ITC’s Paperboard & Specialty Papers Division (ITC-PSPD) is known for its courageous first steps in the realm of pioneering technologies, and its Bhardrachalam unit is one integrated edifice of many such initiatives, latest of which is the India’s first BCTMP mill. The mechanical pulp mill, again a first for India and operational since 2017, reaches substantially closer to PSPD’s ambition of becoming 100 percent self-reliant in local fiber.
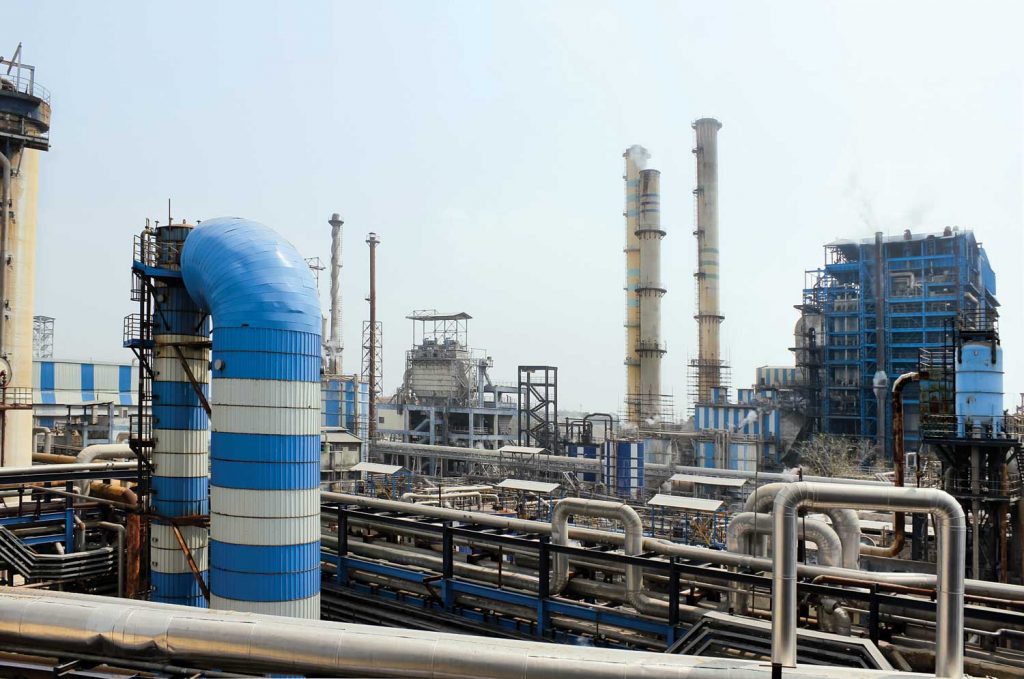
ITC-PSPD believes in ideas — ideas that always keep it at the leading edge of the Indian pulp and paper industry. This belief is not out of a sense of adventurism, but has always been necessitated by a pragmatic urge to be efficient, innovative, and progressive. The recently commissioned BCTMP mill at Bhadrachalam unit is the culmination of one such idea that marked the start of a new chapter in India’s pulp and paper industry, a chapter of self-reliance in mechanical pulp production.
Bhadrachalam, situated on the banks of Godavari in Telangana, falls in a fertile riparian plain and is suitable for cultivation of crops like cotton, chilli, and paddy. The region’s climate is also perfect for fast growing eucalyptus, and one can easily spot numerous eucalyptus plantations dotting the area while approaching the PSPD’s Bhadrachalam unit. Today, the region around Bhadrachalam unit has become a prolific ground for PSPD’s successful plantation experiments and provides the integrated mill the much needed, high-quality fiber for its packaging operations.
A BCTMP Mill was Needed: The Background
The idea of large-scale plantation in the region was PSPD’s first step towards independence in matters of virgin pulp, and going for BCTMP unit was another in the same direction and it proved a massive success, so much so that ITC is mulling over expanding the capacity of this mechanical pulp unit.
