Mr. Thiru. S. Krishnan (IAS), Chairman and Managing Director, Tamil Nadu Newsprint & Papers Ltd. (TNPL), sheds light upon the strategies for water conservation, a detailed discussion on water treatment, two case studies, and the measures adopted to minimise the water consumption.
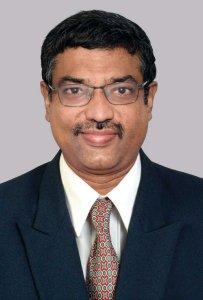
Our water treatment process and wastewater treatment strategies…
Global water use has increased by a factor of six over the past 100 years because of increasing population, economic development, and shifting consumption patterns. For businesses and industries, water stress is one of the main drivers for water reuse and efficiency improvements. Water scarcity is a seasonal phenomenon for manufacturing units like TNPL, which need a large quantity of water and are located near water-stressed areas/rivers. However, seasonal water scarcity has a huge impact on the sustainable operations of the mill throughout the year. At TNPL, we look at day-to-day operations along with water consumption and monitoring. Our water conservation measures focus on recycling and reuse of water and wastewater by identifying appropriate places and purposes with quality and quantity, better monitoring, and leak detection with the right contemporary technologies for treating water and reusing treated wastewater.
This is achieved through dedicated water conservation and management team headed by the unit head and members drawn from all levels and departments. The responsibility of the team is to identify and implement water conservation, and recycling measures at both micro and macro-level and to create awareness among the employees and other stakeholders.
The water treatment plant of TNPL comprises all the modern treatment facilities and storage facilities like a process water reservoir, multi-grade filter to generate filtered water, pressure sand filtration, high rate solids contact clarifier, ultrafiltration reverse osmosis (RO) plant, de-mineralisation plant, etc. The present average consumption for the process is around 35,000 KLD, which includes potable water supply to nearby villages covered under CSR.
Waste Water Treatment Plant
The entire waste generated from the Mill is segregated and collected in two streams:
- High BOD and Low Volume stream
- Low BOD and High Volume stream
The high BOD stream consisting of wastewater from bagasse storage yards and bagasse preparation plants is treated through a bio-methanation plant to generate biogas and used as renewable fuel at a lime kiln. Treated wastewater is further polished in anaerobic lagoons and primary clarifier before mixing with pre-treated low BOD high volume effluent stream.
The low BOD and high volume stream consisting of wastewater from the pulp mill, paper machines, and soda recovery plants are treated through primary clarifiers. The overflow is mixed with partially treated effluents from high BOD treatment and subsequently treated through a secondary treatment system consisting of activated sludge lagoon, secondary clarifiers, sludge thickener (to remove secondary) sludge, etc. The overflow from secondary clarifiers is partially re-used in various plant operations and the balance is sent for tertiary treatment.
Tertiary treatment by Ozone
TNPL’s R&D work to control the colour from the final treated wastewater has resulted in the introduction of a colour removal system based on the ozonation process. The system was put up at a cost of around INR 4 crores. The introduction of ozone, as a tertiary treatment for the treatment of final effluent, is the ‘first-of-its-kind’ in the Indian pulp and paper industry. Apart from the capital expenditure, the company is spending a significant amount on ozonisation. The ozone-treated wastewater having high dissolved oxygen when used for agriculture purposes would improve the soil fertility by way of mineralisation of organic matter into useful nutrients and supports plant growth by promoting a healthy root system, thereby increasing crop yield.
Watch: Evolution of Paper Based Packaging
Our investment into water treatment infrastructure…
TNPL, being a technology-driven company, invests regularly in the water treatment facility to upgrade the treatment infrastructure since its inception. The company has invested more than INR 100 crores in various water conservation projects.
Water consumed per tonne of paper produced…
The current water consumption of TNPL is 32 to 33 m³/MT of pulp and paper.
Measures undertaken to minimise the consumption…
Our approach to water conservation, reuse & recycling is based on the ‘Circular Economy Model’ by circling more by reusing and recycling without treatment, partial treatment, and after treatment inside the mill. Finally, the remaining treated wastewater is used for irrigation purposes by TNPL.
