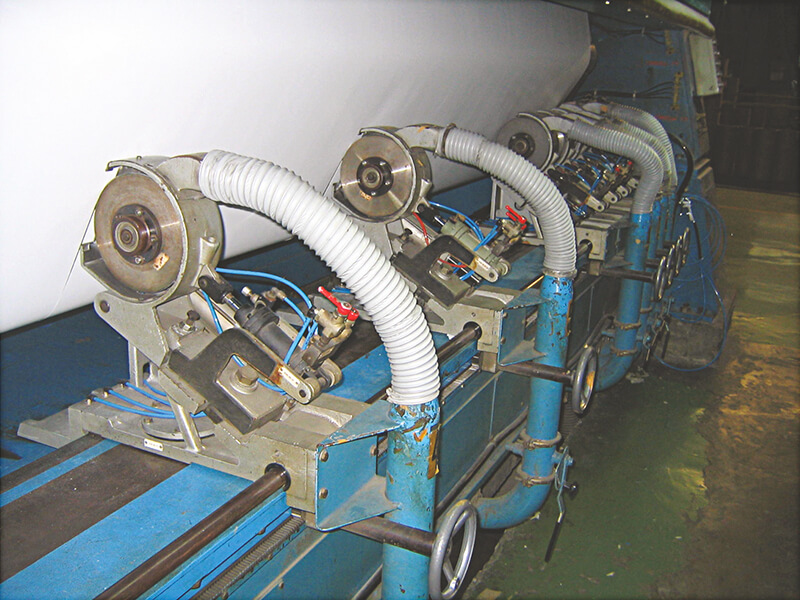
Optimum cutting performance of machine knives does not only require observance of their setting parameters but the framework conditions of the machines have to be appropriate, too. When adjusting transverse blades, we are talking about hundredths of a mm; in this respect, equipment and tools have to be in a perfect condition.
When setting circular blades, special attention is to be paid to overlapping of blades, contact pressure, shear plane angle, and forward slip.
When users detect that cutting quality starts to deteriorate or that the service life of machine knife becomes shorter, this is quite often due to the technical condition of the cutting section which is less than ideal and not due to the tool itself. Well trained repair staff and machine operators have to be able to detect, analyze, and eliminate sources of disturbance. However, corresponding knowhow and experience are often missing.
Training and Practice
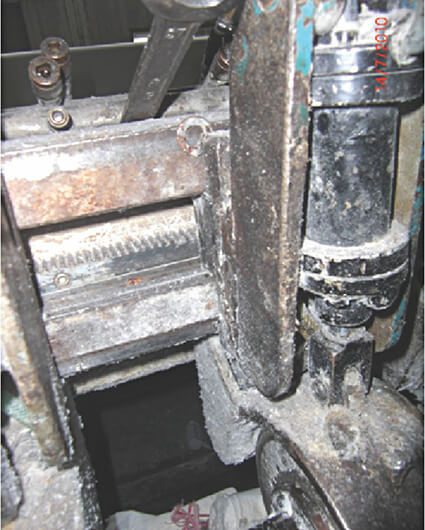
In order to be able to respond to cutting problems appropriately and quickly, operators have to dispose of a vast knowledge of the influencing factors on the cutting process. Theoretical and practical training regarding troubleshooting forms a solid basis to be able to analyze and solve problems accurately.
Preventive Maintenance – Avoiding Emergencies
In many companies, it has been customary for some time to take preventive actions because everyone knows that emergencies bear risks which are always connected with resulting costs, too.
• On the one hand, this includes the availability of the machine. Regarding machine downtimes, stocks can always be justified.
• Regrinding intervals of the knives are to be selected in a favorable way to avoid bottlenecks right from the beginning. Here, the grinding quality should have priority over the quickest possible return of the knife.
• An internal or external grinding service guaranteeing manufacturer’s quality is to be ensured to provide reproducibility of the cutting performance.
• But it is even more essential to perform regular preventive maintenance of the equipment consistently and in good time. In the day-to-day business, this is often neglected due to deadlines or capacity bottlenecks which may be connected therewith.
• Defective knife supports or worn bearings may entail significantly longer downtimes or quality problems and customer complaints.
Operators, knife manufacturers, and service providers equally profit from talking openly about homemade problems such as machine failures by material jam (crash) which may damage knife support or transverse blade drums.
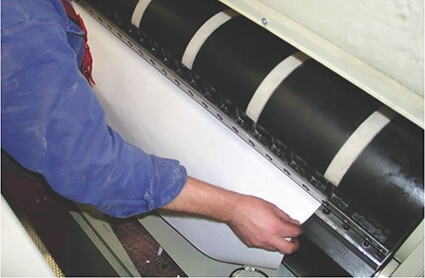
cutting edge and good fine adjustment secure the
optimal cutting result.
Operating errors should also be discussed openly as making mistakes is human and all of us can learn from them. Common efforts and team spirit in this respect do not only ensure the sustainable efficiency of the production process but also enhance it.
Turn some employees into your in-house experts holding the company’s know-how!
Preventive maintenance and repair ensure your product quality, avoid customer complaints, and increase the efficiency of your production processes and the profit situation connected therewith.