Challenge for Industry for 10 percent improvements in energy intensity (The mills are located in Palatka, Fla.; Green Bay, Wisc.; and Muskogee, Okla.). The challenge is a five-year commitment to improve energy intensity by 10 percent, discounting increases in volume. Therefore, with stable volume, many sites could improve energy consumption by 2 percent per year.
PM: How can this potential energy use reduction be achieved?
MY: All three of the Georgia-Pacific Consumer Products mills used different tactics to achieve the strategic goal of energy optimization. One mill executed a large capital project to replace four inefficient evaporators with one large efficient unit. A second plant used a combination of replacing a coal fired boiler with a natural gas unit, but the primary driver was an energy billing effort aligned with mill leadership organization that drove ownership of energy consumption. The third plant made a series of smaller investments and expense repairs to reduce the energy intensity.
PM: What steps have you taken to reduce energy use in your mill?
MY: We have used a wide variety of tactics to optimize our energy consumption including insulation surveys and repairs, LED lighting upgrades, boiler upgrades from coal to either natural gas or biomass, capital projects such as the evaporator, driving cultural change through energy billing by department, compressed air and steam leak repairs, steam trap upgrades, pump upgrades, etc.
PM: Which process in your mill is the largest consumer of energy? Can you name the processes where you have been successful in reducing energy use?
MY: We operate fully integrated mills, market pulp mills and recycled paper mills. Each type of mill faces challenges unique to their fiber sources, but the paper machines are energy-intensive operations at all the mills.
PM: The implementation of an energy conservation program frequently requires a change in the culture of a mill – cultural changes starting with senior management. Senior managers must be committed to the process, develop a sound plan of action, provide the leadership and secure the resources. The benefits from an energy conservation program will generally be derived from many smaller gains. Continuous effort is therefore required to retain the benefits long after the projects are implemented. Do you endorse this view? Please elaborate.
MY: I do agree that senior leadership is vital to the success of the effort, but developing the plan of action and securing the resources should be done by the energy leaders. An energy project with a solid financial and/or social return will be approved by senior leadership.
PM: Benchmarking enables senior management to compare the relative performance of their mills with similar mills or with a model mill. Do you think that benchmarking is one of the first steps a mill should undertake to implement an energy conservation program? Please elaborate.
MY: Benchmarking is an important element of energy optimization because it helps quantify the opportunity available to be captured. We are currently working with the Natural Resources Canada and an economics professor to create a benchmark for U.S./Canadian based recycle paper mills.
Additionally, here is some information on Georgia-Pacific’s recognition of energy optimization in recent years:
• Georgia-Pacific is the only paper company to earn EPA’s ENERGY STAR Challenge for Industry recognition – three of our sites have achieved the challenge: In 2018 (Palatka, Fla. and Green Bay, Wisc. mills) and 2019 (Muskogee, Okla. mill)
•Our Green Bay mill was recognized by Wisconsin Focus on Energy for Sustainability 2019
•We have earned ENERGY STAR Industrial Partner top project recognition for our Green Bay natural gas boiler – 2017, our Green Bay energy billing effort in 2018 and Naheola, Ala., biomass boiler in 2019.
“Considering the medium size (300,000 TPA of paper/paperboard production) integrated paper mills in India, there is potential for further reduction by 5 to 7 percent from the current level,”
says SVR. Krishnan, Executive Director (Operations), Tamil Nadu Newsprint and Papers Limited (TNPL).
Paper Mart: Can we regard energy – steam and electricity – as one of the biggest challenges that pulp and paper mills across the world, especially in India, are currently facing?
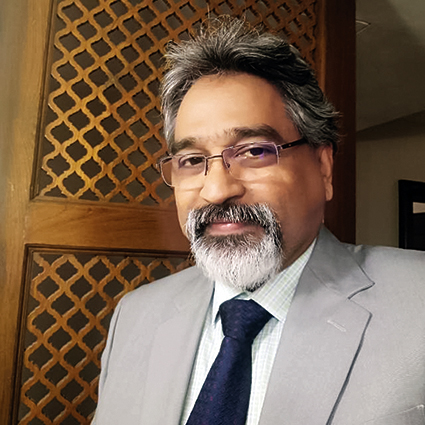
(Operations), Tamil Nadu Newsprint and
Papers Limited (TNPL).
SVR. Krishnan: Yes, steam and electricity are the biggest challenges for paper mills across the world, more so for India.
PM: What is the potential for energy use reduction in pulp and paper mills?
SVRK: It is difficult to answer this question, as we have too many paper mills, close to 800, of different capacities with different levels of infrastructure and automation. However, considering the medium size (300,000 TPA of paper/ paperboard production) integrated paper mills in the country, there is potential for further reduction by 5 to 7 percent from the current level.
