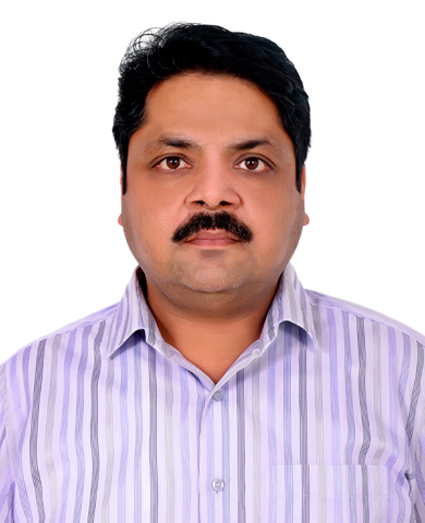
Paper Mart: How do you implement the water treatment process to facilitate the recycling of water and what are your different wastewater treatment strategies?
Deepak Jindal: Based on the studies conducted at our plant, the following are the recommendations and strategies with respect to water conservation:
- The major areas of freshwater consumption are showers on the paper machine, wet washing of raw material and bleaching section of the pulp mill. Thus, the mill must use appropriate techniques to clarify paper machine backwater for further reuse to the best possible extent.
- Use of high consistency pumps helps avoid unnecessary pulp dilution.
- Segregation of colorless/low COD load effluent streams and reuse/recycle with or without treatment in the process to the best possible extent.
- Mill may also use mechanical seal pumps or ceramic-based pumps where water requirement is very less or even mechanical face and lip seal where water requirement is almost nil.
- Use of new generation pulp washer to minimize the water requirement.
In view of the scarcity of water, the use of membrane filtration for the selected effluent stream will be useful in achieving system closure. The mills or association should promote R&D studies to assess techno-economic viability of these technologies. Also, regular water auditing is an important tool that helps the industry to know the current status and also explore the possibility of minimizing water consumption by setting a target/benchmark for individual section of the mill.
The mill should also conduct an awareness programmes for the mill staff working on the shop floor and involve them to participate in giving suggestions to improve water conservation in a particular section.
It must be noted that freshwater conservation leads to saving energy in pumping and handling of relatively smaller volume, lesser material loss, lesser effluent treatment cost and eventually lower the cost of production in an environmentally sustainable manner.
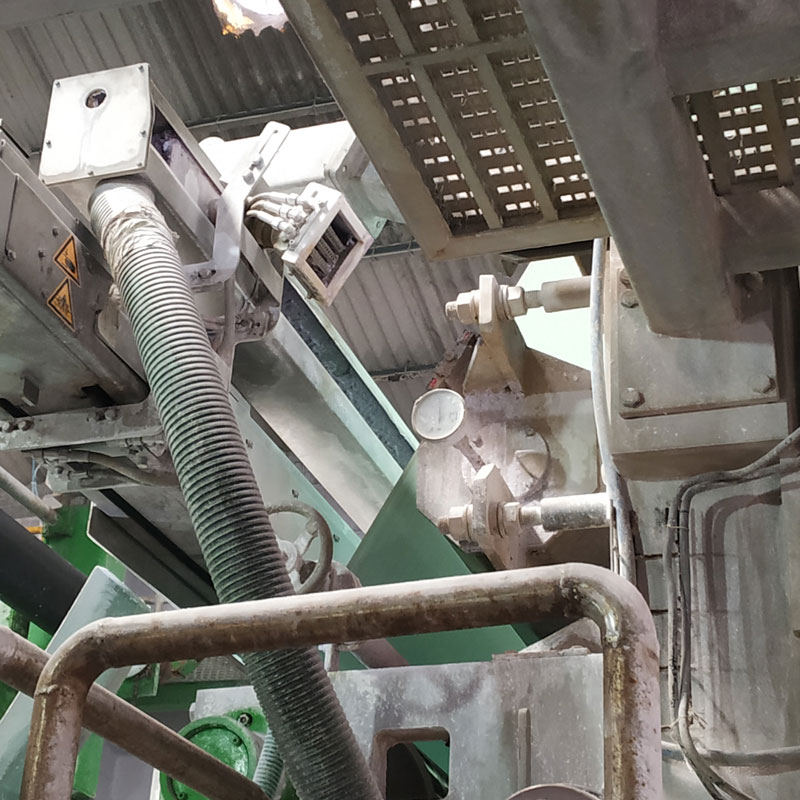
Retrofit strategy for the Conservation of Water in Pulp and Paper Mill.
