The well-themed conference juxtaposed fine speakers and even finer subjects on one of the most pressing issues worldwide, more so for the pulp and paper industry, i.e. water management and conservation through adoption of innovations and technologies.
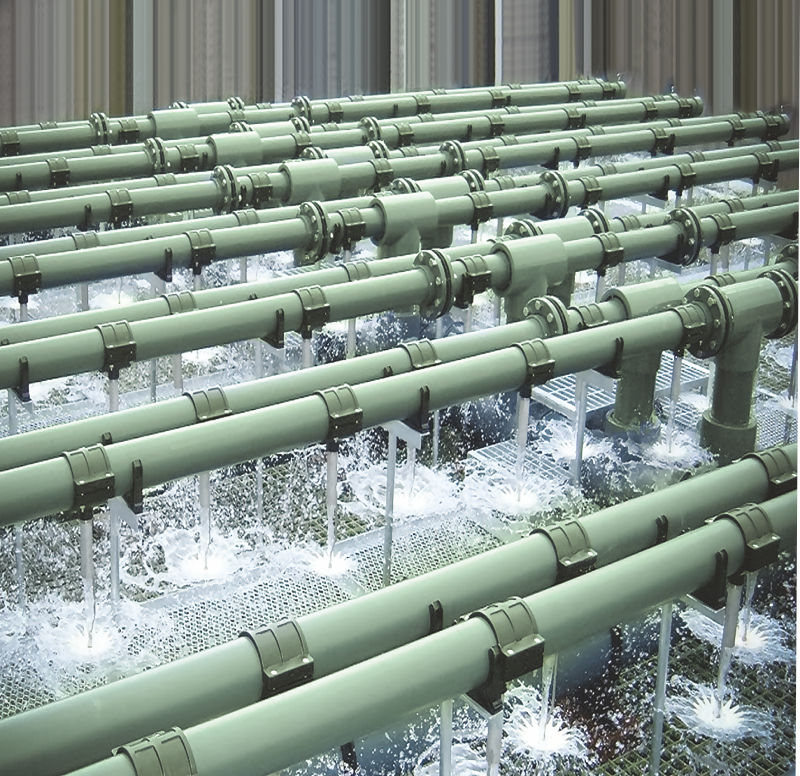
As a large water consumer, the Indian pulp and paper industry has been progressively improving its water usage and quality benchmarks as have been mandated by the regulatory bodies from time to time. Being water intensive industry amid the rising water scarcity concerns, its commitment to overall water conservation and management has now gone much beyond the regulatory expectations to embrace proactive understanding of the impacts of water use on environment. This new zeal of the industry has resulted in various innovative water management and conservation strategies on mill level and beyond.
Water concerns are now global and among the most pressing of issues, partly because of climate change and its impact on water bodies. As per facts retrieved from various surveys and research reports, less than 1 percent of the world’s water is easily accessible fresh water. Around 240 million people (roughly 20 percent of the world’s population of 1.2 billion people) lives in areas of physical water scarcity, while nearly another 25 percent (about 300 million) where it is very difficult to meet basic human and environmental water need owing to governments lacunae in technical, infrastructural, and funding abilities. Areas of physical water scarcity include a portion of the U.S. southwest and south-central areas, the border of Northern Africa, large portions of Asia and southeast Australia.
The Indian pulp and paper industry duly takes cognizance of this global water concern and acknowledges the fact that increasing population, urbanization, per capita demand, and pollution damage to supplies will put even greater pressure on the limited resources of water. The concern was manifest in the National Conference on “Innovative Water Management Strategies towards Enhancing Competitiveness of the Pulp & Paper Industry” organized by CII-Triveni Water Institute.