If we closely look into the decision for setting up a BCTMP mill, it’s not a one-off or an isolated decision taken in haste only to be ‘the first’. Everything ensued from the idea of becoming ‘100 percent self-reliant’ in wood pulp — the plantation drive, its subsequent growth, and availability of ample eucalyptus wood — all gravitated to the conception of a mechanical pulp mill.
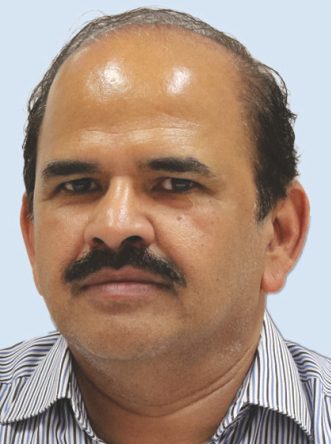
Besides, mechanical pulp is a critical ingredient in manufacturing packaging grade board and importing 100,000 tonnes of mechanical pulp every year was a costly business. Mr. Makrand Barhanpurkar, Unit Head, ITC-PSPD, Bhadrachalam, says, “There is a gap in demand-supply for this pulp, and no new capacities are being added up globally owing to low-profit margins. By this strategic investment in a BCTMP plant, we have isolated our business from vulnerability arising out of demand-supply gap and foreign currency fluctuations.”
However, becoming self-sufficient in procuring wood from the locality owing to PSPD’s successful plantation drive was one of the strongest determiners to go for a mechanical pulp mill. Today, the plantation covers an area of around 200 km surrounding the unit and over 15,000 farmers supply more-than-adequate wood for mill’s pulping operations. ITC-PSPD’s clonal research center and farmer contact programs have ensured that not only the right type of eucalyptus are grown, but that farmers also are well benefitted, for example, growing eucalyptus in rows with existing crops like cotton and chilli.
Right BCTMP Mill: Exploring Technology Options
Even after the decision was made, ITC took long time in exploring the technology best suited to available wood, plant setup, and product range. Finding the best technology for mechanical pulping keeping in mind the pulp quality, efficiency, and excellent environmental performance wasn’t easy, and it took ITC multiple foreign tours to examine various BCTMP technology alternatives. Mr. Barhanpurkar says, “Our projects team travelled around the world to explore the right BCTMP technology, and eventually gave their decision in favour of Andritz’s Pre-conditioning Refiner Chemical Alkaline Peroxide Mechanical Pulping (P-RC APMP) technology, which they have been observing for a long time.”
Andritz’s BCTMP technology has been under ITC’s observation since 2010, followed by a reference visit to China the next year. However, it was only in 2014 in China that ITC was able to experience first-hand the Andritz’s latest BCTMP technology, called P-RC APMP. In 2015, at the Springfield pilot plant, ITC carried out extensive trials with eucalyptus wood species, and the trial experience convinced the management further in favour of this newest pulping technology.
ITC’s technological demands were quite stringent and in keeping with the concept of modern mill built around the core of sustainability, quality, efficiency. The zero-effluent concept, minimum COD and BOD, low chemical consumption, low specific energy consumption, etc. were some of the pre-conditions put by ITC that must have been fulfilled by the pulping technology. Added to these, ITC also wanted a technology that would best fit within the existing process technologies to achieve a synergy resulting in low material consumption and running costs. Besides, a technology which could give the best process yield with the available eucalyptus hardwood was always a consideration.