PM: How can this potential energy-use reduction be achieved?
SVRK: It can be achieved by focusing on:
•Right designing of power boilers and turbines for the required electricity generation, thereby avoiding grid power/power import.
•The power boiler and turbine efficiencies, with minimum most or nil venting of steam.
•Right grade of coal with GCV and proper moisture content and optimizing the TG loads.
•Replacement of old/inefficient pumps and motors with new standard ones.
•Installing VFDs wherever applicable and huge fluctuations on load, etc.
•Frequent energy audits, with global benchmarking and deriving action plans.
PM: What steps have you taken to reduce energy use in your mill?
SVRK: The steps we have taken are:
• Steam and power cost reduced with the right grade of coal, lower specific consumption and improved the power boiler and TG efficiency.
• Idle running eliminated, staggered and timer-based operation for electrical systems/ for pumping systems/ for flow and level controls.
•IE3 motors for the new requirements and for replacing the existing ones in a phased manner.
•VFD in all possible areas, where the demand fluctuates for various grades and machine speeds.
•Timely replacement of the shower pipe nozzles and periodic replacement of the vacuum box tops.
•Refiner tackles modified for various furnishes for the lowest power consumption on the refiners.
• Replacement of individual vacuum pumps by turbo blowers.
•Machine clothing audit (on the drainage and the vacuum systems), steam and condensate audit for the Sp steam consumption and the maximum condensate recovery.
•Energy campaigns in the mills, by the senior management Team.
PM: Can you name the processes where you have been successful in reducing energy use?
SVRK: We have been successful in reducing energy use in the following areas:
•The paper machine vacuum system – with turbo blowers and periodic maintenance on the individual vacuum pumps, for the best vacuum factor.
•Stock preparation refiners areas – optimization of the refining (deg SR values) and the modification of the refiner plate pattern to reduce the load
• The paper machine electrical drives system – AC drives for the dryers, Dp calibration, condensate removal and recovery.
•Wet end of the paper machine – by tuning the process loops, for timely and faster response/control.
PM: According to a report published in The Hindu on July 18, 2013 (updated on November 27, 2017 ), “the paper industry has managed to bring down its energy consumption by about 20 percent in the last five years. From an average energy consumption of 1700 kWh per tonne, it has now come down to 1300 kWh per tonne.” Do you think the pulp and paper industry in India will see a further reduction in energy use in times to come? Please elaborate.
SVRK: Yes. The pulp and paper industry in India will see a further reduction in energy use:
•By leveraging more on the wind and solar energy for select application areas.
• Leveraging on the IT developments for the best utilization factor, for any process / equipment.
•Energy management teams are being formed and trainings are given to energy managers.
• Overall awareness is created.
•More and more mills are actively participating in the PAT cycle (Perform, Achieve and Trade).
•Getting rid of technological obsolescence and inefficient systems.
•Other than coal, alternate sources of fuel will be searched for – already research is going on.
•Effective usage of producer gas/ methane gas and gasification technologies to be in place.
•Recycling of process condensate and NCG in plants.
PM: Tamil Nadu expects the industry to use about 6 percent of energy requirement from the solar energy sector. Can the pulp and paper industry across India go for solar energy in a big way?
SVRK: Yes, but nor for the main high consumption areas. Paper mills can go for the solar power for ancillary applications / peripheral low consumption areas and for converting sections, etc. As land in India is vast and the climate is ideal for solar energy, paper mills have already started looking at this option for the future.
PM: Can we say that reduction of energy use in paper mills in the western world is greater than that in Indian paper mills? Do you think mill owners in India should follow in the footsteps of their counterparts in the West?
SVRK: We cannot compare mills in the western world with those in India. Here are the main reasons:
•The size and magnitude of the operations (ours is fragmented and small).
•Mill size is small/lower tonnage in Indian mills (even the biggest capacity is medium size mill in the western world).
•We have too many grades/ products and SKUs due to the highly fragmented printing and packaging industry (customers of paper mills).
•Western mills are standardized, and we lack standardization in processes and grades.
•The investments payback is faster for western mills just because of the size and volume of operations.
•Western mills have better infrastructure and the machines and equipment are most modern, especially in Europe and Scandinavian countries.
•Indian mill owners/proprietors have to work on the minimum tonnage production required for the scale of economy and to intervene on the technology front periodically. Ploughing back in paper mill operations is a must to stay contemporary.
“Scale of operation, technology, levels of automation, uniform raw material quality, and efficient operation are the contributing factors to lower energy consumption in western countries,”
says Ganesh Bhadti, Vice President Technical, Seshasayee Paper & Boards Ltd.
Paper Mart: Can we regard energy as one of the biggest challenges the pulp and paper industry is currently facing?
