“TNPL is also in the process of finalising one more board machine of a similar capacity of 2,00,000 TPA and subsequently, a full-fledged BCTMP fiberline.”
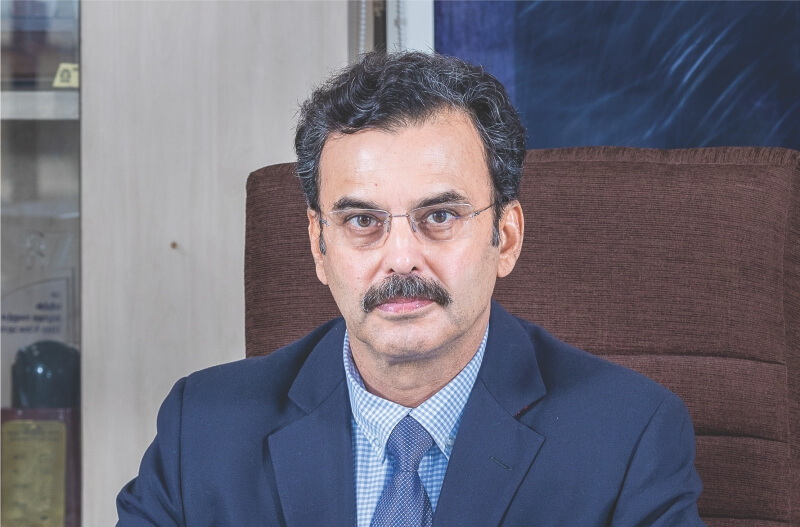
Tamil Nadu Newsprint & Papers Ltd. is an acknowledged leader in the technology of manufacturing paper from bagasse. Established in the 1980s, the company today enjoys the status of being the most environmentally benign mill in the country with the least water consumption. To further better the operation, it is continuously adopting modern technologies and moving towards digitalisation. In an exclusive interview with Paper Mart, Dr. Rajeev Ranjan (IAS), Chairman and Managing Director of Tamil Nadu Newsprint & Papers Ltd. talks about the company’s interesting history, manufacturing capabilities, and world-class technology.
Read Paper Mart’s June-July 2021 Issue.
Paper Mart: Could you please give us a brief outline of the business story of TNPL – Tamil Nadu Newsprint & Papers Ltd.?
Rajeev Ranjan: An adventurous journey started in 1984, when TNPL (Tamil Nadu Newsprint & Papers Ltd.), the first mill of its kind, to produce newsprint from sugarcane bagasse was set up. From a small beginning of 90,000 tonnes newsprint to 6,00,000 tonnes of paper & board, this mill has transformed into one of the largest, integrated industries in the Indian sub-continent after crossing many milestones over the years. Bagasse is continuing as one of the primary raw materials for producing quality papers. The company has ideated a plethora of innovative and outstanding technological developments to become what it is now. TNPL is the largest exporter of paper in India. We have a total production capacity of 6,00,000 TPA of paper and boards at present with an additional 2,00,000 TPA in the pipeline at our plant in Trichy.
PM: Please elaborate on the manufacturing capabilities of the company and the core competencies which have helped you in attaining substantial growth and carving your niche in the Indian paper industry.
RR: TNPL’s capacity includes 4,00,000 MT of printing and writing paper and 2,00,000 MT of multi-layer coated boards. The product mix consists of folding carton boards, recycled duplex boards, and cup stock baseboards. The core competency of TNPL is its adaptation of the latest technology and sustainability. TNPL excels in the selection of the best-in-class contemporary technology, with a clear focus on the delivered quality at competitive cost combined with the lowest water, and energy consumption.
“The core competency of TNPL is its adaptation of the latest technology and sustainability.”
The best technology, the most committed and passionate human asset with efficient monitoring & control systems are the pre-requisites for efficient manufacturing of quality products.
