Krofta Engineering Limited, one of the leading suppliers of waste water treatment equipment and complete water management solutions across the globe, has come up with its own anaerobic technologies, in order to overcome the issues of smell and color faced by the kraft paper mills. This was revealed by Mr. Raghvendra Khaitan, Managing Director, Krofta Engineering Limited, while interacting with Paper Mart during Paperex 2023.
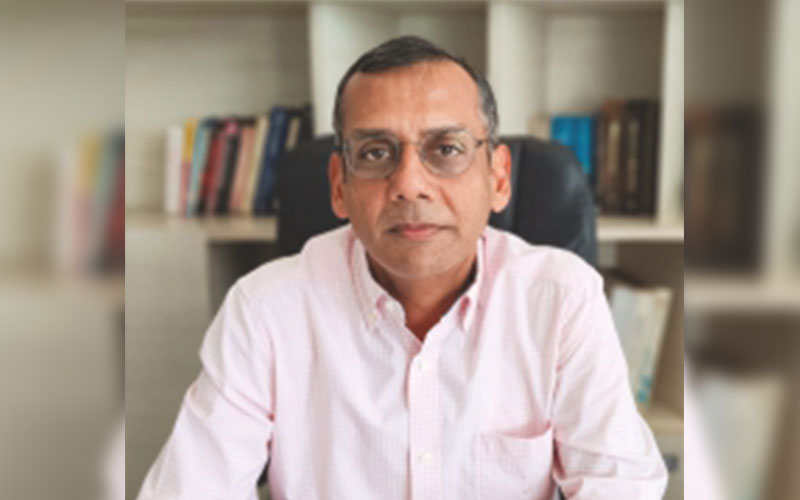
Paper Mart: Krofta Engineering Limited recently completed four decades in India. Congratulations on the achievement. Please walk us through your business journey, major achievements and crucial milestones.
Raghvendra Khaitan: Krofta Engineering Limited, India began operations in 1983 as a manufacturer for Dissolved Air Floatation (DAF) units. Since then, we have added multiple products to our portfolio and made technical collaborations with several companies around the world. What began as a joint venture with Dr. Milos Krofta, the pioneer of the DAF technology, has grown to provide many new technologies such as the most up-to-date DAF clarifiers (rectangular/circular), sludge de-watering systems (screw press/belt filter press), oil water separators (API/TPI/CPI), Lamella clarifiers, tertiary filtration (ACF/PSF/DMF) as well as end-to-end water solutions such as ETPs (Effluent Treatment Plants) and WWTPs (WasteWater Treatment Plants), including energy generation using anaerobic technologies.
Today, Krofta Engineering Limited India is the leading supplier of wastewater treatment equipment, and the world leader in clarifiers based on DAF technology. We provide complete global solutions for water and wastewater treatment, recovery of resources and energy generation. We design, engineer, manufacture, install and commission all our machines and projects. All our manufacturing is in our own facility in North India. We also provide complete turnkey solutions, including effluent treatment plants. KEL maintains the highest quality and procurement standards. With over 4,000 installations in India alone and more than 12,000 around the globe, we consistently meet customer requirements, have reliable on-time delivery and cost-effective solutions which operate at the highest efficiency.
We have our own 60,000 square feet manufacturing facility in Faridabad, India. We have a qualified team of top personnel along with a certified production team.
PM: Please share information about your DAF technology and its use in the pulp and paper industry.
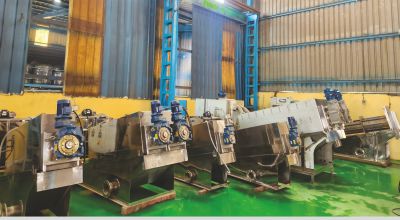
RK: Krofta Engineering Limited (KEL), India was incorporated in India as a joint venture with Dr. Milos Krofta, the inventor of DAF technology. This is why the name ‘Krofta’ is synonymous with DAF. Our DAF technology is used for physio-chemical separation and is most popularly used to treat the paper machine back water and is used for fiber recovery, which is then taken back to the machine chest. Our DAFs are also used as secondary clarifiers in lieu of conventional clarifier systems, especially in those areas where space is constrained and in this case they also serve a dual purpose of not only physio chemical separation but also sludge thickening. Additionally, our DAFs are also used for color and Chemical Oxygen Demand (COD) reduction after the secondary clarifier, and we have seen excellent results in two paper mills where we have installed them. Our DAFs work best with our patented air dissolving tubes, which is a pressure vessel used to saturate air in water.
PM: How has the industry responded to your anaerobic systems?
RK: Today, the industry is not only bereft of new technologies, but we also cannot ignore the cost of procuring fresh water, which is ultimately going to come in. Keeping in mind the fact that new technologies need to be implemented where the kraft paper mills are facing issues of smell and color, we have introduced our own anaerobic technologies. With the help of varied anaerobic treatment methods, we are able to provide more value to our customers and give them the best solutions to keep their paper mills running without any hiccups. We help our clients produce smell-free paper, while allowing them to save costs by re-using process water and generation of bio-gas. We think it is definitely a much-required system and a proven technology. Countries worldwide had them in the past and we think looking at the future where companies would be expanding capacities, simple normal activated sludge systems will not be sufficient to handle those waste waters, so anaerobic systems will definitely play a major role. These are also of utmost importance in paper mills due to the prevalence of high levels of COD (chemical oxygen demand).