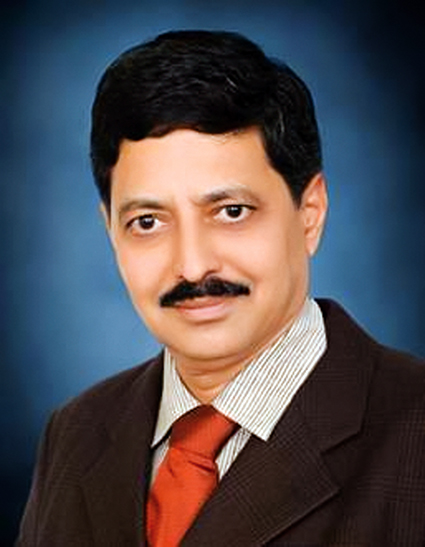
Seshasayee Paper & Boards Ltd.
Ganesh Bhadti: Certainly, yes! To meet the growth targets, the major requirements of the pulp and paper industry are:
•Technological upgradation
•Environmental compliance
•Raw material availability
Energy sustainability is also of paramount importance:
•The pulp and paper industry uses and produces a large amount of energy.
•The pulp and paper industry is the fourth largest consumer of energy in the world.
•Pulp mill spent wash Black Liquor is the fifth largest fuel used in the world; makes pulping inherently sustainable in terms of energy.
•Energy cost is 16 percent of the production cost (BREF 2010), and in some cases, up to 30 percent (CEPI 2012).
•Making energy the second highest cost factor after raw materials.
• Provide significant challenges that rise in fuel prices including biomass resources bring to the sector.
•75 to 85 percent used as process heat and 15 to 25 percent as electrical power.
For sustainable operation, managing the above are big challenges.
PM: What is the potential for energy use reduction in pulp and paper mills?
GB: As published by BEE, the national and international benchmarking is as follows:
•GAP in SSC compared to global is 4 kwH/Ton as against the Indian average.
•GAP in SPC compared to global is 300 kwH/Ton as against the Indian average.
PM: How can this potential energy use reduction be achieved ?
GB: It can be achieved in the following ways:
•Benchmarking with national or global best companies.
•Do gap analysis
•Devise an action plan to achieve the same.
•Practise TPM, participating in energy efficiency workshops, encouraging shop-floor engineers to participate in energy-efficiency summits to know and share the best practices.
•Vendor training programmes on restoring OEE.
PM: What steps have you taken to reduce energy efficiency in your mill?
GB: We have taken the following steps:
•To showcase top management commitment towards energy management, we have a separate energy policy.
•We have a dedicated energy cell headed by senior team members.
•Engaging energy efficient equipment suppliers to study and audit our system and efficient pieces of equipment are installed.
•Regular energy audits, gap identification and rectification.
•We will be discussing the daily energy consumption and deviations with concerning HOD on a day-to-day basis and CAPA are taken.
PM: Which process of your mill is the largest consumer of energy? Can you name the process where you have been successful in reducing energy?
GB: These areas are:
•Thermal consumer is Black Liquor evaporation plant.
•The main electrical consumer is paper machines.
•Our lime kiln runs on 100 percent HFO fuel. We have reduced around 15 percent of the total energy through a unique way wherein foul condensate along with bagasse pith filtrate is biologically treated to generate methane rich bio gas (65 percent) in an anaerobic lagoon.
PM: Do you think the pulp and paper industry in India will see a further reduction in energy use in times to come?
GB: Yes. There is a gap and we have to reduce energy.
PM: Tamil Nadu expects the industry to use about 6 percent of energy requirement from solar energy sector. Can pulp and paper mills across India go for solar energy in a big way?
GB: Yes. It is only beginning now, but expanding very fast.
•Solar energy use like light pipe, roof-top solar, solar day lighting, and solar water heaters are encouraged in admin buildings, offices, stores, godowns, and canteens of the pulp and paper industry.
•The integrated pulp and paper industry consumes more than 50 percent of the total energy through digester spent wash liquor which is renewable fuel, which makes pulp and paper production inherently sustainable.
•Making use of solar energy in a big way in the pulp and paper Industry requires huge pieces of land/ big rooftop areas. They are being explored.
PM: Can we say that reduction of energy use in paper mills in the western world is greater than that in Indian paper mills? Do you think mill owners in India should follow in the footsteps of their counterparts in the west?
GB: Agreed. Many factors are attributed to this difference in energy consumption. Scale of operation, technology, levels of automation, uniform raw material quality, and efficient operation are the contributing factors to lower energy consumption in western countries. More and more use of bio fuels, stringent norms and accordingly their practices are making them more efficient. In India, focus is now shifting towards making operations cleaner and greener. Technology developments, scale of operation, takeover of smaller mills by big players, and better plantation practices are making the Indian pulp and paper industry sustainable.