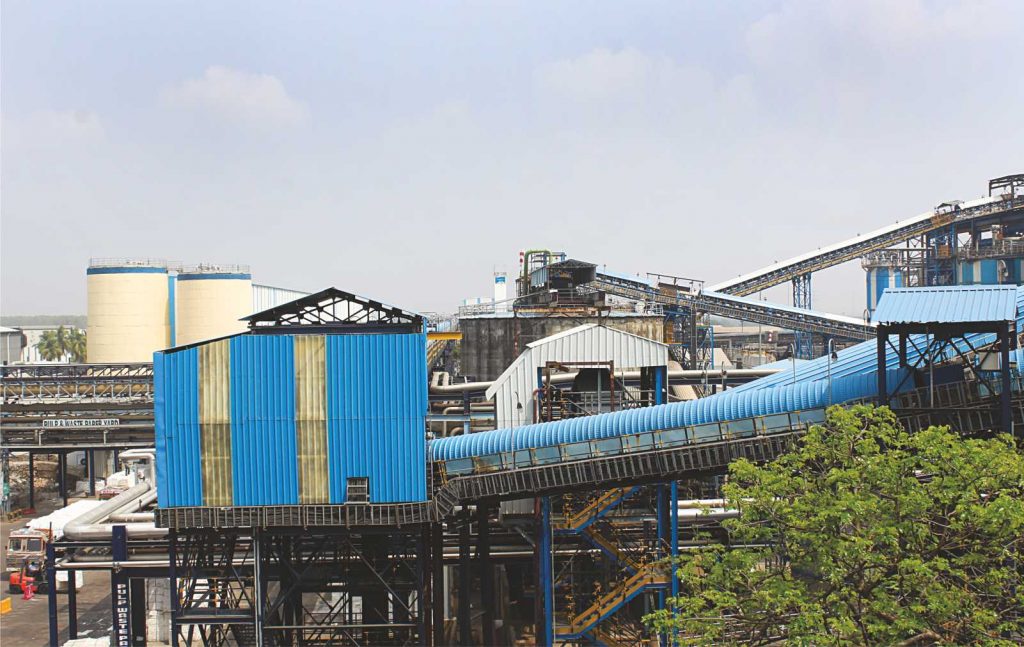
For above considerations, Andritz’s P-RC APMP emerged as a preferred BCTMP technology for the production of high-quality chemi-mechanical pulps from local hardwoods. Besides, The P-RC APMP process is ultimately designed for optimum pulp properties, such as brightness, strength, and bulk. The process impresses with minimum chemical, energy, and water consumption for all hardwood species.
The vision to install the new mechanical pulp mill was also strongly predicated on utilizing the existing plant technologies without disturbing the ongoing processes. The new unit was to be conceptualized in a manner to achieve an overall technological synergy and chemical balance. For example, using the common chemical recovery was tricky and has proved to be a remarkable success. Today, at Bhadrachalam, chemicals from the BCTMP effluent are recovered in the mill’s existing recovery boiler and recausticizing plant, made possible by using oxidized white liquor as an alkali source in the mechanical pulp mill. Also, black liquor of the integrated kraft pulp mill is evaporated together with BCTMP effluent and clean condensate is sent back to BCTMP plant to be used for pulp washing. As a result, the total mill effluent is considerably low and fresh water consumption minimum.
Uniquely New Technology for India
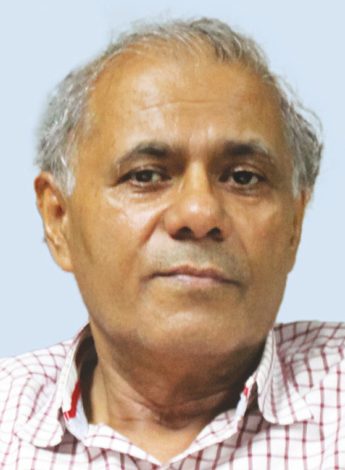
ITC-PSPD installed Andritz’s 300 admt/d P-RC APMP mill in the year 2017, and it took around 14 months from contract signing to start-up, i.e. March 2017. The mill is designed to process 100 percent eucalyptus hardwood with leverage to use 30 percent softwood in its furnish to produce high quality pulp with lower power and chemical demand. As described earlier, the main challenge was to integrate this pulping technology with existing kraft pulping mill without affecting the chemical balance across soda recovery plant, and the objective was realized substantially in the design of the new mill. Mr. K. D. Sharma, General Manager, Pulp Mill, ITC-PSPD, Bhadrachalam, says, “Integrating the chemical recovery for BCTMP with kraft mill was crucial for us. To achieve this end, the new APMP plant is designed to handle 100 percent oxidized white liquor, in place of caustic, which is required for peroxide bleaching. This helped us to manage and sustain the white liquor’s sulfidity, an important factor for maintaining the pulping efficiency.”
