Qualifications: Master of Technology, Indian Institute of Technology, Mumbai, India
Technical Specialization: Steam engineering, Two phase flow, thermal & Fluid dynamic aspects of plant design including Automation and Instrumentation packages
Abstract
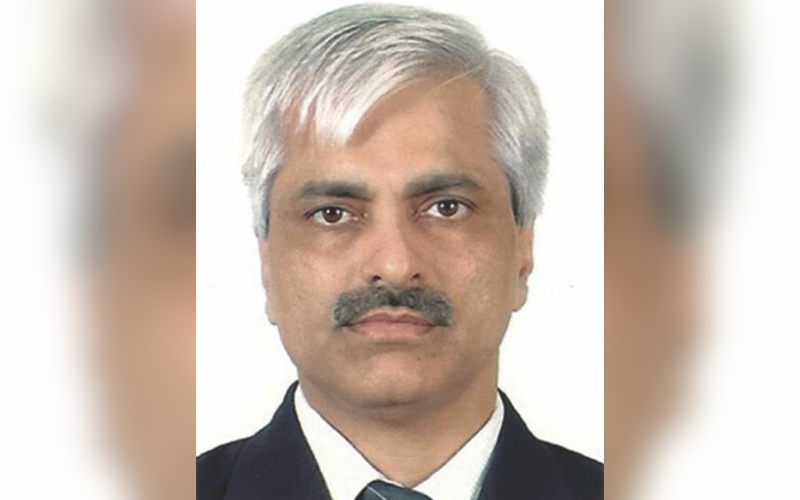
The objective of any Utility manager in a Pulp and Paper mill is to minimize his losses, whether in production or in Energy generation or utilization. Steam forms an essential part of his energy portfolio and is critical to the Paper mill energy costs. However Steam has also been the least understood and probably not very well managed in several industrial plants. The principle of steam management is to ensure that losses are made zero. Our research shows that Pulp and paper mills can reduce steam demand anywhere between 15-25% just be minimizing losses across plants. This does not require rocket science.
Steam has been an ancient topic ever since James watt invented the steam engine in late 1700s. The subject of steam has of course been discussed and debated, but the perception that Steam has nothing more to add is also strong. Thus it is this perception that drives efforts or lack of it!
This paper aims to look at afresh approach to steam management. Rather than look at Steam in isolation, one needs to look at five parameters that connect with steam:
1) Production
2) Environment
3) Energy Efficiency
4) Safety
5) People competence.
This paper thus looks at recent advances that have happened in each of these areas that eventually then impact the specific energy consumption of pulp and paper mills.
From super efficient steam boilers to Boiler house safety systems that enable customers to take action real time using mobile convergence is one such example. The Big data analytics technology is also making its impact on Steam management and Steam trap maintenance systems are being designed that ensure zero loss through steam traps. Intelligent fuzzy logic control systems are already coming in to India where intelligent algorithms are being designed to maintain optimal performance of Paper machines.
Thus any technological advance in steam systems should make the systems affordable, safer and easy to use. Thus this paper aims to look at key technological changes that make steam systems safer and easier to maintain and also make them affordable.
Introduction
Steam has always been considered a ancient topic and thus far removed from any technology focus, The mid 1700’s saw the emergence of the Steam engine and it powered the Industrial revolution. Since then Steam engineering and its associated thermodynamics has remained fairly static and process plants considered this part of the plant as a necessary evil to be managed to the point that it does not cause any obstruction to the production unit. However in the last thirty years, despite the many obituaries written about steam, great focus has been given to the energy efficient utilization of steam and its impact on plant profitability, specially give the spiraling energy costs. This in turn has driven Technology suppliers to invest in the improvement of Steam equipment technology and the increasing convergence of sensors, data and Internet has caused steam systems to become not just smarter but more importantly efficient!
The innovation in steam technology for a long time has been rather slow and evidence indicates how the steam technology evolved rapidly in the 1700s and then slowed down in the 1800-1950 period and then driven by energy costs, a rise in the innovations that were inspired by rising steam costs /fuel costs since the late 1970s. The Internet and data analytics area have converged to make steam systems smarter in the era after 2000.
Pulp and Paper mills in India of late have been providing renewed focus on optimizing their steam networks and also driving down steam consumption and their fuel bills .The entire steam network from Steam boilers, Steam turbines, Steam distribution, Steam utilization and condensate and flash recovery need adequate attention to make a big impact on total fuel bill.