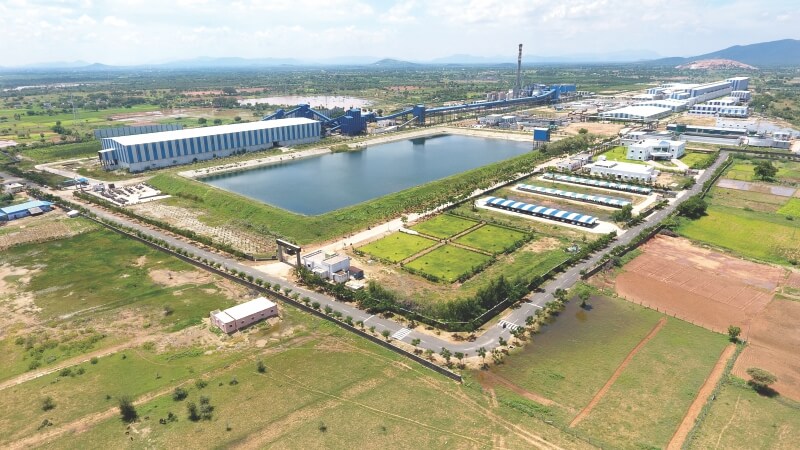
PM: How would you describe the key strengths of your product range? Also, could you please elaborate on the distinct features of the installed machinery and the different technological capabilities you have installed at your production facilities for the manufacturing of paperboards?
RR: TNPL products, be it paper or paperboards/packaging boards, are tailor-made for various end applications as required by the end users. We have three high-quality papermaking machines, supported by state-of-the-art fiber lines from hardwood and bagasse and a modern deinking plant with a three-loop system.
TNPL is equipped with 103 MW power generation and an elaborate effluent treatment facility in our Kagithapuram unit in Karur District and also a world class packaging board manufacturing facility in Trichy district. This Trichy plant is also going to become an integrated pulp & paperboard mill with Valmet fiberline, Andritz chemical recovery system, and the most modern effluent treatment facility.
We also have the Indian paper industry’s first in-house cement plant of 3.0 lakh TPA capacity. Its objective is to handle the solid wastes generated from the paper mills at both units. We have a total production capacity of 6,00,000 TPA currently with an additional 2,00,000 TPA in the pipeline at Trichy plant.
As we have hardwood, bagasse, deinked pulp along with imported BCTMP and softwood pulp grades, we have the flexibility to make different niche products for various Indian and overseas customers.
Our writing & printing papers have wide acceptability in the overseas market with the tag of ‘eco friendliness’ with the usage of bagasse in furnish. Our packaging boards made with the mix of all these fiber components deliver superior performance with respect to functional properties as required by different printing and converting processes.
We have the brand-new board machine from VOITH Germany, with the most modern technology. The machine is equipped with four forming wires (for making heavier grammages with a good formation of the layers), tandem shoe press (for preserving the bulk of the final board), speed flow, capable of running both starch and the pigmented colour, three auto controlled blade coaters (two for the top side and one for the backside of the board) giving the uniform coating thickness, in turn giving the best possible surface for achieving good smoothness & opacity. The most efficient soft nip calendaring gives the best printable surface and sheet gloss.
The company has the in-house capability for handling the total sheet volume with 5 milltex sheet cutters and 5 CHM cutters with the total production and quality control by the Mill personnel, ensuring the best possible delivered quality to all our customers, across the globe. TNPL is the only company having the auto storage and retrieval system for both the intermediate reel storage and finished goods. TNPL is also in the process of finalising one more board machine of a similar capacity of 2,00,000 TPA and subsequently, a full-fledged BCTMP fiberline.
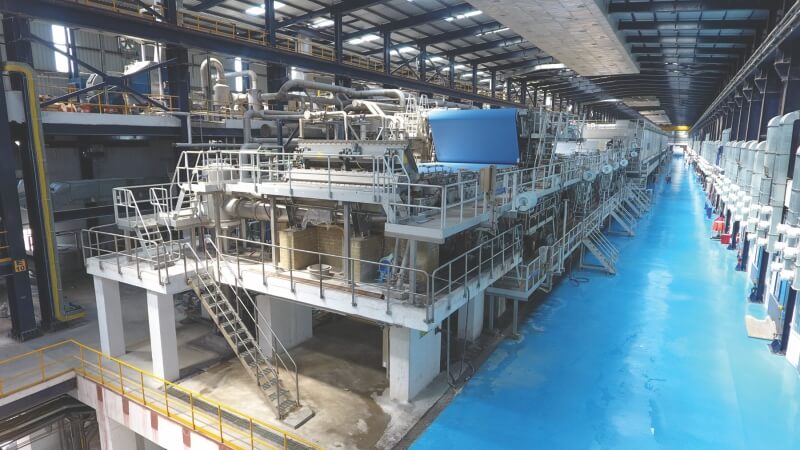
PM: Tell us the market outlook for various grades of paper.