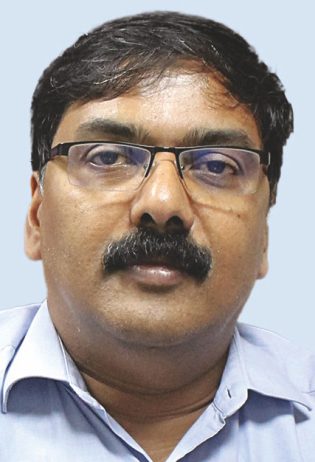
Mr. K. Rambabu, Chief Manager, Pulp & Recovery, ITC-PSPD, says, ” It is very important that P-RC APMP technology applies chemicals like oxidized white liquor, sodium hydroxide (NaOH), and hydrogen peroxide (H2O2) in impregnation and after the primary refiner. In the new BCTMP, we use around 70-75 percent of oxidized white liquor, made possible only by this technology and crucial for maintaining an overall chemical balance across pulping and recovery processes.
Andtitz’s P-RC APMP mill at Bhadrachalam has many new features, which make this technology avant-garde among other hardwood pulping technologies — features such as the 2-stage MC-HC bleaching system, MSD Impressafiner, 2-stage refining process, 6-stage washing process, etc. This is the first such BCTMP mill in India, and in the world for many reasons, suited to the mill’s demands of flexible production of high-quality pulps at the most economic operating costs, a primary consideration for mills in India.
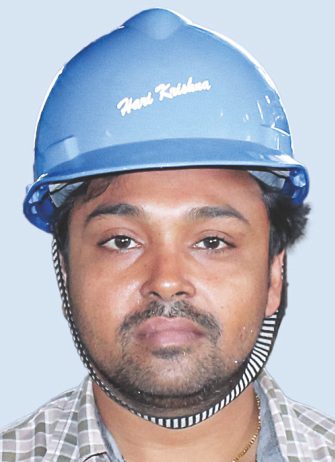
For P-RC APMP mill at Bhadrachalam, Andritz has designed the entire process as a single line starting with chip washing followed by chemical impregnation with the unique MSD Impressafiner. MSD (Modular Screw Device) provides a highly efficient chip compression which opens up chip structure to uptake chemicals in impregnation stage. In the process, dirty liquor is removed because of extreme chip compression and then the chip is opened up before the chemicals are applied in the impregnation stage to enable the maximum penetration of chemical into chip. Mr. A. V. Hari Krishna, Manager, Pulp Mill Operations, ITC-PSPD, Bhadrachalam, says, ” This MSD Impressafiner is really a unique feature and, I would say, is the heart of the BCTMP unit. The process enables maximum chemical intake to enhance the pre-bleaching mass of the chip. Efficient chemical impregnation is also useful for equalizing the chip moisture profile and chip bulk density, important for reducing energy requirement in subsequent high-consistency (HC) refining stage.”
Mr. Sharma further adds, ” In particular, with the local eucalyptus woods with its high extractives contents and high dryness, MSD is an important step before refining and bleaching to reach high brightness and keep the chemical consumption low.”