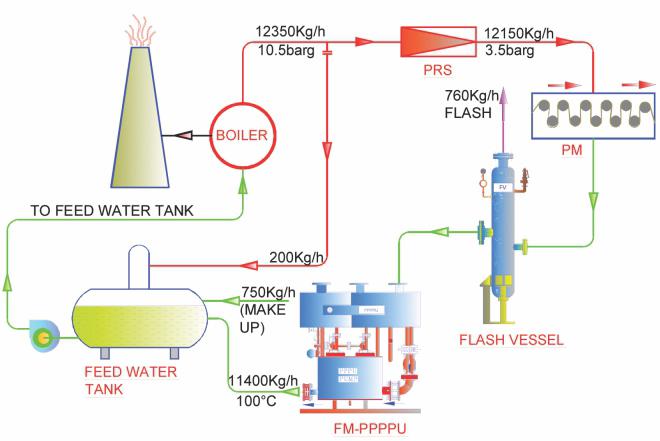
the mass balance within a 150 TPD Waste paper mill
Fig-1 show thermal energy distribution of a typical steam plant in a 150 TPD plant and it says that the potential opportunities for a typical waste paper plant reside in the Boiler house and also the Paper machine. For a large integrated pulp and paper mill, the opportunities also extend to the large steam distribution network and the improvement in the steam mass balance across various sections.
Thus the purpose of any innovation in a typical pulp and paper steam system has to be that cost of steam and consumption of steam be minimized. This paper thus intends to describe the recent advances that have occurred in the Steam systems and their specific applications to the Pulp and Paper industry.
Steam Systems Management
The old adage “what you cannot measure, you cannot control”, applies well to steam systems.
The management of any steam system thus first starts with measurement and that would mean using sensors to measure steam pressure, temperature and flow. The first step is to ensure that the sensors used are of the right type, sized correctly and are accurate and repeatable.
The next step is to make sure that the data generated by these sensors is collected a place where some insights can be gained from their collection, trends and analysis. Thus the need for reliable and continuous data gathering becomes the second step in a steam systems management approach.
The final step, which is obvious, is to act upon the data with some finality! The actions could stem from simple housekeeping to probably exotic fuzzy logic systems that have self actuated control systems.
One aspect of a Steam systems management approach that is often overlooked is to ensure that the results obtained are sustainable over a long period of time. The excitement of having achieved a large steam savings is often neutralized by not adopting practices that are monitored and maintained over a period of time. Thus some means of ensuring sustainability of the efficiency gains is an essential pre requisite.
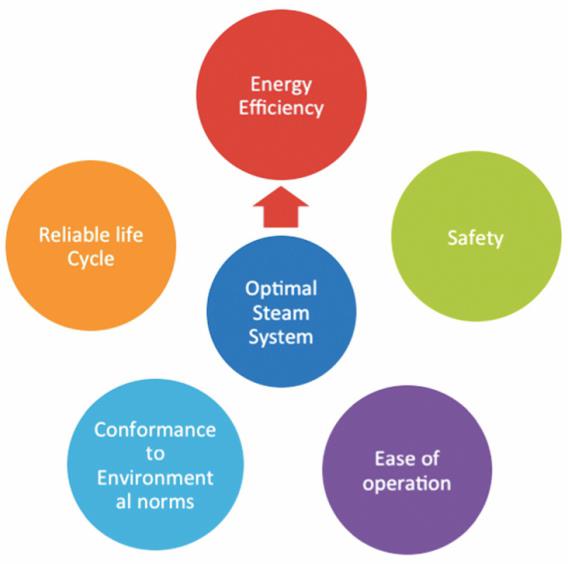
Fig-2 alongside depicts the 5 aspects of any steam Management program and a pulp and paper mill Should evaluate where they stand on each of these aspects.
Energy efficiency could be measured by Specific Steam consumption or specific Fuel consumption.
Safety is measured by number of deviations from Predefined safe levels of critical parameters like Pressure, Water level etc.
Ease of operation is denoted by how operators can run the system without any non conformances
Environmental regulations stipulate adherence to stack dust Loads, Nox and Sox. Finally a reliable life cycle of a steam plant Means uptime of the system that meets the process demand.
The above points thus become the drivers for any product or service innovation and the innovations hitherto described in this paper, aim to serve these objectives.
Some of the technology trends that one observes in steam systems and will become more dominant in the future are:
- Super Efficient Steam Generators with real time Efficiency monitoring&BEESAS.
