Established in 2009, north India based BPML produces writing and printing (non-surface sized, SS Maplitho and Copier) grade papers with a capacity of 1.1 Lakh tonnes per annum with latest technologies in process for pulping and paper making.
October 22, 2017
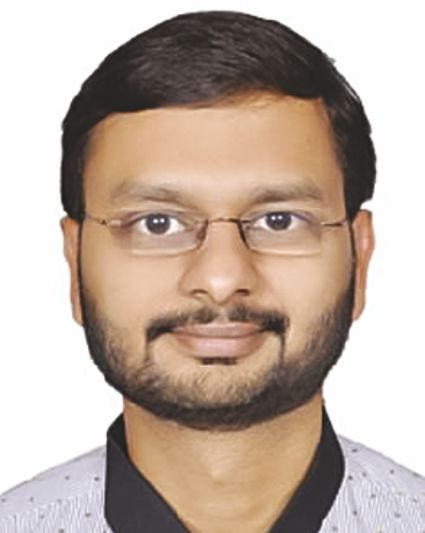
Director, BPML
In a first of its kind, Bindals Papers Mills Ltd. (BPML), an agro based integrated pulp and paper mill is pioneering the transformation towards Zero Liquid Discharge (ZLD).
BPML has always been on a quest to look for state-of-the-art techniques for a greener ecosphere. One of the major advances towards this initiative has been the efforts to reduce water foot print. The organization has realized an innovative approach to reduce Fresh Water consumption by recycling back water from individual sections of the mill, adopting 4R methodology i.e. Reduce, Reuse, Recycle, and Recover.
BPML chalked out a systematic plan to achieve their goal of Water Footprint reduction. A brief snapshot of the plan is as follows:
Step I: Change their Extraction stage of Pulp Bleaching Plant which produces:
- about 80% of pulp mill effluent color
- 60% of its COD
- 30% of its BOD
To Oxidative stage by using oxidative chemical at lower ph and temperature which reduces caustic and steam. It also eliminates hydrogen peroxide.
Step II: Make each section of the mill as zero discharge
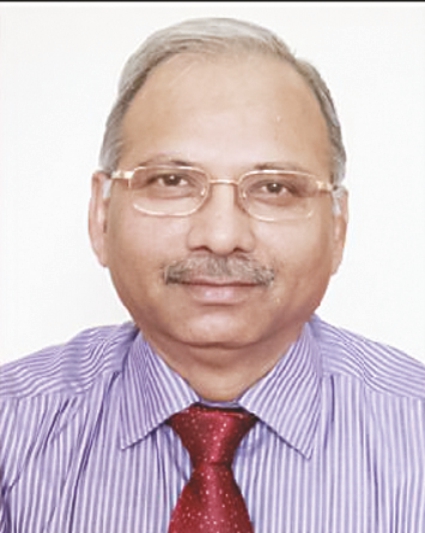
President, BPML
a) Pulp Mill and Recovery: Close water circuits in all the sections so that the recycled water can be used rather than the fresh water. This was implemented in all sections except the bleaching section where the first stage bleaching effluent goes to ETP Plant for the treatment.
b) Paper Machine: Replace fresh water being used in Wire & Press sections with treated paper machine white water by installing specially designed DAF followed by Micro Filters to achieve less than 10 ppm in the white water. Also, recover water from the CC reject and utilize it as make-up water for the cooling tower. Thus, making the machine functions a closed loop.
Step III: Upgrade the ETP Plant by installing the following:
a) Mist Aeration system in the aeration tank in addition to fixed surface aerators
b) DAF, after Secondary Clarifier to improve further environment norms, followed by MMF
Step IV: To achieve ZLD, customized Reverse Osmosis (RO) systems are being installed for integrated Pulp & Paper Mill. This gives 97% recovery of effluent as Mill water which will be utilized back in the mill in place of Fresh Water. The remaining 3% reject will be evaporated. This project is expected to complete by October’17.
Post this, Bindals Papers Mills Ltd. Muzaffarnagar (Uttar Pradesh), India will be the first ZLD integrated agro based Pulp and Paper Mill in India and abroad, producing writing and printing grades.