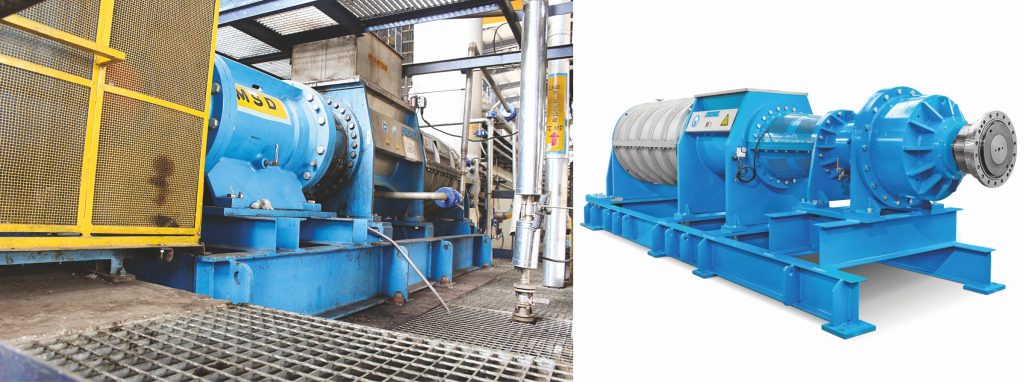
For each mechanical process, refining is one of the most important stages. At ITC’s BCTMP unit, there is a highly reliable 2-stage refining process, designed as a single line by Andritz, HC refiner in the first stage and a single stage TwinFlo LC refiner as the second stage. Mr. Sharma describes the process well, saying, “High-consistency (HC) refining converts chips in to pulp followed by low-consistency (LC) refining to improve the pulp quality in terms of fiber development, i.e. improvement in strength index, and control of required freeness depending on board requirements such as low shive levels.”
Further explaining the 2-stage refining process, Mr. Hari Krishna says, “There is also an ANDRITZ TwinFlo refiner installed for reject refining. The low-consistency pressure screening system consists of proven ANDRITZ ModuScreens with highest screening efficiencies to remove shives and undeveloped fibers. In addition, a cleaner system is installed to remove dirt particles and so-called stone cells (or “scleroids”). Mr. Rambabu says, “Heat generated in the HC refiner can be recovered in heat recovery boiler which generates steam which can then used for internal and evaporator heat requirements.”
The 2-stage MC-HC bleaching system is located right after the primary refiner, but before secondary refining and screening. Mr. Sharma says, “The 2-stage peroxide bleaching system which consists of MC (medium-consistency) followed by HC (high-consistency) bleach reactors enables the production of pulp with wide range of brightness from 70 – 80 deg ISO. A washing stage was added before the first bleaching tower to remove detrimental substances and ensure optimum bleaching results and minimum peroxide consumption.”
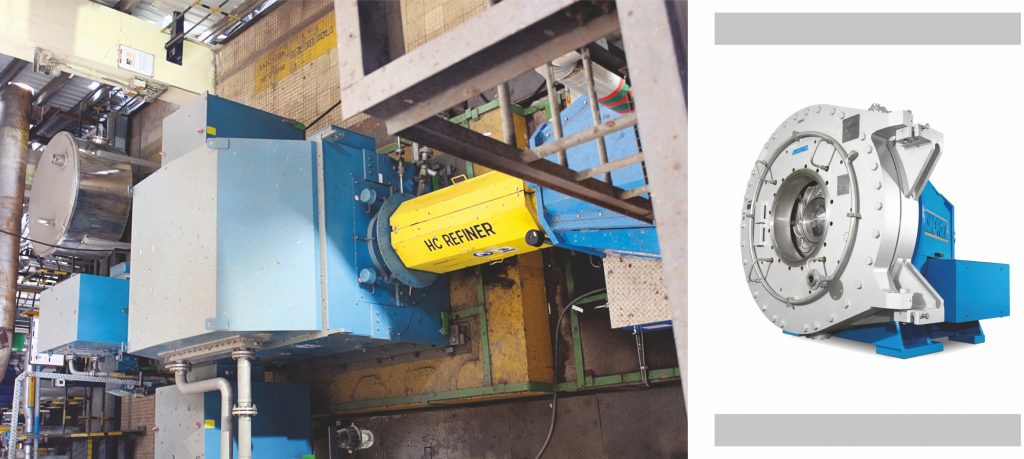
ITC’s BCTMP mill at Bhadrachalam also becomes the first mill in the world to be equipped with 6-stage washing to produce one of the cleanest pulps around. Mr. Rambabu says, “The unique 6-stage washing system enables us to produce superior, clean pulp required for manufacturing various food-grade boards, which ITC offers in the industry.” Mr. Hari Krishna says, “Highly efficient pulp washers (screw presses) clean pulp as well as recover the residual bleach chemicals after HC-bleaching stage to be reused in MC-bleaching stage. This reduces the overall chemical and water consumption.”