Reuse the water without treatment after usage
All the water used for pump cooling in various process in the plant are collected in a sump through a network of pipelines and collected water is once again pumped back to the water treatment plant as such without treatment to reduce freshwater intake.
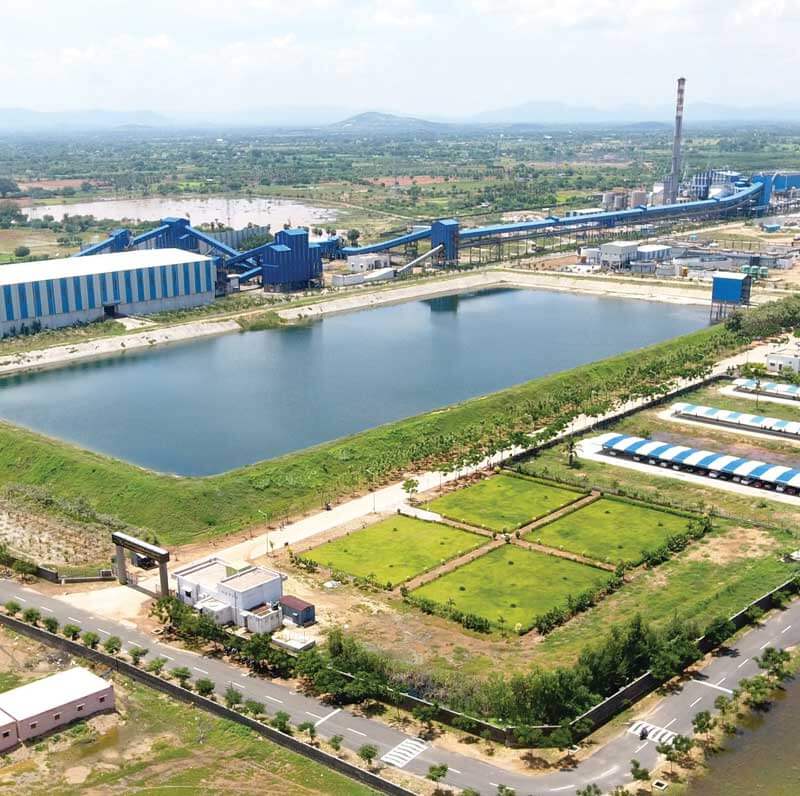
Within the plant
Water used in various processes is reused from one stage of the process to another stage in the same plant, based on the quality and quantity requirements of TNPL.
Recycle water from one plant to other plant
- Paper machine backwater is reused for dilution of pulp in chemical or wastepaper pulp mill.
- Hot water generated from the hardwood fiber line is reused in the bagasse fiber line. This saves fresh water and energy used to produce hot water.
- Process condensate and vacuum pump seal water from the chemical recovery plant are reused in the pulp mill in various stages of pulp washing.
Recycle after partial treatment
The wastewater generated in the paper machine mostly contains suspended solids and it is treated through settling in the clarifier and the clarified water is reused in the backwater clarification system of the bagasse pulp plant. Similarly, the white water generated from the paper machine is filtered through a special filter and filtered water is reused for showers.
Recycle after full treatment
Wastewater, after treatment in the effluent treatment plant, is reused in the bagasse yard by TNPL.
Recent developments with regards to water management and treatment…
TNPL has managed the water shortage in River Cauvery by reducing freshwater consumption through extensive reuse and recycling of processes and wastewater by implementing various plans. A number of water conservation measures have been undertaken to manage the water crisis. There are about 122 projects taken up by which about 10 million m³ of water has been saved. The water savings due to these water conservation projects is about 34.50 million cubic meters per year.
Case Study 1:
Return of pump seal water and hydraulic oil cooling water in Hardwood Street to water treatment plant.
Freshwater used for all the pump seals in the digester, bleaching, and other areas of hardwood fiber line was drained to the effluent channel and wasted. It also increases the hydraulic load in the effluent stream. A project was conceived to collect all pump seal water by laying a network of pipelines and channeling it to two collection pits (based on the fiber line floor topography). All pumps seal water collected in the collection pit was pumped to an existing water storage tank. From there, it is pumped to the water treatment plant and used as a freshwater source. Level controllers and conductivity meters were installed in collection pits and storage tanks to have better control over pumping and water quality. The freshwater saving is about 300 m3/day.