The conference was adequately represented by the majority of the industry and deliberations covered almost all the facets of water management and conservation; augmentation of technology and cleaner production initiatives; technological obsolescence and the lack of standardization in production processes; etc. Experts and panelists from the Govt., industry, third party organizations, and Central Pollution Control Board discussed volumes of issues pertaining to fresh water consumption, effluent generation, treated effluent discharge quality, commissioning of green technology for efficient water management, etc. The new national Charter for Water Recycling and Pollution Prevention in Pulp & Paper Industries w.e.f. April 2015 was also deliberated in detail wherein all the concerned parties tried to grasp the meaning of important norms to be met in short- and long-term.
Apt Theme, Apt Time
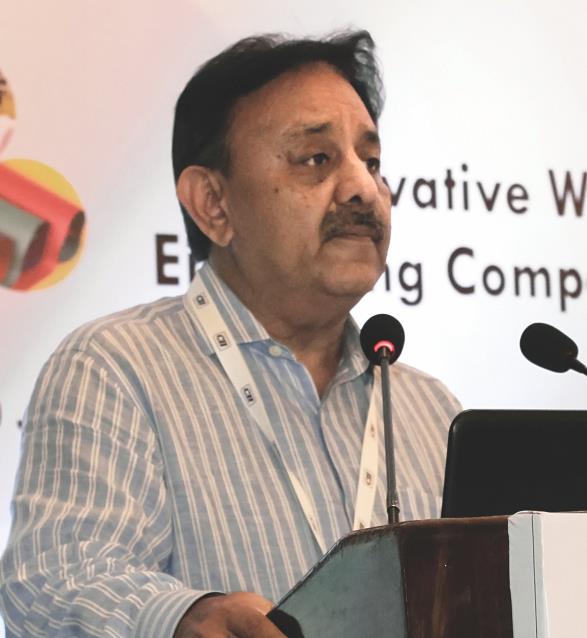
industry in addressing the water concerns saying
that the industry now needs to take these initiatives
beyond the mill boundaries. He sounded
positive on meeting the new water norms by CPCB.
“Few months back, I was a bit surprised when contacted by CII-Triveni Water Institute to preside over a conference with a theme ‘Innovative Water Management Strategies towards Enhancing Competitiveness of the Pulp & Paper Industry’. There could not have been a more apt time to convene such a session as the summer was just setting in and we had had two consecutive draught years with almost no or scanty rainfall,” said Mr. Sanjay Singh, Conference Chairman, and CEO of ITC – PSPD.
Mr. Singh shared his fears of depleting water level in rivers and overall water crisis amid irregular monsoon. He said, “All of us are worried, and we are more so as one of our mills is situated on the Godavari River. At times, we became so worried over the continued flow of the river that we would often send our engineers to measure the depth and breadth of the flow, and could be reassured only when they would say, ‘Don’t worry! The Godavari will continue flowing’. Fortunately, the river has continued to flow. We have often heard news that certain rivers had gone dry during summers and the dependent mills had to stop production because of water shortage.”
There was a time when large quantities of water and black liquor used to be spilled on the shop floor of the factories, and now through TPM route every drop of water, chemical, and black liquor is saved.
It is not that the pulp and paper industry has not taken any actions on recycling and reusing the water, yet enough emphasis has not been given to the source of water, said Mr. Singh. This would serve us good if we separately look into all the sources, viz. groundwater, river water, surface water, etc. and think of ways of managing them efficiently, he added.
Mr. Singh also said that the Indian paper industry took some time to understand the significance of water conservation and the quality of effluent discharged. “During my over three decades of activity in the industry, I have seen dramatic changes happening in the field of water conservation and management. There was a time when large quantities of water and black liquor used to be spilled on the shop floor of the factories, and now through TPM route every drop of water, chemical, and black liquor is saved. Not only does it give you some money back, but provides tremendous environmental benefits too,” said Mr. Singh.
He added, “There has been some really good work happening on the front of resource conservation and environmental compliances, still the paper industry has got this negative image of being the biggest polluter and user of water, energy, chemicals, etc. However, people don’t realize that in the last 30 years we have scaled high on saving parameters and brought down the water consumption considerably low from 200 cubic meter/tonne to 40-50 meter/tonne. And, now when the new national charter is going to have stricter norms, we as an industry would not be dithering about meeting theses norms exactly and timely.
