Datta Kuvalekar is the Head of Forbes Marshall Limited and has surveyed over 500 paper machines globally in his career spanning 2 decades of research, design, engineering of Paper machine steam and condensate systems, heat transfer equipment and Energy Efficient Innovations across multiple industries. His passion continues to be aimed at reducing steam consumption in paper mills across the globe. The article focuses on the causes of high specific Steam consumption in Paper machines and the role of automation in enabling Indian Paper machines to operate at Global benchmarks for reducing specific Steam consumption. Based on his experience in studying Indian Paper machines, the author projects that anywhere between 10-25% reduction in specific energy consumption is feasible using cost effective automation.
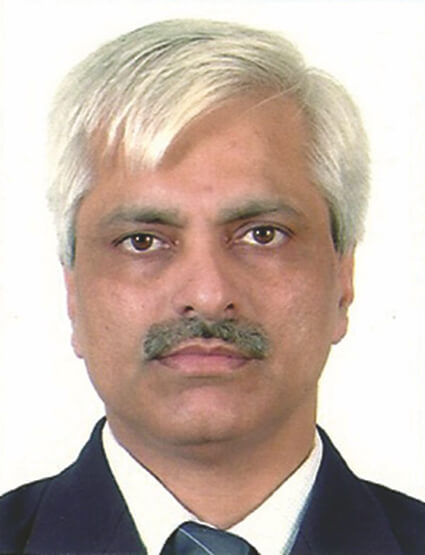
For several hundred years, steam has been the only cheap source of thermal energy. Its ability to be generated from “abundantly” available water makes it the only easily available energy source. It’s now another matter that steam generation needs combustion of fossil fuels whose supply is now increasingly expensive & erratic and probably will be rarer as their natural storehouses deplete at a fast rate. It’s for the same reason that steam is used as the main heating source in the pulp & paper industry. Its ability to heat steam driers at a constant temperature due to its latent heat also makes it a desirable heating medium.
Steam as seen from an Indian perspective is normally generated in either coal or bio mass boilers and these boilers generally have a steam to fuel ratio that varies between 2.5 to 5.5 depending on fuel type and grade. This when one talks of reducing energy consumption in a steam based plant, one has to look at the whole steam circuit- from the boiler house to steam distribution to steam utilization in the paper machine.
The paper machine is a major consumer of steam and thus the focus of this article. This article is based on the results of several energy audits conducted in several Indian and overseas mills. The constant and substantial difference between specific steam consumption numbers of typical European / Scandinavian / International mills and the average Indian mill makes for a good case for saving energy.
Why is that TAPPI standards of 1.3 kg of steam/kg of water evaporated for drier sections are not seen on most Indian machines? Why do we not see condensate recovery factors exceeding 95% on most Indian machines? Our study of Indian mills itself shows stark differences between the best mills and average mills with a 25% difference between them. India should move to reach global standards in energy efficiency.
Specific Energy Consumption
Specific energy consumption is energy consumed per ton of finished production. For thermal energy, this can be expressed as kilogram of fuel/ton of paper or kilogram of steam/ton of paper or Mkcal/ton of paper. For electrical power, it is generally expressed as Kw-h /ton of paper. For recycled based paper machines, one also can look at energy usage per ton of machine production if one needs to delve into actual machine losses by excluding production losses.
Specific energy consumption of paper machines is a benchmark that is now widely used across the pulp & paper industry to compare energy efficient performance of mills. The ideal specific thermal energy consumption of a paper machine should be 2.8 Gj/kg of water evaporated. Good performance should get us to 3.2 Gj/kg of water evaporated.
Our experience of Indian machines vary between 3 to 4.5 Gj/kg of water evaporated. In most of the mills in India energy managers pursue energy reduction targets, but have no physical measurements to actually know where their mill stands today. So it is important to understand the simple truth that you cannot control what you cannot measure.
Factors Affecting Specific Energy Consumption
Specific energy consumption is generally based on finished production. However when it comes to specific equipment, it is considered more practical to base it on actual production draw as that then excludes effects of trim losses and broke & downtime which in any case need to be tracked. Specific steam consumption can be expressed in 2 ways:
– Kg of steam per kg of production (finished or reeled)
– Kg of steam per kg of water evaporated.
While steam expressed per kg of paper is more common and more digestible to users, the steam number expressed per unit water evaporated is actually a more technically correct comparison that can be applied across machines. TAPPI norms suggest that this number can be 1.3 kg/kg of water evaporated for most grades. Ofcourse over time even this number has seen a reduction and 1.2kg/kg of water is also being achieved in some parts of the world.