RR: The Indian writing and printing paper market has enjoyed healthy growth rates of 5-6 percent per annum. Due to the current Covid pandemic, the writing and printing grade of paper is the most affected. However, the demand is expected to revive once the education sector opens up. India being a country with a large young population, the education segment continues to lead in the consumption of paper. The government’s focus towards 100 percent literacy is also pushing this.
Packaging grades of paper boards are growing at a very good pace with growth rates in the region of 10-15 percent per annum. Increased packaging intensity and high competition is leading to increased consumption in FMCG, packaged foods, consumer durables. Growth in e-commerce and online purchases is also fuelling demand.
In view of the focus on hygiene, demand for tissue papers has increased. In the days to come, this is expected to drive growth in this segment. The push from the government on banning single-use plastics is expected to drive the growth of eco-friendly paper-based products. Paper cups and paper-based food packaging will be another area of growth.
PM: Process efficiency is very important for any manufacturing company. Please share with us the technologies implemented and the kind of efforts made by TNPL on this front.
RR: Yes, process efficiency is the key metric for the overall standing of the company. The companies can buy world-class assets, but the same is to be maintained and utilised by the most competent workforce to produce world-class products, in a most competitive manner. The total workforce, workmen, and executives at all levels are well trained for the job and are given individual responsibilities in their respective areas. We have the best automation systems, from renowned vendors.
“The best technology, the most committed and passionate human asset with efficient monitoring & control systems are the pre-requisites for efficient manufacturing of quality products.”
Every piece of equipment is monitored for the OEE (Overall Equipment Effectiveness) on a daily basis, to improve the machine utilisation and to understand the repeated issues hampering the availability or the lower rate of production or defective output, for taking immediate actions.
The process, right from the chipping line to the packing line, is being covered under TNPL Branded ‘ME (Manufacturing Excellence) Program’, tailor-made and developed in-house, encapsulating the principles of ‘5S’, TPM – four major pillars and lean manufacturing. This was started in 2018, and going on well and people are getting on board. All the unit operations and the processes are covered under ‘ME’ for improving efficiency by involving all the shop floor people.
We also reward the workforce for the innovative suggestions, having tangible benefits through merit award schemes, and motivate them by promoting them to higher responsibilities for their vertical growth.
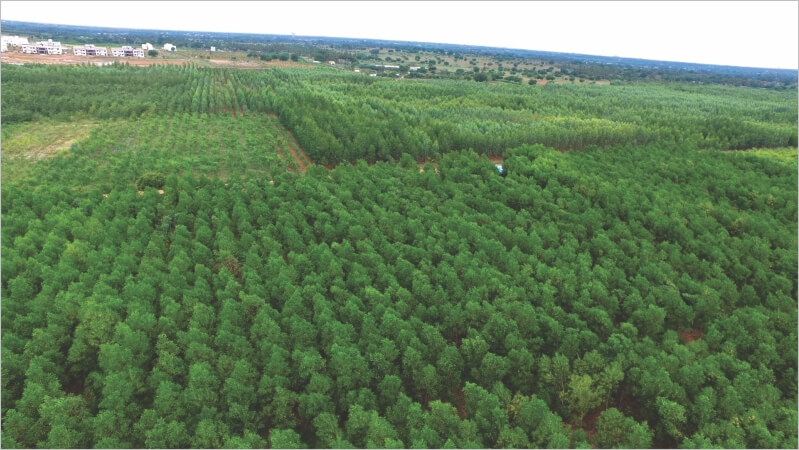
PM: What kind of technologies were implemented and efforts were made by TNPL to reduce the overall water consumption to one of the lowest in the Industry?
RR: TNPL has always been the front runner for a cleaner environment, especially concerning water/liquid pollution. Every area in the mill operation has been assigned a narrow band for water consumption on a daily basis and the same is monitored and acted upon.