Environmental Performance: Beaconing the Future
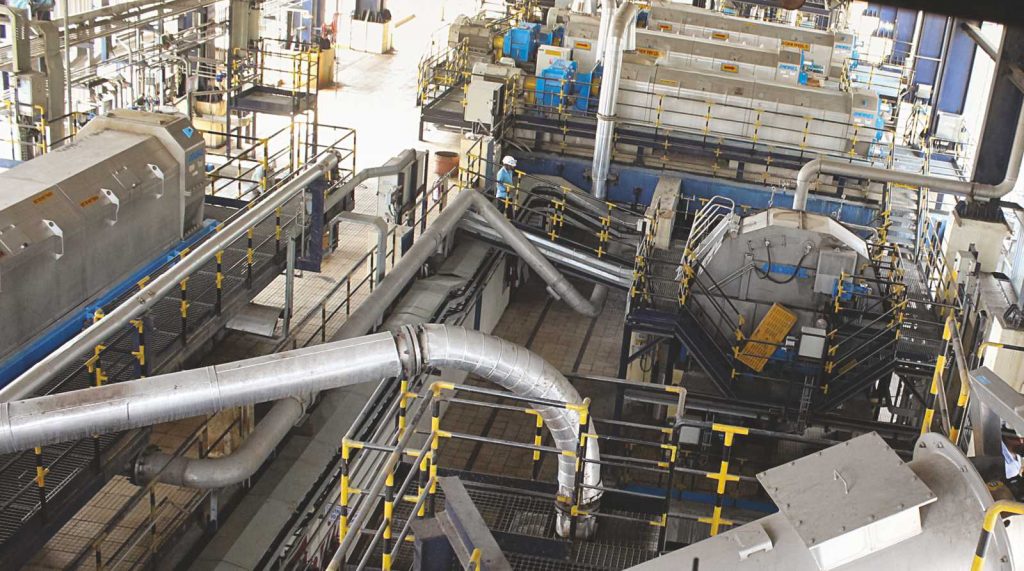
Making mechanical pulp has its own challenges, but it has its boons too, especially the beneficial environmental outcomes. First and foremost, while discussing environmental impact, it is pertinent to recall that ITC’s mechanical pulp production is strongly rooted in using the local eucalyptus hardwood, which is amply available only because of remarkable success of ITC’s plantation drive, which in turn has its own direct environmental benefits in terms of green cover and sequestering carbon.
Besides, in the mill conception, planning, and development stages, environmental concerns like low consumption of power, water and chemical; lowest possible BOD and COD load; lowest possible discharge of effluent; and effective zero liquid discharge system were recurrent themes. All these concerns were effectively addressed by Andritz’s P-RC APMP technology, and the mill has set a world record for any the lowest COD in final pulp.
Bhadrachalam unit has also become one of the first units to implement the zero liquid discharge (ZLD) concept with any feasibility. At the mill, there is no liquid discharge to effluent treatment plants like conventional APMP mills. ITC has installed specially designed and customized evaporator plant, exclusively for handling low-solid effluent from APMP mill. Mr. Barhanpurkar says, “Concentrated solids from evaporator is mixed with the liquor stream coming from Kraft mill and processed further in soda recovery plant to recover chemicals. Clean condensate from evaporator is sent back to APMP mill where it is used for pulp washing, thereby reducing the fresh water consumption in APMP.”