“I can assure everybody on behalf of the entire pulp and paper industry that we are prepared, not just for now, but for many years to come as we realize the increasing pressure on environment due to increasing population.”
Mr. Singh also cautioned the industry from using makeshift or temporary arrangements in the name of technology, and urged them to invest in real technologies to have a sustainable future for the mill as well as the environment. He added that the process optimization through technology should not be limited to the mill, but the conservation and optimization processes should encompass the area beyond the mill boundary in terms of raw material procurement from forestry efforts, conservation of soil, and utilization of discharge water for agricultural purposes. He also emphasized the need to adopt social and farm forestry practices which not only will cut the need of imports, but would address environmental issues such as quality of air and rainfall.
Innovation and Competitiveness
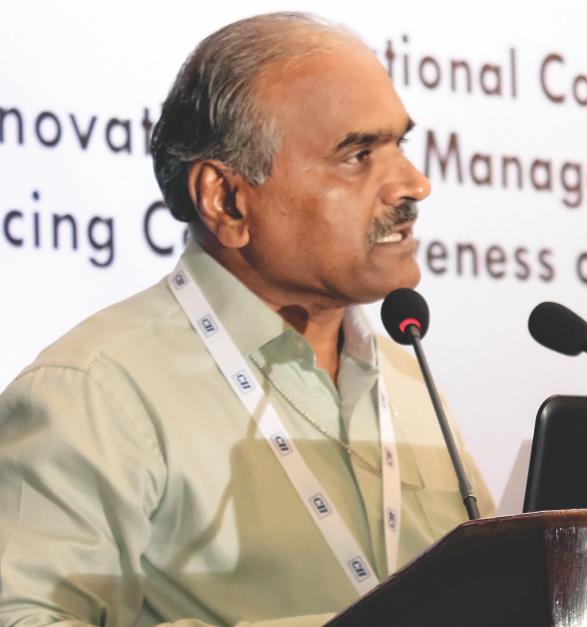
the theme of the conference and said it was
quite timely. Dr. Hota assured that Govt. would
reach standards and benchmarks only after the
due consultation with the industry stakeholders.
“The theme of the conference has two aspects, viz. innovative water management and enhancing competitiveness. The selection of the theme for the present conference could not have more precise and appropriate, especially when the country is struggling for water and we could not even see IPL in Mumbai as directed through judicial activism,” said Dr. Maoranjan Hota, Advisor, Ministry of Environment, Forest and Climate Change, Government of India.
He said that objective of today’s deliberation is finding ways as to how to manage water within and outside the industry, and still remain competitive and survive in the market. Competiveness is all about price and quality, and also competing with products in the international market. And, this kind of competitiveness cannot be attained without ours resorting to best and environmental friendly practices of production.
Mr. Hota expressed the willingness of the Govt. to work with the industry in making strategies for environment and resources management, including water for present instance. He said, “Hailing from the Ministry doesn’t make us act like your big-brother, or with some high-handedness in the matters under consideration. Since you are the people who develop technologies, implement it and knows better whether the said technology is appropriate, the Govt. must consider your inputs and opinions before framing any policy on a subject pertaining to your industry. The consultation is a vital part of policy formation and also a key for the Ministry in order to develop a particular set of standards.
“I still remember when we were discussing the new charter of 2015 by CPCB; the Ministry, CPCB, and industry stakeholders deliberated on the key components of charter related to recycling of effluents, zero liquid discharge (ZLD), how to reduce the effluent to maximum extent possible, etc. before agreeing on a benchmark.”
Mr. Hota also stressed that the pulp and paper industry must not resort to makeshift or provisional arrangements in the name of technology as many such things does more harm than good in long term. He said that the industry has to see whether the technology adopted by it is just provisional in nature, or would be viable for generations to come; today’s solution must not become a hazard for tomorrow.