We are extremely careful after the river Cauvery went dry in 2017 and the mill at Kagithapuram was badly impacted for a period of 5 months. Since then, we have intensified various measures to reduce the water consumption at the source. OEM companies are contacted periodically for the best water consumption levels, in various operations/departments and the gadgets to be installed on the machines. We ensure that the unmetered usage of water has been totally stopped and the mill wide campaign on the collection of waste and spillage water and put for reuse in the system, which is effectively implemented.
We have now started collecting the waste streams department-wise and studying for various cost-effective treatments, rather than mixing all the areas influent in the effluent treatment plant and trying to treat a much bigger volume. At TNPL, water usage and water treatment are always focussed, providing a lot more challenges and opportunities to improve further.
PM: TNPL became the first company in the country to procure about 1.5 million MT of pulpwood directly from farmers. Tell us more about your pro-afforestation schemes.
RR: TNPL uses predominantly bagasse supplemented with 35 percent of wood resources. The hardwood pulp mill at unit 1 needs annually around 0.5 million tonnes of pulpwood. However, the requirement will increase to 1.2 million tonnes of pulpwood per annum from the 3rd quarter of this year, once the commercial production of the new pulp mill starts at unit 2. In line with the National Forest Policy, TNPL initiated afforestation activities during the year 2004 with the motto of ‘Self-sufficiency and Sustainability’ by implementing two major schemes viz., farm forestry & captive plantation in the non-forest area through a people-centred participatory approaches, which is economically viable, socially acceptable and environmentally compatible.
The farm forestry programme is mainly for small and marginal farmers. TNPL provides them the quality planting material at a subsidized cost, free technical support, and buyback assurance with MSP and facilitates the harvesting and transportation of pulpwood from farm to mill. Captive plantation scheme is implemented in a large extent of barren land belonging to the government departments, temples, and absentee landlords either on a long-term lease basis or on a revenue-sharing basis. TNPL carries out the plantation establishment activities starting from land development, establishment & maintenance of plantation till harvesting the pulpwood and the yield is shared at an agreed ratio. The company has promoted plantations in 1,87,680 acres with the support of 35,962 farmers within Tamil Nadu under these two schemes during the past 17 years and continuing its afforestation programme with a yearly target of 25,000 acres.
The productivity of plantations depends on the quality of saplings used for planting. In order to enhance the productivity through the supply of quality plants to the farmers, TNPL has established state-of-the-art clonal propagation centres at both its units with an annual production capacity of 50 million plants. The site-specific high-yielding pulpwood clonal plants produced in these nurseries are being supplied to the farmers through three decentralized nurseries located nearer to planting areas. The company has produced 2502 lakh plants and supplied 2242 lakh plants to farmer’s fields over the past 17 years.
TNPL has also digitalised the establishment and monitoring activities of plantations by developing an exclusive mobile app with GPS mapping of all its plantations. TNPL is the first paper industry in the country that started direct procurement of pulpwood from the farmers without any intermediary from the year 2009 to ensure the maximum benefit to the farmers. Till now, the company has procured 1.80 million tonnes of pulpwood directly from farmers and paid over INR 700 crore directly to the farmer’s bank account.
TNPL has also proved its social and environmental responsibility by obtaining FSC (Forest Stewardship Council) certificates in forest management (FSC-FM) and Chain of Custody (FSC-CoC) for its plantations. With its trajectory pointing upwards, the scope for pulpwood plantation is on the rise and thus provides farmers with a sustainable market and generates employment for over 1 million man-days every year through its plantation activities.
An eco-friendly paper maker, TNPL has increased the green cover outside forest areas through its pro-afforestation schemes and improved the economy of both farmers as well as local communities by providing employment.
PM: Do you face any logistics challenges while sourcing fibrous raw materials? Tell us about your supply chain.
RR: Yes, we faced and are still facing a lot of challenges in logistics and for the fibrous raw material procurement. In the pandemic situation, especially in the last couple of quarters, the logistics for every raw material was so strained that only the container availability was the main topic of every meeting.
The varying pandemic intensity in various countries also played havoc in getting the raw material out of their factories. Vessel availability and the shipment schedule also gave a tough time. But one thing to share here is that all our vendors/suppliers have been cooperating with the company and doing their best, which helped us tremendously.