- Smart Technology in traditional products like steam traps
- Creating a Data connected Steam world. Steam products that are Intelligent and networked.
- Process linked Diagnostics and controls
- Preventive Maintenance systems
- Affordable steam products like Steam meters!
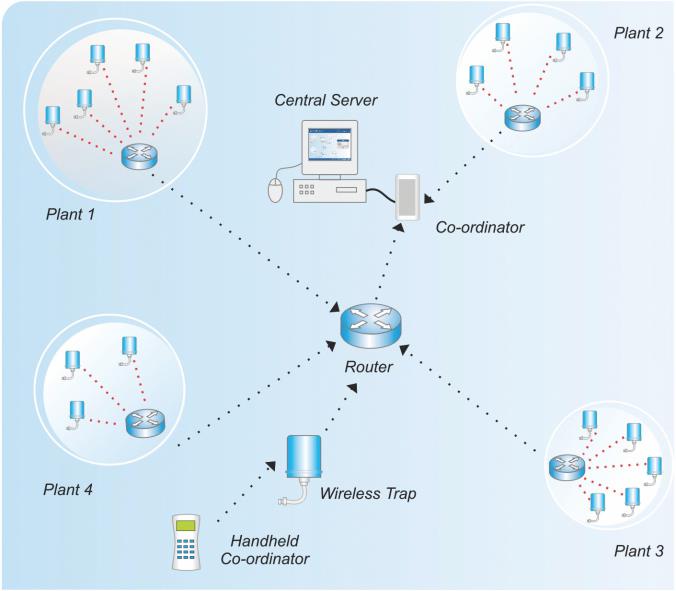
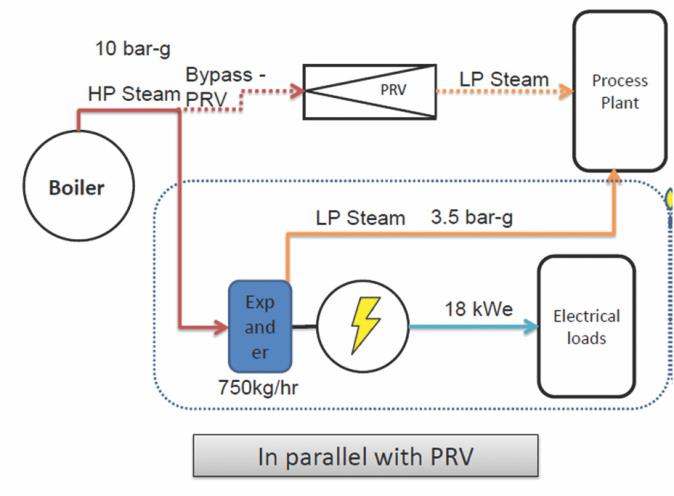
This paper will cover one major innovation in each of the key sections of a steam network- which is the Boiler house, Steam distribution, Paper machine steam and condensate system, and Condensate and Flash steam recovery.
The Boiler House Manager
The typical annual fuel bill of an Indian 100 TPD waste paper based mill would be Rs 50 million (0.75mUSD) and even a 1% saving on the fuel bill would translate to Rs. 5 million, which is easily possible to justify any investment in the Steam system optimization.
The 1% that has been mentioned is just arising out of actions in the Boiler house, not to mention the actions that can be taken in other areas of the same steam network. Thus each of the pulp and paper mills take on the easy target of making a minimum of 1% efficiency gain in their respective boiler houses would make a major impact on their profitability.
When one looks at the Boiler house, there are several issues that come forth:
1) Safety
2) Environmental regulations
3) Energy Efficiency
4) Plant availability
Paper plants need to simultaneously review each of the above norms in their own boiler houses. A system that enables this is now available as an integrated system acronym as BEESAS (The Boiler Energy, Environment Safety Automation System).
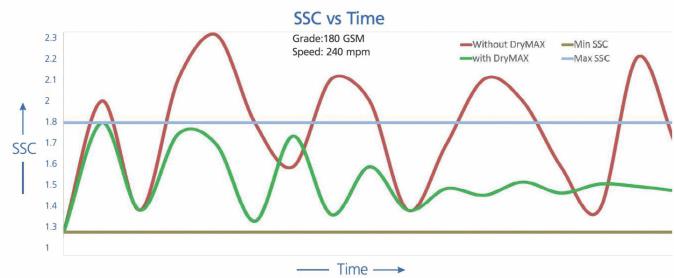
The concept of an integrated system that holistically takes care of all aspects of boiler house operation and at the same time generating real time mobile alerts and being able to connect to the Internet, enables managers and operators to be constantly connected to any possible deviation that may occur in the boiler house and prevent an accident or quickly respond to any deviation in Stack emissions or Energy inefficient conditions.
