Mr. SVR Krishnan, Executive Director (Operations), Tamil Nadu Newsprint and Papers Ltd. (TNPL), dives into the technological advancements and strategies adopted.
“TNPL conceived and implemented the ideas like recovery of the paper machine boilout caustic for the reuse in the soda recovery plant, treatment of the backwater… R&D work is done in the field of ZLD approach, minimising the chloride deposits in SRP, segregating the effluent streams at source and treating them through Mechanical Vapour Recompression.”
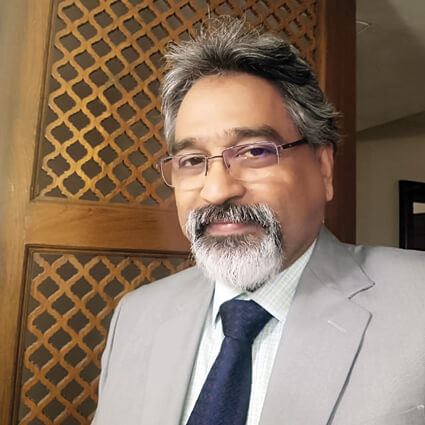
Paper Mart: Please highlight the technology or quality development or up-gradation that recently took place at TNPL.
SVR Krishnan: At TNPL, we go for periodic CAPEX intervention for capacity enhancement with contemporary technologies. During the conceptualisation of any project, right from the selection of the technology and suitable machinery itself, the environment and the usage norms of the natural resources are kept in mind.
TNPL has always been the front runner in implementing the ‘state-of-the-art technologies’ thereby protecting the environment. TNPL is the only paper company in the country to go for a cement plant, just to mitigate the environmental issues relating to solid waste management. We have gone for the manufacture of a 600 TPD cement plant for using all our solid wastes like lime sludge, grits, fly ash, and de-inked pulp plant sludge generated from the Kagithapuram Paper unit. The same plant was upgraded to 900 TPD after the commissioning of the coated packaging board plant in Mondipatti. At TNPL, every waste stream is considered as a by-product to make some other useful products.
TNPL’s packaging board plant at Mondipatti is with the latest technology from Voith (Germany), having all the new generation equipment & components like a hydraulic headbox with dilution control, tandem shoe press, speed flow (metering size press), three-stage blade coating, and soft nip calendar. The entire machine is loaded with the complete automation, having 6 on-line scanners, for monitoring and controlling the process parameters and the final product quality, under Real Time Quality Management (RTQM) at TNPL.
In our journey of continual improvements and the business sustenance, TNPL has installed and commissioned the Gen3 HW fiber line, based on Eucalyptus and Casuarina species, with the capacity of 1,40,000 TPA, supplied by Valmet (Finland) and also the recovery island supplied by Andritz along with other accessories supplied by Bossco and Raumaster were recently commissioned at Mondipatti plant, making it the most modern integrated pulp & paper mill in the country.
These facilities are with the most modern technology to date, resulting in the lowest water and energy usage. It is also to be noted here that the extent of automation implemented from start to end, enables the seamless integration of the entire process with the ERP modules and also IIOT platform.
Watch: Evolution of Paper Based Packaging
PM: Could you shed some light on the R&D and innovations at TNPL?
SVRK: Innovation is something when great ideas are conceived and simply implemented in the process, bringing quantum benefits to the organisation.
In this way, TNPL conceived and implemented the ideas like recovery of the paper machine boilout caustic for the reuse in the soda recovery plant, treatment of the backwater from the process streams for the reuse in the chemical preparation, dilution and also for the equipment cleaning in the process, except the paper machine felts cleaning showers and the usage of the probiotics in the fiber lines for reducing the hazardous chemical usage to a great extent.
A good amount of R&D work is done in the field of ZLD approach, minimising the chloride deposits in SRP, segregating the effluent streams at source and treating them through Mechanical Vapour Recompression (MVR) technology modules, alternate fuels for the cement kilns and power boilers in both the units, superior high-yielding clones of both Eucalyptus and Casuarina and probiotic treatment of the pulp, for reducing the consumption of chlorine dioxide and hydrogen peroxide.
There is good work done by the R&D department in developing tailor-made new products for niche applications like Aura Brilliant Plus, Aura Flute Supreme, Aura Siksha and Aura Gnan grades, for various packaging, cup base and publication segments, etc.
PM: What are your views on the technology and the business roadmap of the company?
SVRK: At Kagithapuram Paper Unit, we will be revamping the total steam and power systems for better efficiency, and economy and to be future-ready for meeting standards to protect the environment. Both PM1 and PM2 will be rebuilt with the latest fourdrinier wire technology for a wider range of production and quality enhancement.
The finishing house will be equipped with the latest technology sheet cutters along with the material handling systems with necessary automation, for enhancing the finished product quality and to reduce the converting and handling losses.
At Mondipatti plant, we will be taking up the second phase of the mill expansion plan (MEP – Phase: 2), with one more packaging board machine with the capacity of 200,000 TPA, one more power boiler and TG. It is also under consideration to add a Eucalyptus-based BCTMP plant, with the capacity of 100,000 TPA.
As both the units have become full-fledged integrated pulp & paper mills, the wood requirement is phenomenal and we will require close to 1.2 million tons of wood to meet this requirement of pulp wood, the company is aggressively doing its farm forestry activities, covering almost 25000 acres of land per every year.
Also Read: Yesterday, Today and Tomorrow of Technology
PM: Please elaborate on some of the Industry 4.0 initiatives taken by the company.
SVRK: Though many companies invested heavily in ERP/SAP systems, the effective utilisation of such systems for business performance is still less and TNPL is not an exception to this. The point is that having understood the gaps, TNPL now focuses on the training of the total workforce for the systems and also putting controls wherever needed. All the quality testing and reporting are done through ERP and also the process parameters are auto-controlled and captured in ERP.
Online data captured through DCS, QCS and Power Bi is flashed to the mobile phones and iPad of all the senior executives and the controls are real-time. There are analyses on the sudden changes and long-term variations to take appropriate actions in the process. The real-time data capturing and subsequent analysis help us in taking very proactive steps towards predictive and preventive maintenance.
As the automation levels are extensive, with contemporary technology, the focus now is to make the operations robust, consistent, avoiding variability, reducing the wattages/losses and improving the bottom line. TNPL very enthusiastically follows the ‘Triple P’ Concept – People, Planet & Profit.