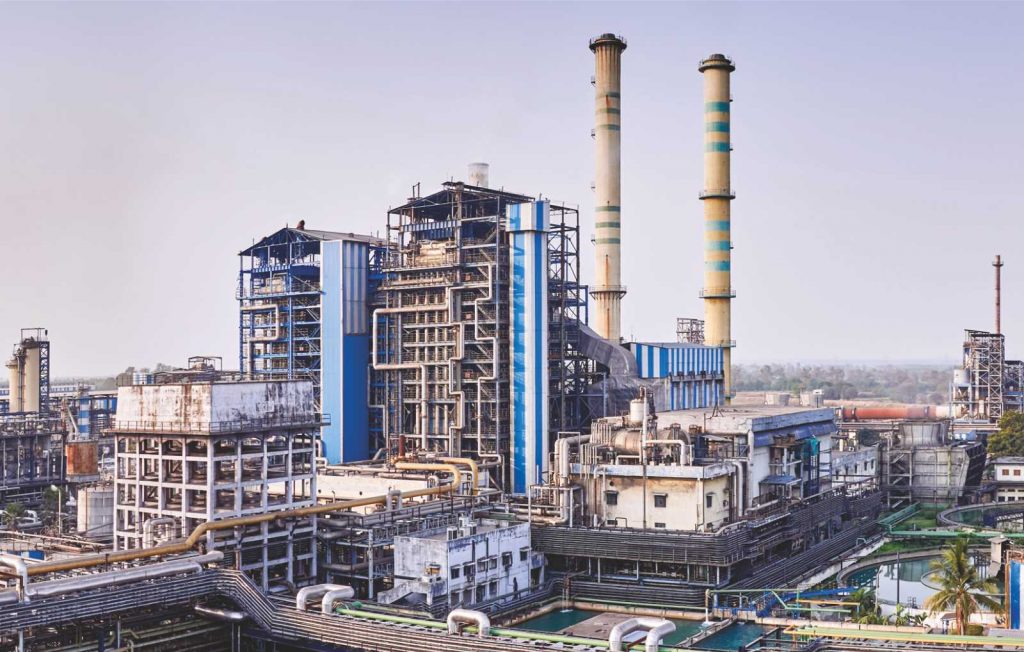
In order to reduce COD and other dissolved substances in the final pulp to a minimum level and also keep the amount of wash water and effluent as low as possible, six counter-current washing stages with ANDRITZ Screw Presses are included. “The 6-stage washing has helped us attain the world record of minimum COD in the final pulp,” adds Mr. Burhanpurkar.
Besides, the effluent from the mechanical pulp mill is sent to the mill’s integrated kraft mill, where it is evaporated, burned, and chemicals are recovered. After this process, clean condensate and oxidized white liquor are sent back to the BCTMP plant. Andritz’s Heat Recovery System at the plant treats the process steam coming from the HC-refiner to produce clean steam which is then used in the effluent evaporation system.
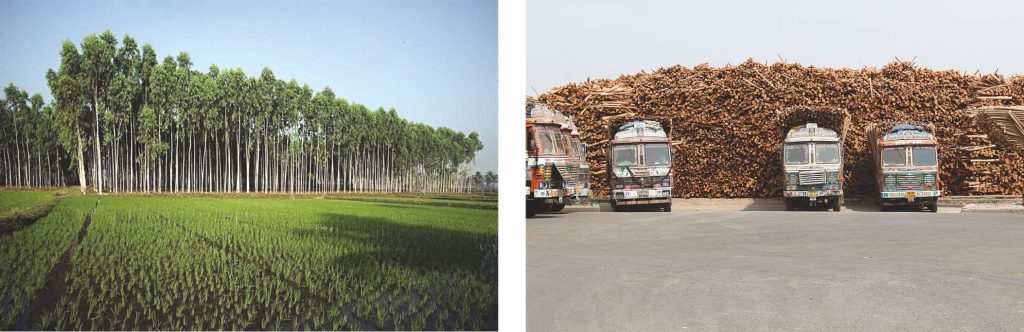
Mr. Burhanpurkar says, “The new BCTMP mill is a model mill in every aspect, and the mill design is such that almost all by products are processed and channelized back in the system, making us one of the best mills across the globe in terms of environmental performance.”