Specific Steam consumption for Paper machines is influenced by several factors:
• Moisture of web entering the drier section and amount of moisture increment in the sizepress: As a general thumb rule, a 1% increase in entering moisture increases steam consumption by approximately 4%. The type of press and press loading are some factors that govern this moisture value.
• Type of furnish and degree of refinement: The stock freeness usually tends to provide good formation but can leave the press section wetter and thereby increase steam consumption.
• Number of driers in the machine: This has been specially found in board machines which tend to be longer. The radiation losses from driers vary between 5-6% and add to the fixed losses. Thus longer the machine more will be the heat loss through radiation all adding to increased steam consumption.
• Type of steam and condensate system: Generally low speed machines have a steam trap based steam and condensate system. However the type of siphon is the traditional scoop or sometimes a rotary siphon. The combination of a steam trap and rotary siphon/scoop is fatal and causes steam locking of the trap preventing condensate from being evacuated efficiently leading to increased heat requirement due to the thermal resistance of condensate. Another important aspect in steam trap based systems is the need to recover and utilize flash steam from condensate tanks. Typically 5-10% energy savings are possible by recovering flash steam either through thermocompressors or simply using it for feedwater heating.
As machine speeds increase, the trend is to use blow thru systems either in cascade sections or as thermocompressor modules or a combination. Generally in theory both the cascade and Thermocompressor systems are equally efficient, the cascade system tends to be imbalanced and one finds bleed valves that control differential pressure open in many cascade systems. A well designed thermocompressor system then provides better control & flexibility and provides a 10-15% benefit over such imbalanced cascade systems. It is pertinent to remember that this benefit can accrue only if the thermocompressors are correctly sized and mass balance is accurate.
• Condensate evacuation: Typical paper mills report condensate recovery between 65-75% while the ideal number would be @ 95%. Practical measured values on efficient machines range between 85-90%. Increased condensate recovery from the paper machine leads to higher boiler feedwater temperature and an enhanced steam to fuel ratio in the boiler house. The correct choice and size of siphon pipes and siphon tip clearance are critical to optimum condensate removal. Maintaining the correct differential pressure for the given grammage and speed can help maximize condensate removal. A machine that runs with driers full of condensate also then consumes more electrical power and therefore can ruin the energy cost competitiveness of the machine. Such machines also suffer from frequent downtimes and overall extremely high energy consumption. A well designed condensate evacuation system has the potential to reduce specific energy consumption upto 20%.
• The type of hood and pocket ventilation system: The benefit of the hood is to provide a consistent drying environment around the driers and also recover heat from the exhaust. The colder the ambient temperature, the benefits of a closed hood seem to be that much more accentuated not just from the energy perspective but from the fear of condensate dripping onto paper web, while in tropical climates the heat recovery benefit is restricted to essentially sensible enthalpy. However a well designed hood with heat recovery can provide 10-15% reduction in energy consumption. A high velocity well controlled pocket ventilator can also enhance heat and mass transfer in saturated moist pockets, and lead to lower energy consumption. A good pocket ventilator can also lead to increased machine speeds upto 5%.
• Felt Tensions: The role of felt tension in ensuring tight contact of sheet against the hot drier is important to maximize drying rate and therefore heating requirements. Loose felt can cause air gaps between sheet and drier and add thermal resistance.
• Number of wet end cylinders connected to the condenser: This is normally more critical in unorun machines with a large number of uno run driers and also in newsprint or writing & printing machines. The blowthru coming out of these low temperature driers is dumped to the condenser and is a waste and therefore efforts should be made while adhering to process constraints to minimize this blowthru dump to condenser by adjusting differential pressure or by installing cantilever stationary siphons in these driers or if feasible minimizing the number of such driers.
• Machine Runnability: A machine that has frequent paper breaks or more grade changes tends to show higher specific steam consumption (average). The reason is that although no paper is being reeled in a paper break or a grade change, the driers are being kept hot by steam and this is a waste.
• Presence of non condensibles in steam: Air trapped in steam headers or in driers can play havoc with heat transfer and can reduce drier temperatures substantially. This can then result in steam pressures being raised to compensate for lower drier surface temperatures and thereby higher steam consumption. Adequate air venting techniques need to be adapted as a mill wide practice for all steam lines.