Case Study 2:
Recycling Paper Machine effluent after clarification for bagasse washing and storage.
Freshwater/treated effluent was used in the bagasse handling and storage area. Paper machine wastewater, which contains relatively low TDS, was identified as an alternative to freshwater/treated effluent. It was clarified using one of the clarifiers separately and pumped to bagasse handling and storage area for use. This has reduced average freshwater consumption by 4000 m³ per day and TDS entry to process from treated wastewater.
Also Read: Paper Boat Needs WATER to Float… Save it!
Path-breaking steps taken…
A Circular Economy is a regenerative system in which resource input, waste, and emission are minimised by closing and narrowing energy & material loops. This can be achieved by reducing, recycling, reusing, refurbishing, and recovering resource input used for manufacturing and by minimising wastes and emissions. This is in contrast to a linear economy which is based on the ‘take, make, dispose’ model of manufacturing and use.
TNPL voluntarily made many initiations and is a pioneer in achieving the circular economy models in the various manufacturing process and this helps TNPL to function as an economically and environmentally sustainable company among integrated pulp and paper industries across the globe. A few of the examples of the circular economy concept adopted in the TNPL mill are:
- Biogas from Bagasse wash wastewater: Earlier, bagasse wash wastewater was treated in the open anaerobic lagoon to reduce the organic load carryover and energy consumption in the activated sludge process. Biogas generated from the anaerobic lagoon, due to uncontrolled anaerobic digestion of organic compounds present in the wastewater was emitted into the atmosphere. It is known that biogas contains nearly 75 percent methane, the second-largest greenhouse gas, next to CO2, and has 25 times more global warming potential than CO2.
Commissioning of bio-methanation plant process, anaerobic digestion of bagasse wash wastewater is being done in the closed reactor that makes it possible to capture generated biogas of around 27000 to 30,000 cubic meter per day and use as in house renewable energy, in lime kiln and this prevents uncontrolled methane emission to atmosphere from anaerobic lagoon. The use of biogas in lime kiln resulted in a saving of around 15-18 KL of furnace oil saving leading to a cut down of CO2 emission from fossil fuels to the atmosphere. Together, about 95,000 to 1,00,000 MT CO2e GHG emissions are reduced per annum by TNPL.
- Utilisation of Lime sludge and Fly ash for Cement manufacture: The lime sludge generated during the first stage causticizing process in the chemical recovery cycle and the fly ash generated from the power boilers, lime grits, grits from PCC & GCC plant, bed ash rejects & colour coating kitchen sludge from TNPL unit 2 are issues of concern in inorganic solid waste management. An innovative solution was evolved by combining these two inorganic solid wastes and converting them into high-grade cement. Initially, a 600 TPD plant was put up in the mill and the project was commissioned in 2012. This project is a beacon for other mills, in the direction of converting wastes into wealth besides addressing the concerns being faced in the disposal of inorganic solid wastes. Further, the plant has undergone expansion from 600 TPD to 900 TPD in the year 2015. Further, the CO2 present in the flue gas from the cement manufacturing process is utilised for the production of PCC.
- Recovery of Caustic soda lye during paper machine boil out: Wet end area and associated pulp chests in the paper machines are frequently washed and cleaned by caustic boil out to keep the system clean and to reduce the problem associated with deposits and slime growth. Wastewater generated during the caustic boil out contains a high concentration of sodium hydroxide, which is detrimental to the environment as well as to the effluent treatment process. To avoid this, caustic boil-out wastewater is being separately collected stored in the tanks and reused in the soda recovery plant and also to reduce the caustic make-up.
- Wastewater reuse: The wastewater generated in the paper machines at TNPL is treated by clarifier and reused in the backwater system at the chemical bagasse plant. Process condensate and vacuum pump seal water from the soda recovery plant is reused in the pulp mill in various stages.
- Bio-fuels: Waste pith generated from bagasse and wood dust from wood chipping are fired in the boiler to replace the fossil fuel and to reduce GHG emissions.