He conveyed the concerns of citizens over environmental degradation and other related challenges and also their mistrust of the Govt. and the industry not doing anything to address these challenges. He said that this is upon us to convince public or citizen that concrete steps are being taken and results are also encouraging.
On the draft notification on the various standards for pulp and paper industry issued by the Ministry, Mr. Hota said, “We have notified the draft standards to the industry and I am sure people must have given their opinion, view and comments which of course will be considered duly before finalizing the standards acceptable to both of us, and citizens at large.”
Praiseworthy Efforts
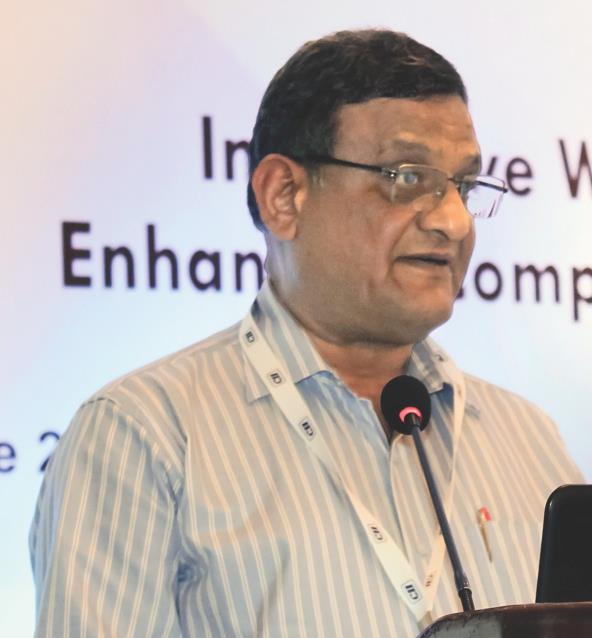
efforts by the Indian pulp and paper industry in
addressing water concerns resulting in considerable
improvement in usage pattern. Dr. Jain said
that despite all the challenges the industry had
posed a steady growth picture before the world.
“I would like to complement CII-Triveni Water Institute for taking this initiative which really is the need of the hour, especially when the Indian pulp and paper industry is struggling and making all out efforts for effective water management and conservation to achieve the norms for water usage as well as the parameters for the emission,” said Mr. R. K. Jain, Director, CPPRI, GOI. “In fact, the efforts of the Indian pulp and paper industry in this endeavor are indeed huge and I take this opportunity to place before this house a word of appreciation for efforts taken for water conservation by way of innovative technological advancements.”
In his address, Mr. Jain shared many facts and figures about the industry. He said, “There are around 800 paper mills in India with a production of around 15 million tonnes. Though the Indian pulp and paper industry contributes hardly 4 percent of world’s production, the growth of the industry is quite steady with an average rate of 6 percent, which is quite significant compared to the global average.
“Despite of various challenges and issues which the industry is confronting including raw material constraints; obsolesce of technology & lower scale of operation; environmental concerns in terms of public pressure, regulatory pressure, compliance to new charter norms, etc.; higher cost of basic inputs in the form of high cost of energy and high cost of raw material influencing competitiveness; and lack of skilled manpower, such kind of growth is only indicative of serious efforts gone in on all fronts of production processes.”
Underlining the criticality of water for the industry, Mr. Jain not only indicated the volume of water the industry consumes, but outlined the industry’s efforts in bringing down the water usage over the years. He said, “Paper Industry in general has been traditionally a ‘Water Intensive Industry’ both from point of view of consumption and discharge for the reasons such as use of mixed raw materials, low level of technology and equipments, lack of optimized process conditions, use of low capacity multiple paper machine, lack of reuse / recycling practice, low cost of water, etc. Paper Industry in India as of now consumes about 750 million tonnes water annually.
Hence, there is a need for synergy between paper industry, technological suppliers and technical institution to achieve minimum water footprint for paper making.