Steps to reduce specific Steam consumption
The first step in reducing specific steam consumption is to first measure the steam flow rate and then several other investments can be done to reduce specific steam consumption:
• Install steam flow meters on all main steam lines coming to the machine: It is recommended to install accurate, high turndown steam flow meters on steam lines for each machine. Some machines have thermocompressors, in that case it is essential to measure the low pressure and high pressure motive steam flow rates coming from different sources and add them up to arrive at total steam consumption. As of today, vortex flow meters meet the accuracy requirements needed for steam measurement provided some basic installation precautions are taken. These meters should be capable of providing serial outputs and can connect to a SCADA program or a DCS system and automate the process of calculating the specific steam consumption value.
• The next step is then to take corrective action on the steam consumption through minor and major corrections:-
The Small Things to do first:
1. Check & replace leaking traps: Leaking steam traps can be a large source of steam wastage and hence it should be checked across the plant starting from the boiler house. Check for the right type and size of trap. It is common to see main line steam traps discharging continuously or even bypasses cracked open.
2. Check siphon tips and clearances: Depending on the type of siphon and machine speed, the siphon clearance can be fixed. Typically low speed stationary siphons operate between 6-12 mm clearance while high speed shoe type siphons (stationary or rotary) operate with 1.6-2 mm clearance. The clearance dictates the condensate evacuation which in turn affects steam consumption.
3. Check rotary joint seal failures / leakages: Steam wastage can also occur through leaking rotary joint seals and journal flange gaskets. This is especially common in wobbling joints which are not properly centered on drier axis. Experience suggests that anything upto 5% steam wastage occurs due to leaking joints
4. Check excessive DP set points: Excessively high differential pressure results in more blow thru and possible venting of steam through bleed valves or in the first thermal groups more steam dumped to condenser.
5. Check excessive steam pressure: The need to obtain higher drier temperatures forces many operators to run driers at high steam pressures sometimes perilously close to the hydrotested pressure of the driers. A machine with normal drying rate demand should not need more than 3.5 barg steam to run. The need to operate at higher pressures results only when the other factors like condensate removal or the system design is deficient. High steam pressures results in more steam demand and higher blow thru for the same DP setpoint.
6. Install airvents and sightglasses: The need to eliminate air in steam is well known. Install air vent bottles on every steam header and group header. Sightglasses can be a very convenient way to visualize condensate flow in driers and can be excellent at diagnosing condensate flooding conditions.
The larger things leading to automation:
1. Controlled moisture and basis weight: Higher incoming moisture or too much dryness before sizepress can lead to higher steam consumption. Hence it is required to monitor & maintain the average moisture at controlled levels after press, before size press and at the popereel. This can be attained by installing Quality control system that has moisture and basis weight sensors fitted as a basic minimum.
2. Installing a well instrumented steam and condensate system: A good steam and condensate system should have the following controls :
– Steam pressure control: The steam pressure is controlled to maintain just the right steam pressure required to dry paper and also therefore contains excess steam consumption.
– Differential pressure control: The differential pressure control ensures adequate DP at all times and eliminates the drier flooding condition and also one can use this control to set the right DP at the given speed.
– Level control system: The level control of condensate separators, generally located in the basement of the machine, provides effective blow thru separation and avoids pump cavitation.
Another important aspect of a steam and condensate system is the allocation of driers in each thermal group and then cascading these driers. On most occasions it has been found that there is imbalance in mass flows across groups and that leads to bleed valves dumping steam to the condensers. This has to be corrected in design and can lead to a permanent improvement in steam consumption. Typically this is seen in testliner post-driers where later thermal groups are cascaded to “just after sizepress” driers which are few in number. Many writing/printing machines have their pre-driers imbalanced in a cascade system. The critical issue in design is to have the correct number of driers assigned to each thermal group while in a cascade configuration.
3. A well designed Thermocompressor system: An oversized thermocompressor can be as bad as an undersized one, if not worse. The ability of a thermocompressor to re-circulate blowthru steam or recover flash steam depends critically on the matchbetween design parameters and actual operating conditions. Designing the thermocompressor for the maximum suction flow and ensuring that its output does not exceed the process consumption requires deeper understanding of the process dynamics.
4. An intelligent drier diagnostic system: There have been some recent installations of intelligent drier diagnostic systems which provide on line operational guidance to operators for minimizing steam consumption. While a very noteworthy concept, it still has to catch up in terms of its “wide & broad range” of rule base to be able to provide deep and relevant diagnostics.
Conclusion
Finally, Reduction in specific steam consumption is a matter of focusing on all the above points and ensuring that the machine is kept running at its optimal capacity through a consistent and untiring effort of looking at opportunities to minimize wastages in every area. Automation can help in maintaining a watchful eye on all critical parameters and coupled with corrective control and ensure that machine operates at world class levels of specific steam consumption.