Watch: Top Paper Companies 2023
PM: Tell us about your other technologies, which have helped the pulp and paper industry.
RK: As pulp and paper is a large carrier of water, sludge generation is a major concern, also in view of the guidelines issued by the National Green Tribunal (NGT) regarding plant discharges in April, 2019 and upheld by the Supreme Court in June, 2021. With our recent development of screw press and triple wire belt press, we are able to handle and dewater large volumes of sludge, which invariably if not treated, are either discharged as a slurry or taken back to ETP which increases the load. Since the sludge cannot be thrown out and has to be dewatered to a maximum extent, our triple wire belt press ensures higher throughput and allows you to handle large volumes of sludge.
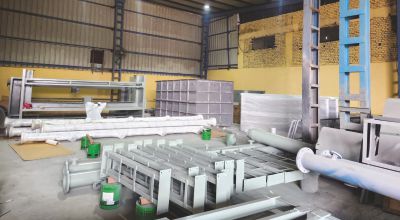
Further, we continue developing our existing technology, such as in DAF’s. Our Megacell has been very successful in paper mills across India and outside. We have also launched a sludge digester, which is of great importance to the paper industry as we are able to generate gas from excess sludge and this generation of gas can become a part of green energy initiative for the paper mills. From the point of resource & availability and to ensure good usage of water, prior to Krofta DAFs, we have also launched our disc filters, which are used primarily for filtration and not for pulp thickening, which they are typically used for.
PM: Please elaborate on the philosophy of your company and new innovations.
RK: Our objective is to keep on innovating as much as we can, as you have seen in the past, when we had Supercell and Sedicell as part of our DAF technology. Innovation in that category came with Megacell, which has been a good success since we launched it about two years ago. We have sold more than 100 machines. Similarly, we earlier had twin wire presses, now we have made them triple wire. We believe that innovation is the key and today’s customers are receptive to the fact. Since it is coming from Krofta, they know our background, they know the capability of our engineering team and the key factor here is that we are able to deliver.
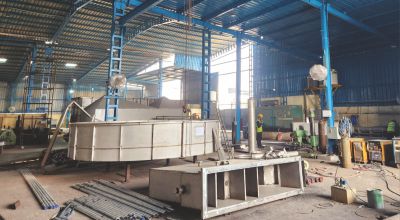
PM: Kindly share details about your market footprint.
RK: We look at exports as well. Today, water is a concern everywhere. For us today, the opportunities that come are definitely from the Middle Eastern region and the African region for sure. The places where either the new mills are coming up or the capacities are being augmented, we guess, those areas are opening up for us.
PM: Research plays an important role in the development of a company. Please tell us about your R&D team and manufacturing capabilities as well.
RK: From the R&D point of view, we have built up our team over the last year. Our team includes people from engineering backgrounds, who have worked around these technologies earlier. They are familiar with these technologies and we can develop them in-house as well. From the manufacturing perspective, most of these equipment are designed and fabricated at our own end. We have increased our facilities in terms of space, manpower and more machine requirements, but ultimately at the end of the day, if we do not make a good and viable product that is more tenable to the customer, then it doesn’t matter. We cannot just make something and give it to the customer. The key factor here is that the product should not only look good, but it should perform well too.
Also Read: Allimand Eyes Specialty Paper Market for Growth in India
PM: Please tell us about your future innovations.
RK: I think these innovations that we have done in 2023, will definitely see the light of the day in 2024 and years to come. With more than 400-500 paper mills active in the country today and everybody looking at expansion, there is ample scope for us to get a foothold within the market here as well. Innovation is the key, so we are sure we will be looking at something new in 2024 to add to our basket as well.
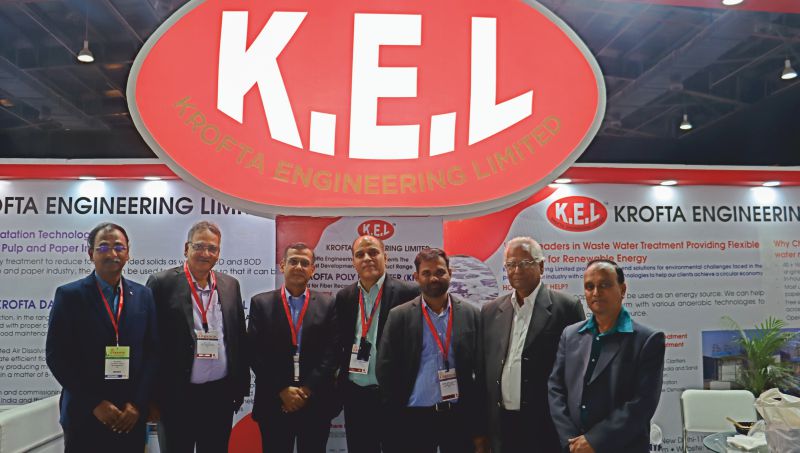