“The Indian pulp and paper industry has progressively brought down the consumption of water over a period of time as this is in the nature of industrial growth. Growth in the paper production and limited water resources restricts water consumption in the industry and calls for the adoption of ways and means to keep expanding the production process with constant water resources. And, the industry has done so quite remarkably – brought down the usage from 300 cubic meters per tonne of paper in 1960 to 70-80 cubic meters per tonne presently.
“The new charter prescribes further reduction to the extent of 50 cubic meters per tonne of finished paper (process water) and 40 cubic meters per tonne of finished paper (waste water). I am sure the industry will take it as challenge and try to meet the benchmark in due time with remarkable improvement in technology and optimization of processes. Of course, this is arduous task for mills having multiple machines with small capacities, but we will have to adopt the strategy of reduce, reuse and recycle.”
Mr. Jain described major areas of water consumption in pulp and paper mills and stressed on the need to look into each one separately to have overall reduction in consumption. Indicating towards the new charter norms of CPCB for fresh water consumption and waste water discharge, he said that locating the challenges in water consumption reduction would pave the way for their redressal. Increase in the concentration of TDS, chloride content and other pollutants in waste water; problems of scaling and slime growth due to system closure in paper machines; need to adopt the advance technologies to achieve the norm as prescribed by the charter are some of the challenges the industry would need to focus in order to meet the new charter norms, Mr. Jain said.
Elaborating more on the challenges in water conservation facing the industry, Mr. Jain said, “Stringent discharge norms compliance in itself is a major challenge, especially with regards to prescribed standards like BOD (< 20 mg/l), TDS (1800 & 1600 mg/l ), and Color ( 150 & 250 PCU). ZLD to river through land application has its own set of issues in the form of land availability, farmer acceptability, and disposal issue during lean period when there is no requirement of water for irrigation, whereas ZLD through system closure may have problems in terms of techno-economic feasibility of kidney technologies and disposal of mixed salts / concentrate.”
Mr. Jain also emphasized that the industry needs to tackle water conservation subject both through process modification and through reuse/recycle. According to him, in the process modification, the industry can try new generation washers, like pressure washers, diffusion washers, chemi or belt washers, twin roll press washers; use of ODL and ECF bleaching; use of efficient fiber recovery system; improving scale of operation; etc. For reuse/recycle, he suggested collection and segregation of colored and colorless water streams; collection and reuse of clear water from vaccuum/gland cooling; condensate collection for reuse as boiler feed water; reuse of paper machine back water; adoption of closed loop system; etc.
Among the strategies of water conservation, he highlighted process optimization and technology upgradation, ETP upgradation, and monitoring. He said that process optimization and technology upgradtion may happen by way of metering of daily/hourly fresh water consumption, unit wise quantification of fresh water consumption, water audit & balance, adoption of energy efficient and environment friendly technologies, incorporation of fibre recovery units, optimisation of paper machine nozzle dia, increased recycle and reuse through process improvement, strict metering of the water use and wastewater generation. Under ETP upgradation, assessment, augmentation and addition of tertiary treatment units for treatment of back water and treated mill effluent to make it suitable for discharge/ reuse/recycle may be tried. Moreover, he stressed the need of monitoring and self-awareness in optimizing the water conservation efforts and outcomes.
Concluding his remarks, Mr. Jain said, “Recovery of process water from waste water/back water involves application of combination of technologies as no single technology is applicable or adequate for different categories of paper industries. Hence, there is a need for synergy between paper industry, technological suppliers and technical institution to achieve minimum water footprint for paper making. The selection of technologies including advance kidney technologies depend upon the size of the mills, raw material used, volume of effluent and quality of product, so it is difficult to work out generic capital and operating cost.
“Moreover, there is a need for a Demo Scale Trial of combination of technologies, viz. Ultra-filtration Nano & Reverse Osmosis and Evaporation to evaluate the feasibility of ZLD in Indian Paper Industry. In the present scenario the only and the foremost requirement of the paper mills is to do strategic exercise to determine the opportunities for recycling and reuse of the process water and to set specific water consumption targets.”