Regarding the virgin pulp grades, China was buying huge quantities from the Scandinavian countries, which has caused a shortage of virgin pulp grades in the global markets. In addition to this, some of the mills were shut either due to pandemic situations or maintenance activities. In the case of waste paper, global circulation has come down. The collection was also poor due to the pandemic but things are slowly improving now. This has also resulted in a huge price increase in various grades of pulp and waste paper.
It is also to be noted that it is not only the availability of the material and transportation in the supply chain that got disturbed, but also the unpredictable requirement for certain raw materials, chemicals, and key components/items in the supply chain due to sudden change in the marketplace, or strict lockdown in various parts of the country and across the globe.
Still, the lockdown is in force in various parts, of course with some relaxation. As the market is not yet fully opened up and the third wave (in October-November) is widely talked about, the challenges with respect to planning of the raw material and all the way through shipment would continue for some more time, till things get normalised, maybe towards the end of this calendar year.
PM: The biggest challenge faced by the Indian paper industry is the uncertainty regarding the availability of uniform raw materials. How do you cope with raw material supply chain issues, price volatility, and import challenges?
RR: As we are all aware, the supply chain involves manufacturers, dealers/agents, logistics support, and customers/consumers. Unfortunately, during this pandemic, every component of this chain is impacted. The prudent planning, forecasting, close networking with the dealers and customers, etc will certainly give better results, with respect to the raw material supplies/availability.
Planning of container loads, breakbulk shipments, and tie-up with various shipping lines and close coordination with the vendors and their agents have eased out the situation to some extent. Price volatility is a big issue for the companies while fighting for their very survival. Keeping minimum inventory with prudent planning and taking shorter runs based on the inventory and pull from the market and working with the local vendors for the JIT (Just In Time) and the VMI (Vendor Managed Inventory) is the fundamental norm today to keep the businesses afloat. Import consignments are being planned meticulously by keeping in mind the fluctuating prices of the pulp grades, chemicals, and other components. Various reports on the NET, RISI, and other price indices are all taken to have some forecasting and planning for 45 days cycle, rather than planning for a quarter as it used to be earlier. These are all explaining the term ”New Normal”.
PM: With the digital era taking over businesses everywhere, offices are claiming to ‘go paperless’ in the near future. As a paper company, how do you react to this hypothesis?
RR: Yes, digitalisation is here to stay but the paperless office might not be a reality. We will have a “less paper” office. Having said this, our young population coupled with the government’s focus on literacy will be the engine to drive paper consumption. Printing and the usage of paper will continue to be there, in varied applications like newspaper inserts, POP danglers, promotional items, etc. The consumption of A4 size paper increased in spite of the digitalisation process. India’s per capita consumption of paper is 13 kgs against the global average of 57 kgs. We still have a large room to grow. Paper is the most eco-friendly material and will continue to remain so. The form of paper usage will evolve based on the emerging trends. There will definitely be a shift from writing and printing towards packaging grades. We will have to identify the high-growth sectors and focus our energies on them.
PM: Any concluding thoughts that you wish to add to this interaction?
RR: Paper industry is really reeling under huge stress. Non-availability of raw materials, exorbitant cost escalation of key input materials, unstable paper market, stringent requirements of state pollution boards, import threats, and changing needs of the customers all together make this industry a difficult proposition for future generations. The government should support the paper industry and domestic consumers should not just admire the eco-friendliness but also support this by using eco-friendly papers.
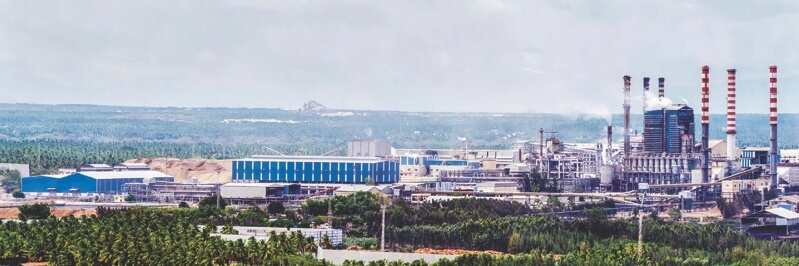