Fitting with the JK Paper sustainability objectives, AFT has supplied a complete POM® wet end and a refining system for the paperboard line. The wet end system includes a full POM approach flow for the multi-layer paperboard machine with POMix stock processors, POMp degasser arrangements, and MaxFlow headbox screening.
JK Paper Grows its Leadership Role
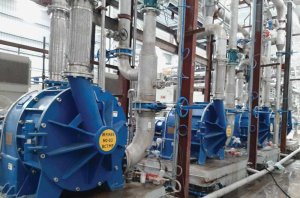
An important 2021 milestone in India’s continuing rise as a paperboard powerhouse is JK Paper Ltd.’s new PM5 cartonboard machine in Fort Songadh, Gujarat. With a capacity of 170,000 TPA, this multi-layer paperboard machine successfully started up at the end of August 2021. PM5 is designed to produce paperboard grades with basis weights ranging from 160-440 gsm with an operating speed up to 700 m/min using BCTMP and Kraft fibers.
In the words of JK Paper’s President and Director, Mr. A.S. Mehta, “We are proud to produce premium cartonboard grades, doing so with world-class equipment and highly trained operators. Our strong sustainability commitment is demonstrated by low energy and water consumption for a machine of this size.” Mr. Mehta adds, “We will produce top-quality folding boxboard (FBB) and solid bleached sulfate board (SBS) and convert them to meet customer requirements with our modern converting, finishing, and warehousing facilities.”
Mr. H.P. Singhania, Vice Chairman and Managing Director of JK Paper, also expresses appreciation for the JK team and suppliers for successfully starting up a new board line in extremely challenging times due to Covid interruptions, travel restrictions, and remote commissioning of various equipment.
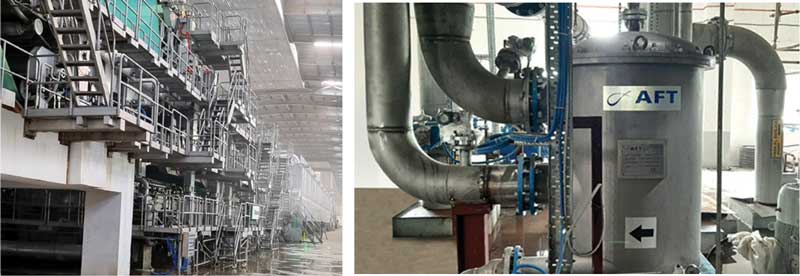
AFT Stock Prep and Approach
Fitting with the JK Paper sustainability objectives, AFT has supplied a complete POM® wet end and a refining system. The wet end system includes a full POM approach flow for the multi-layer machine with POMix stock processors, POMp degasser arrangements, and MaxFlow headbox screening. Basic engineering and mill site services were part of the AFT delivery. Engineering supply included complete process and plant engineering with 3D modelling.
Compared to traditional approach flow systems, the POM paper machine wet end with headbox screening delivers superior stock cleanliness in a compact and efficient package. Without the need for traditional storage tanks, POM runs smoothly with lower water and energy usage for enhanced environmental performance. Operational features of the POM system result in higher paperboard machine operating efficiency and increased annual production capacity.
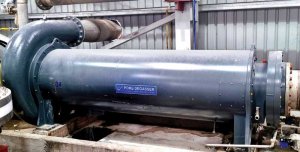
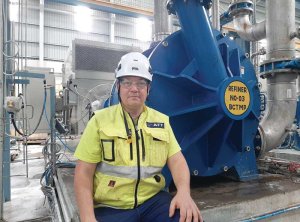
Refiners and Deflakers
According to Mr. S.K. Jain, Head of Board Projects, “AFT’s contribution helps us make fast grade changes in a cleaner, short circulation system – with less air and biological build-up to yield fewer sheet defects and breaks, which is best for our multiply operations.”
Watch: Evolution of Paper Based Packaging
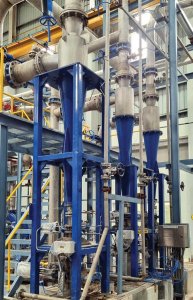
In addition, AFT’s ADC38 double conical refiner design increases production capacity for a single unit, while offering easy access for maintenance and filling changes. The refining process design is flexible and adaptable for multiple fiber types. JK Paper can easily configure the refining system as per fiber type and refining requirements needed for their products. Low-intensity refining is achieved with Finebar® conical filling technology for optimum fiber development with low energy use.
Notes Mr. Sourav Das, AFT Regional Sales & Marketing Manager – Asia Pacific, “Board properties are significantly influenced by refining. Desired objectives happen almost instantly in combination with the benefits delivered by the compact POM system. This helps of course with grade changes, but also in product optimisation. The commitment to innovation and sustainability at JK Paper is impressive. We do our best when flexibility is important, matched with a long-term focus on doing what is better for the planet.”
Also Read: JK Paper Installs New HERB Recovery Boiler from ANDRITZ
Mr. Olli Pekka Riippa, AFT Product Manager – Refiners and Deflakers says, “Our cooperation with JK Paper gives us opportunities to push refining to a higher level. Fiber treatment can be optimised to achieve the specific product characteristics that their customers demand. As proven in many installations, the ADC refiner concept saves applied refining power. Preserving energy is one of the main factors for papermakers’ profitability and competitiveness.”