The Industry Needs to Work on Mission Mode
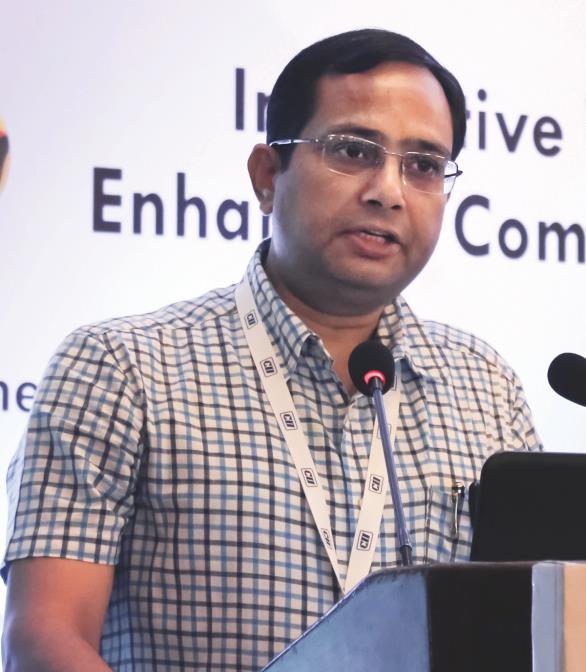
discussed in detail the norms of the new charter
on water recycling and pollution prevention in
pulp and paper industries. He explained how the
implementation will result in the sustainable
growth of the industry.
“For me, it is a great opportunity to share some of the initiatives that have been recently launched for water management and conservation in the Indian pulp and paper industry,” said Mr. A. K. Vidyarthi, Additional Director, Central Pollution Control Board. “The Indian paper industry is one of the important industrial sectors of the country and is also categorically considered one of the high water consuming industries because of its nature. The industry also has high water pollution potential.”
Citing the data from various CPCB surveys, Mr. Vidyarthi illustrated the water polluting potential of the industry. “As per CPCB survey conducted in 2007, out of estimated 236 MLD industrial effluent discharge into the river Ramganga, a tributary of the Ganga in Uttar Pradesh and Uttarakhand, about 185 MLD of contribution was estimated from the pulp and paper industry – roughly 78 percent of the total industrial discharge. This corresponds to 28 TPD of BOD load contribution from the pulp and paper sector out of total industrial BOD contribution of 36 TPD into the river Ramganga in Uttar Pradesh and Uttarakhand,” said Mr. Vidyarthi. “Similarly, out of 86 MLD industrial effluent discharge into the river East Kali, again a tributary of the Ganga, the pulp and paper sector’s contribution from Uttar Pradesh was estimated at 37 MLD, which is about 44 percent.”
Citing another such examples, Mr. Vidyarthi pressed the industry on the need to follow the principles of sustainable manufacturing and asked to respond to environmental concerns immediately. He also agreed to the fact that many paper mills in the last decade have implemented various projects on augmentation of technologies and cleaner production initiatives leading to better environmental performance. He however was of the opinion that the industry still needs to work in mission mode to ensure its sustainable growth.
“The industry needs to address the issue of technological obsolescence and the lack of standardization in production processes urgently,” he said. “Inspired by the successful implementation of PAT in 2003 and the charter for water recycling and pollution prevention in pulp and paper industries in the Ganga River Basin’ in five identified clusters of the industry located in Uttarakhand and Uttar Pradesh during 2012-13, CPCB formulated a national charter for water recycling and pollution prevention in pulp and paper industries in 2014-15. This new charter would be applicable for the entire pulp and paper industry in the country and would provide a more level playing field.”