The innovation in BEESAS is thus the integration of all aspects of critical boiler house operations and combining the Energy and Environment equation enabling complete control on Boiler house operations. Coupled with a service that can be provided by the Technology supplier, which is the Boiler Peak performance service, that combines real time data analytics with control action, sustainability of the fuel reduction could be ensured.
Apart from Safety and uptime, BEESAS ensures That operators get valuable feedback of what Combination of parameters should the boiler be run at to ensure adherence to regulations as well as maximize energy efficiency.
The graph alongside shows a typical correlation For a boiler in a paper mill operated on coal and Shows that 6% excess O2 is the point where SPM, Efficiency is optimized. The optimum point of operation depends on several parameters which a system like BEESAS can detect.
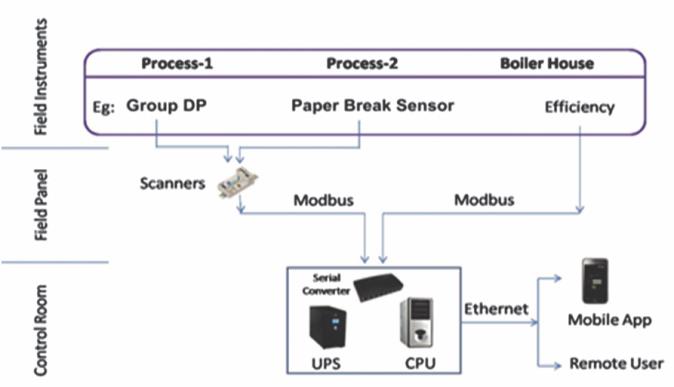
The Wireless Steam Trap System
We selected this innovation as being important because in our surveys of large integrated pulp and paper mills, we find that almost 40% steam traps leak at any point of time and quick action to replace the leaking traps is missing. This leakage loss represents a major opportunity to plug obvious wastage and if there exists a steam trap leak alert then it would minimize a waste that is so very controllable. One might argue that why not install steam traps that never leak! Whatever be the technology or supplier, steam traps do leak and over time and use can develop leakages and these leakages need to be arrested. I would also add that Steam trap designs have become more robust and standards for Steam trap losses have been around now for several years. Thus the Wireless steam trap system provides for an alert that detects if the Steam trap is leaking steam or whether it is stalled and has condensate build up or is operating normally, which is what is desired.
Using a combination of conductivity and temperature sensors which are coupled with a Zigbee sensor network, plants now are able to real time detect steam trap leakages and arrest them as they occur resulting in much lower loss numbers.
In a integrated pulp and paper mill, Wireless steam traps can be installed Which use a star mesh sensor network that connects to each other and to the central Server and provide a a more pro-active leak alert to the operators who maintain the plant.
This technology combines a problem in an age-old product that now rides on top of the latest wireless zigbee technology and also can lead to Internet of Steam traps, giving Process diagnostics and lower steam losses.
Generate Electrical Power from Invisible Steam Loss
Steam engines have been known to the world for over 200 years. However the myth is that Steam engines are an old obsolete technology and thus not be even given a second glance is quite predominant. However many times such old technologies make a comeback because modern day design and manufacturing technologies make them affordable, easy to maintain and also maximize their thermal efficiencies. Thus one more innovation that readers may want to consider is generating electrical power from Steam engines (I am using the word steam engine for a common group of devices that may include Reciprocating engines, rotary micro turbines or rotary axial screw expanders)
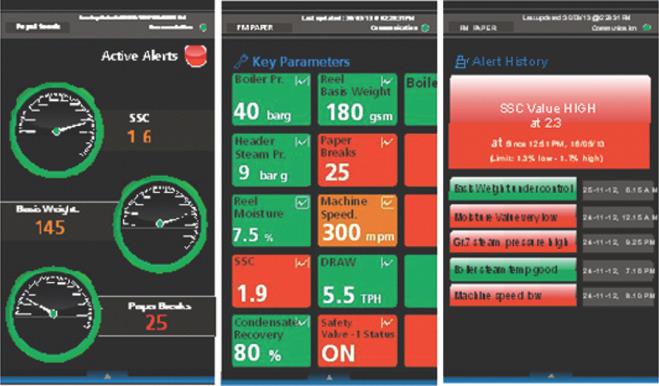
I call this an invisible steam loss, because not many are aware that in throttling steam from 10 barg to 3.5 barg, the available energy is not being utilized and this “energy availability “can be converted to electrical power in a steam turbine or a steam engine or even a screw expander.
