Mr. Vivek Chawla, Whole Time Director, and CEO, Emami Paper Mills Ltd., speaks in detail about the technologies adopted at their paper mill, the investment of the company into strengthening the water treatment infrastructure, and the steps undertaken to minimise the consumption of water.
Our water treatment process and wastewater treatment strategies…
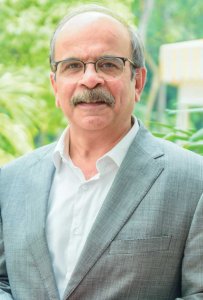
Emami Paper Mills has already implemented the latest technologies in fiber recovery, a closed water loop for water-saving, and an online monitoring system for a green and clean environment. Today, it has also achieved the status of zero solid waste by adopting the principle of ‘Reduce, Reuse, Recycle and Recover’. Wastewater generation is minimised by effectively recycling, and utilising it for paddy cultivation, plantation, gardening and plant use.
The first step towards efficiently managing and conserving water resources is monitoring and mapping water consumption under various processes. This involves conducting a regular water audit that identifies and quantifies water uses and losses from a water system.
Our effluent treatment plant is designed to handle the entire wastewater generated in the process. Our ETP is provided with primary clarifiers followed by UASBR (Up-flow Anaerobic Sludge Blanket Reactor), diffused aeration systems and secondary clarifiers.
Continuous online monitoring systems are installed in the final treated wastewater discharge point and the parameters such as pH, TSS, COD, and BOD are continuously transmitted to SPCB/CPCB.
Our investment into water treatment infrastructure…
The investment in the company’s wastewater treatment infrastructure is approximately INR 50 crore.
Water consumed per tonne of paper produced…
The present water consumption of Emami Paper Mills is around 13KL per tonne of paper produced.
Watch: Evolution of Paper Based Packaging
Measures undertaken to minimise the consumption…
In Board Plant:
- Planned to install high-pressure single-point scanning showers.
- Screens sealing water is returned back to the sealing water tank for reuse.
- All machines are equipped with disc save-all for fiber recovery & for better separation of the backwater for reuse in the system.
In Paper Machines:
- Reduction of nozzle diameter of HP & LP showers in all machines.
- Installed disc filter for better fiber recovery and using super clear water for LP showers, edge sealing (wire part), etc.
- Reuse of filter backwash in PM4 process cooling tower makeup.
- A dissolved air floatation system is installed to recover and reuse the clear water in the manufacturing process.
- Recycling of sealing water in all machines.
In Power Plant:
- Evaporation & drift losses are optimised by installing counter flow cooling towers with drift eliminators and maintaining the system parameters.
- Blowdown water from the cooling towers and the boilers are being recycled in the manufacturing process.
- RO Plant rejects are being recycled in the process and ash conditioning.
- Usage of ETP treated water for screw press shower after adequate treatment
- ETP final treated water is used in various non-process areas like dust suppression in a coal yard, gardening/plantation area, ash conditioning and water sprinkling purpose over the entire plant, etc.
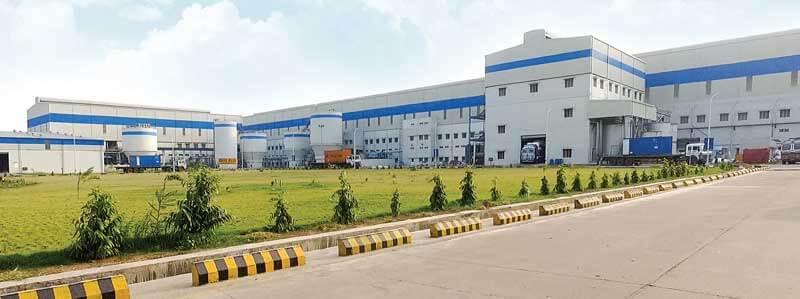
Recent developments with regards to water management and treatment…
We have installed a clariflocculator in the board machine area for the treatment of process water from the machine and to use the clarified water in the process. With the installation of clariflocculator in the board machine, there is a saving in freshwater consumption and it has reduced the hydraulic load on ETP.
Also Read: Emami Paper Mills: Well-Positioned to Look at Further Opportunities in the Paper Industry
Path-breaking steps taken…
The total primary sludge from ETP is taken to the sludge tower of the sludge dewatering plant. This sludge is treated with organic coagulant & flocculent, and taken to pre-thickener to improve the consistency from 3.5 percent to about 15 percent. Sludge is dewatered through a screw press to the dryness level of 50-55 percent. This dried primary sludge is used as co-fuel along with coal in the power boiler (Coal saving – 10500 MT/annum). There has been utilisation of 100 percent fly ash generated in local brick manufacturing units (approximately 300 units).