Elaborating more on the new charter, he said, “Basic premise of industrial pollution abatement under the charter is based on participatory approach; benchmarking of the processes and waste-minimization/ cleaner production options; technology augmentation and process standardization; reduce, recycle and reuse of various streams without and with treatment (partial or full treatment) for different endpoint uses, i.e. cascade management of water utilization and wastewater management; end of pipe treatment for existing units with retrofitting of recycle and reuse options; effective and continuous monitoring program.”
CPCB formulated a national charter for water recycling and pollution prevention in pulp and paper industries in 2014-15. This new charter would be applicable for the entire pulp and paper industry in the country…
Mr. Vidyarthi said that the sustainable growth of any industry around the world is directly linked with the best available technology; the Indian paper industry should too adopt more efficient production system and state-of-the-art technology to meet the challenges in the way of sustainability. “The Charter suggests Bare Minimum Technology as an indication of the set of desired technologies or its appropriate alternatives generally considered essential to achieve the objectives of the charter,” he said.
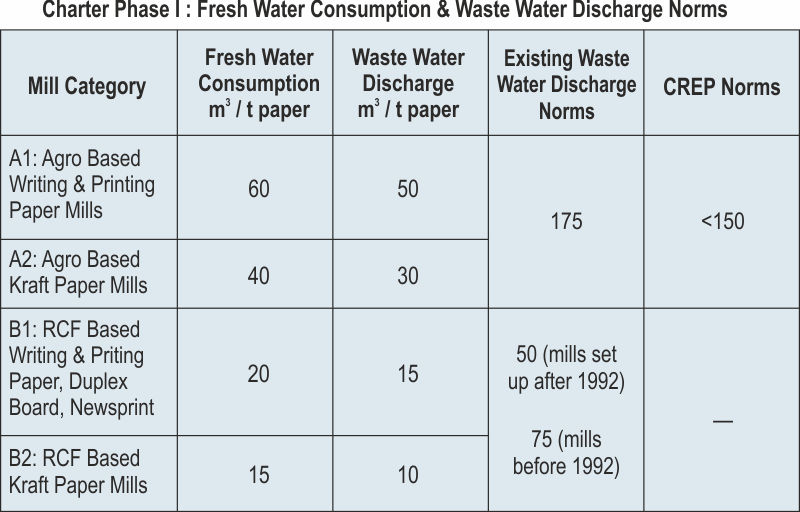
Mr. Vidyarthi accepted that technology actually required or implemented by individual mills to achieve the same documented level of environmental protection may differ on account of their unique set of circumstances such as scale of operation, equipments and system configuration, raw material mix, etc. “The concept of Bare Minimum Technology will not only help the individual mills in environmental compliance, but also in survival and sustainable growth,” he added.
Mr. Vidyarthi also informed about the new categorization of the pulp and paper mills. The Indian pulp and paper mills have been categorized in two broad categories – first, integrated pulp and paper mills manufacturing chemical pulp, paper and paperboard and second, RCF and market pulp based pulp and paper mills. These have been further categorized into five – pulp and paper mills producing bleached grades of chemical pulp, paper, and paperboard; pulp and paper mills producing unbleached grades of chemical pulp, paper, and paperboard; RCF and market pulp based paper mills producing bleached grades of paper and paperboard; RCF and market pulp based paper mills producing unbleached grades of paper and paperboard; RCF and market pulp based specialty paper mills.
Mr. Vidyarthi underscored few points of the charter pertaining to fresh water consumption, effluent generation, and treated effluent discharge quality to be kept in mind by various categories of mills. “The charter prescribes norms for these various categories of mills. The treated effluent discharge norms prescribed under the charter have to be achieved within one year and fresh water norms along with effluent generation norms have to be met within one year for short term objectives and two year for long-term,” he added.
