Many small and medium paper mills continue to manage the paper storage systems with traditional floor storage methods. Initially all mills were comfortable with manual storage system. However, when mills expanded to increase production capacities with greater product mix, most mills fail to re-look at the godown storage and dispatch concepts. This causes severe constraints in material handling resulting in complex operations. Even then the mills were wary of automated storage and retrieval systems (ASRS) due to high investment costs. With the current economic recession that has set in and its impact on the inventory of saleable paper, made it necessary to consider a much larger overall warehousing capacity. To effectively utilize the floor area through vertical stacking, possible way is to mechanize the ream stacking and retrieval operations by implementing ASRS. Further increased hourly in-feed & retrieval is envisaged and manual handling is a daunting task and cannot be accomplished.
In order to turn the focus of paper mills towards the importance of the storage system, team Paper Mart presents below the case study which was explored with Tamilnadu Newsprint & Papers Ltd. (TNPL) who added substantial capacity over the years. To counter the problem of less storage space they went in for ASRS to accommodate their product mix of more than 700 sku’s.
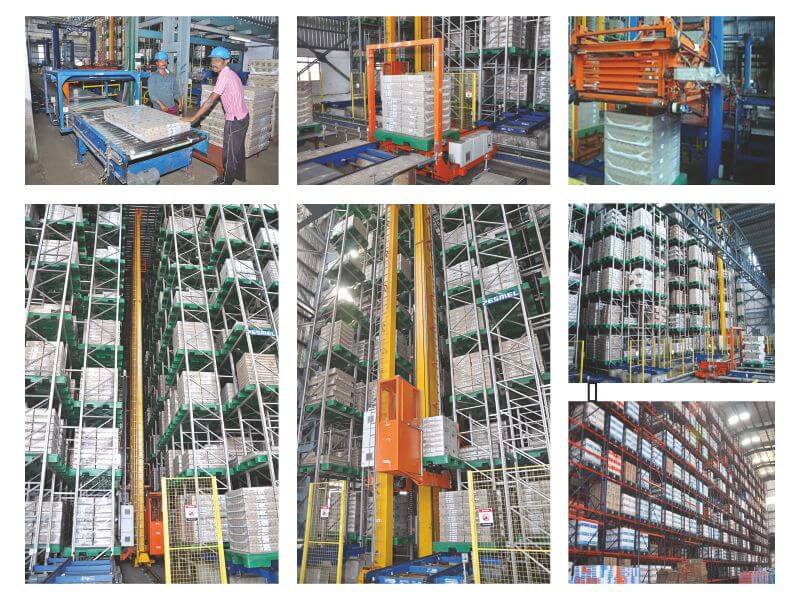
Initial Storage Process at Mill
Earlier the process adopted in the mill for the different product mix was as follows:
Copier – In the year 2005, the copier carton boxes and sheet bundles were stored by stacking on the sheet godown floor manually one over other. By manual storage method, the stacking could be done only upto 2 meters height. Though, the height of sheet godown building was 8 meters. By manual stacking the storage capacity was restricted to 500-600 MT. Further, the necessity to increase the copier boxes storage capacity was due to the increase in production of copier paper to 100,000 TPA and with the installation of an additional 200 TPD cut-size sheeting line for copier conversion.
Sheet Bundles – During the year 2008, the existing sheet godown space meant for storing reels, sheet bundles of PM1 and PM2 with storage capacity of 1,500 MT had to be relocated to accommodate installation of new paper machine (PM3) with capacity of 155,000 TPA. Especially when PM3 was designated to produce value added products, more sheet orders were likely to be serviced from this machine, in-line with the future demand for sheet fed offset printing. Manual handling of additional capacity was a daunting task and cannot be accomplished.
Sheets – Further to handle 100,000 TPA of estimated sheet production, there was need to have large area to store and handle different sheet bundle sizes. The sheets were wrapped manually and stored by stacking the bundles one over the other up to 2 meters height only. Stacking over and above 2 meters would damage the sheets in the lower part and by resorting to manual stacking only 0.75 MT of material could be stored per sqm of floor area, and would require more than 11,500 sqm to store 7,500 MT sheets.
Issues Faced
The mill production has gradually increased from 230,000 TPA in 2005 to 400,000 TPA of paper in 2011 with a break up of 200,000 MT in reels, 100,000 MT in sheets and 100,000 MT of copier. Due to progressive capacity build-up, TNPL faced high throughput situation in addition to shortage of space for storage. In addition to the high volume of production and throughput requirement, unlike in other paper mills the variations in the sheet products based on dimensions, quality, gsm, customers’ specific requirements etc. The numbers of stock keeping units in TNPL was more than 700, which make it totally unique and special and wherein it is humanly impossible to track, handle, store and also to retrieve. Moreover, operations became increasingly complex; market fluctuations made product storage challenging and availability of floor space for warehouse was limited. Every MT of copier or paper sheet bundle storage required 2-3 sqm of floor space & copier and paper sheet storage was becoming increasingly difficult.
ASRS – Solution Adopted
ASRS was being installed as a solution to offset the problem of storage system. The workflow of the solution that was adopted is as follows:
Operator feeds the bundles through the infeed conveyor of palletizer and barcode scanner reads the bundle barcode in the beginning. After reading barcode label WMS (warehouse management system) fetches data of bundle from mill ERP system. Conveyor moves boxes to the palletizer. Palletizer stacks bundle on SRP pallets as per loading pattern for particular bundle size. When pallet is ready it is moved to transfer car by chain conveyors. Profile checker checks pallet dimensions when it is being transported to transfer. If dimensions of pallet is not as per system requirement it will be rejected and send to reject conveyor.