The steam engine system schematic is Shown alongside in fig. 5. The steam engine Generates power from the invisible available Energy as steam expands from 10 barg to 3.5 barg. The 18 kwe is a prototype unit that is now running in a Indian pulp and paper mill and the table below shows the opportunity that a 150 TPD plant has in terms of harnessing the invisible energy contained in traditional Pressure reducing stations. Extra electrical power valued at Rs. 160 million (2.4mUSD) can be obtained.
An Intelligent Paper Machine Steam and Condensate System- Drymax
In an earlier section we stressed upon the need for a sustained effort to conserve steam energy and paper machine being the largest steam consumer in a paper mill, it is essential that we create a system that enables steam to be constantly optimized with respect to grades and speeds and independent of operator skill.
One of the major problems that paper manufacturers face today is to maintain the optimum performance of a paper machine consistently. The reasons might be different operators handling the same machine, variety of grades produced by a single paper machine, faulty set points and failure of components.
To address this issue, a tool is developed with an intelligent logic to understand the paper machine and to predict the pressure and differential pressure set points which allow the user to run the machine at optimum performance achieved. Main focus is to maintain the paper machine performance close towards the theoretical/ideal conditions.
Apart from set point prediction, the tool also provides the diagnostics for high steam consumption, locates the dryers with condensate flooding and generates reports with detailed shift wise production information considering downtime. It is a self-learning tool that improves accuracy with respect to time and can also be integrated, as an add-on, with the existing steam and condensate systems.
The Drymax system has been installed in a Pulp and paper mill in India and shows promise for scale up across more plants, given that the consistency and sustainability of steam consumption has been proven and is now ready for commercialization.
Big Data and Internet of Things (Paper Sense)
In the era of broadbandInternet and mobile connectivity, we need to rethink how our conventional steam systems can leverage the power of big data analytics or even consider the Internet of Things- a topic which has consumed manytechnologists. My view of this is that as long as Big Data and IoT (Internet of Things) can deliver sustained customer benefits and provide concrete measurable savings on the ground, the technologies would remain a hype and less of a benefit. However if we smartly leverage this available technology to develop a way to integrate customer operations with a service that can create an ecosystem for energy conservation, both these converging technologies have great substance.
The Effimax, which is a real time Online Boiler efficiency system and is connected to the Internet is already a form of IoT and can be renamed as the Internet of Boilers. The way this connected network of boilers can be further harnessed is to use this data to help other boilers optimize and create a community of boilers, boiler operators and managers who can then implement the insights from a larger population of boilers in pulp and paper mills.
There are several zones and sections within a paper mill that fall under “ No mans land “. This means that sections between equipment or even equipment data that are not correlated to each other, can be sensed and then applying logic engines, we can make sense of that data to either monitor a situation that can affect safety, environment or even energy efficiency. The Paper sense is a technology that makes it easy for paper managers, operators and management teams to sensibly remain connected to their plants without the burden of Data overload. They can choose which parameters they would like to track and then connect that to their mobile devices and be alerted only when there is a deviation. Such intelligent systems further contribute to the uptime and preventive failures of paper mill systems.
Conclusion
Recent innovations in steam systems have been driven by the rising costs of energy (although lately these prices have either dropped due to the Oil price crash and Coal prices too have seen a drop –but the overall trend long-term would be a rising graph and thus the rising energy costs trend curve may be still valid).
All the innovations that were covered in this paper contribute to one or more of the below mentioned objectives:
- To enhance energy savings and bring plant closer to thermodynamic limits
- To bring down costs of Steam generation
- To Control steam heated processes more accurately with reduced cycle time
- To reduce Carbon footprint and reduce Green house gas emissions of plants through fossil Fuel usage
- To enhance safety of steam plants
Finally, objective of any Paper mill steam advances are focusedaround Higher
Production, Better Quality paper withlesssteam. Safety and environment regulations are now becoming stringent and thus Innovations in steam systems now also include many of these aspects.
References:
1) Paper presented on Advances in steam systems – by D.K. Kuvalekar at the Papertech 2015, Hyderabad.
2) Paper presented on Innovations in Steam systems –by D.K. Kuvalekar at Paperex 2015, New Delhi.