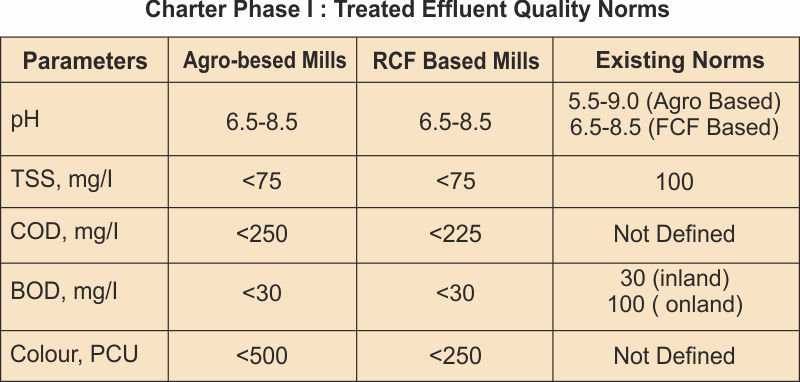
As per Mr. Vidyarthi the norms in the present charter is at par with the recently adopted ‘Best Available Techniques (BAT) Reference Document for the Production of Pulp, Paper and Board’ and associated environmental performance level to be soon mandated by the European Union. “Besides, the charter also prescribes the quantum improvement in effluent quality. For example, the proposed norms prescribe pH level in the range of 6.5-8.5. The norm for TSS has been made stringent from 50 mg/L to 30 mg/L. The norm for BOD has become more stricter from 30 mg/L to 20 mg/L and that for COD from 250 mg/L to 200 mg/L and 150 mg/L in case of integrated mills and RCF & market pulp based mills respectively. The charter for first time introduces the norms for TDS and color; TDS at 2100 mg/L and color at 350 PCU,” added Mr. Vidyarthi.
No chemical pulping without chemical recovery plant (CRP) will be allowed, informed Mr. Vidyarthi. He said that estimates indicated that charter implementation will help in reduction in fresh water consumption and effluent generation up to 60-75 percent and pollution load reduction in terms of TSS, BOD, COD up to 40-70 percent from the current levels.
According to Mr. Vidyarthi, the most challenging part is the implementation of charter over almost 800 mills and to overcome this challenge innovative mechanism of self-monitoring and reporting by individual mills and third party involvement have been introduced in the charter. CPPRI and the paper and pulp mill associations will play a pivotal role in facilitating the individual mills in their planning, assessment, design and execution of action plans for the implementation of the charter, he said.
Presently, the charter is being implemented by about 179 pulp and paper mills operating in nine Ganga River Basin states since April 2015, informed Mr. Vidyarthi. “The major action points covered under this charter in the Ganga River Basin states are commissioning of CRPs for black liquor management in agro and wood based mills manufacturing chemicals pulp; dismantling and removal of chemical pulping facility, mainly digesters, etc., from mills not having CRPs; regular operation maintenance of CRPs by mills and surveillance by the concerned state pollution control boards; preparation of action plans by individual mills to achieve prescribed fresh water consumption, effluent generation and treated effluent discharge quality norms through upgradation of process technology, ETP systems and adoption of best practices; and augmentation and upgradation of ETP up to tertiary treatment level by March 31, 2016,” he added.
Mr. Vidyarthi also apprised the audience that all 152 mills operational in the Ganga River Basin in the states of Uttarakhand, Uttar Pradesh, and West Bengal have prepared the action plan for upgradation of their process technologies, ETP system, and adoption of best practices. He also informed that some mills have common CRPs as no mill is allowed to manufacture chemical without having the CRPs. There are 16 wood- and agro-based mill having 12 CRPs in Uttar Pradesh and eight wood- and agro-based mills having five CRPs in Uttarakhand.
Dismantling and removal of chemical pulping facility is also under process. “CPCB along with State PCBs has ensured the dismantling and removal of chemical pulping digesters from 13 mills in Uttar Pradesh and from 3 mills in Uttarakhand. These actions have resulted in achieving zero black liquor discharge in five Ganga River Basin states. It is estimated that before the closure of agro-based units without CRPs, there was potential of discharge of about 550 TPD COD in to the River Ganga, which has stopped now,” said Mr. Vidyarthi.