If pallet is accepted by system then transfer car delivers the pallets at in-feeding conveyor of storage and stacker crane picks and stores pallet in racking position assigned by WMS. For retrieving pallet from storage, operator creates order for product to be retrieved. Based on order WMS generates tasks to retrieve the product and selects the item, which was stored first. The stacker crane picks pallet from racking and delivers on out feeding conveyor, transfer car picks the pallet and delivers on exit conveyor from where operator removes the pallet manually.
There are 4 aisles for the stacker cranes and there are 4 stacker cranes, which pick up the in feed pallets from in-feed conveyor and deliver the out-feed pallets to the out feed conveyors. The stacker cranes are literally moving and lifting as computers and have the memory to track all the pallets handled by them. Special task allotment could be made in such a way that the crane in-feeds the pallet and while returning is able to pick up the dispatch pallet to save time. This is possible due to optimization of the movements and enhancing the throughput and efficiency.
Mechanism/Features of ASRS
The ASRS consists of the four major mechanisms/concepts. They are:
• Storage function – that includes rack structures, storage modules and building.
• Pick up function – that includes input conveyor, palletizer and transfer car.
• Delivery function – that includes stacker cranes, output conveyors and pallet trucks.
• Warehouse management system (WMS) – that includes inventory control, location management, handling control, data exchange & integration – MIS, trouble shooting and report generation.
The major elements that form the part of the above mechanisms are:
Automatic Palletizers – Fully automated system for in feeding/out feeding of pallets. Bundles are fed to palletizers through conveyors and bundle bar code is read automatically. The bundles are stacked on pallet as per loading pattern for different sizes. The WMS ensures that the pallet is filled up full thus optimizing the operation without exceeding the boundary. Keeping in view that there are different sizes and types of bundles the palletizing is worked out mathematically matching the number of bundles and there area over the available area on the pallets.
Conveyors – Roller conveyors are used to move/feed bundles to palletizers, whereas chain conveyors are used to move pallets.
Transfer Cars – The main function of transfer car is picking and delivering pallet from storage and palletizer. The transfer trolleys become the bridge between the manual handling side and automatic handling ASRS and are designed to cope up with the throughput in addition to having the pallet configuration check device to avoid any projection of the bundles beyond the pallet which would not be fit for the storage in the ASRS.
Racking System – Racking structures are made from special rolled and roll form sections fabricated carefully so that the deflection are minimum and the modulus of rigidity is maximum.
Stacker Cranes – Double mast high speed stacker cranes are machines created for the automated storage of materials by automated movements, being able to travel the length of the aisles and elevate to the height of the warehouse. They store and retrieve material at great speed by driving and lifting simultaneously.
PLC Based Wireless Communication System – PLC’s are the main component of automation that receives and executes the tasks from WMS. Also exchange the data from stacker crane and transfer cars to WMS and mill computer system (MCS).
WMS Server and Clients – WMS server is the heart of ASRS that generates task for PLC and based on PLC feedback keeps record of pallet location and status. The main function of WMS is to track pallet and bundle ID, data exchange and integrated monitoring and troubleshooting and report generation.
Warehouse Management System (WMS) – WMS includes software like Simatic WinCC7.0 SCADA, Microsoft SQL server 2008 and Microsoft windows 2003 server standard edition R2.
Benefits of adopting ASRS over Conventional System
Overall Benefits
• Nearly 3.3 times savings in floor space.
• Less manpower.
• Assured safety and quality in operations.
• Higher throughput in-feed/hour and out-feed/hour.
• Automatic palletizing using kinematics rather than robots thus making the system easy to maintain and operate.
• Automatic storage and error free dispatch.
• Full freedom to store and retrieve according to the needs either with FIFO (first in first out or LIFO (last in first out).
• Easy tracking, quick dispatch possible, ready inventory data, better MIS.
• Part dispatch of the pallets and recycling the part pallets possible.
• Pallet configuration check at the trolleys before being loaded.
• Least deflection on the structures as per FEM norms.
• Stacker cranes effective as per FEM norms.
• Rejects of bundles at entry by tail gate system at in feed.
• Rejects of bundles at delivery end through loop conveyor possible.
• More safe operation as the whole area of ASRS is fenced and protected.
• Max efficiency with planned in-feed and dispatches.
• Multiple storages / retrieval and flexible high bay storage facilities.
• Maximum system availability and 98 – 100% reliability.
Besides, the ASRS with automatic palletization provide the following benefits:
• Uniform product quality with minimum possible damage to the product during handling.
• Round the clock operations with very high uptime.
• Automatic palletizing, feeding, storing and retrieval system with required throughput per hour for in-feed and dispatch.
• Organized computer controlled storage inventory that can be connected and controlled through mill information system, which offers aster and accurate customer service abilities & good production sorting abilities.
• Optimal, flexible and efficient space utilization that enables simplified mill processes with less handling needs.
• Increased selling by 10 -15% with an invoicing average of 7 days shorter during peak dispatch period.
• Minimizes the needed handling equipments & resources (less conveyors, trucks, and operators). The stacker crane can handle incoming and outgoing level height differences. No extra elevators needed.
• Fire safety – sprinkler system in the rack make precision extinguishing possible. In manual and crane storages, sprinklers in the ceiling, limits the storage height.
Conclusion
High bay vertical storage systems have unmatched capacity with smallest storage footprint compared to other alternatives. In line with the saying “Less is more”, ASRS with simplified layouts, have high operational efficiency. With limitless handling and sorting capacity, TNPL gained advantage in maximum storage capacities for copier & paper sheet bundles compared with other alternatives from the traditional storage systems. ASRS is a boon and becoming inevitable part of paper mills as it manages multiple grades/varieties, avoids material handling accidents, insuring highest turnovers of materials received and retrieved per hour, safe and reliable operations with modern warehouse management system which is manually unthinkable.