Reaction system (reactors)
Once the route of chemical transformation of the process is known, the reactor system design is then considered. This involves the examination of a three-way trade-off between equipment, level of conversion and reduction in water consumption. In the case of the bleaching process, the lower the amount of solids product (pulp) at the outlet of the reactor, the lower is the amount of water that is needed to reach the required concentration in the filtering stage. With knowledge of the characteristics of the bleaching reaction and reactor volume, the actual reaction rate can be determined. This information is then used to determine the additional reactor volume needed for more lignin to react.
Also, the amount of freshwater consumption is linked to the level of lignin conversion in the reactor. Since freshwater is used to dilute the reactor outlet stream for it to be filtered downstream, as the amount of lignin that reacts increases, the lower the amount of solids is at the reactor outlet. This condition results in less freshwater being needed for dilution which enables to save water. In addition, warm water is added into the filter for furthering the removal of impurities from the cellulose.
Water use system
At this stage, a water pinch analysis is carried out. Let us consider the washing section of the process – that consists of a series of physical separations for the removal of impurities from the pulp coming out from the digester. This pulp is also known by the name of raw flesh because it has not been bleached yet. During this stage, a large amount of water is used. It is therefore important to ensure the implementation of techniques that leads to the reduction in the requirement of water. The large amounts of water used and the physical nature of the process are conducive for the implementation of the Water Pinch Analysis (WPA) technique which seeks to minimize the consumption of water. These conditions are also appropriate to pose an optimization problem by means of mathematical programming, seeking to reduce the total operating costs. Both techniques are effective for the analysis, synthesis and improvement of the water networks. Furthermore, they take into account the concepts of reuse and regeneration of water that have an impact on the generation of wastewater or effluents while minimizing water consumption.
Water regeneration for reuse
Once exploited and completed all the options for the reduction of water consumption through the measures implemented in the first two layers of the onion diagram, the next step consists of the application of water regeneration techniques. At this level, different techniques for feasible decentralized regeneration of the effluents for water reuse should be evaluated. Among the typical regeneration technologies are those of physical, chemical and biological nature. The selection of the regeneration system should be based on a series of considerations such as equipment cost, operating costs, ease of implementation, availability, etc.
Heat recovery system
The last stage in the hierarchical strategy is to identify the options for reducing energy consumption through the maximization of the heat recovery and the quantification of direct savings generated by the simple reduction of water consumption. In some cases, when the economic scenario is favorable, the savings of steam can be channeled to the production of electrical power in cases where the process plant is integrated with a co-generation system.
Major reasons for high water consumption:
- Low cost of water
- Lack of optimum performance of pulp washers.
- Carrying out of most operations at high dilution.
- Lack of water audit/water balance/assessment of optimum water requirement
- Lack of optimization of washer requirement on decker, pulp washers & paper m/c
- Lack of fiber recovery units or low performance of existing fiber recovery units
- Lack of adequate ETP facilities.
- Mental block in reuse / recycle of treated effluent / back water
- Lack of awareness, trained manpower and monitoring facilities
Steps taken at Naini Tissues for Water Conservation
Installation of an efficient IBS showering system on the paper machine, wet-end to reduce water consumption drastically:
- With the installation of the IBS showering system, water consumption has been drastically reduced from 2900 m3/day to 2200 m3/day, that is, we have been able to achieve the total reduction of 700 m3/day.
Complete recycling of paper machine effluent to pulp mill by passing through Save-all:
- 100% of paper machine backwater is recycled to pulp mill by passing through Save-all and is settled in a clear water tank. It brings about 2200 m3/day reduction in the freshwater consumption.
Installation of state-of-the-art, DCS based Biomethanation plant from Hydrothane (Netherland) for High effluent load drains:
- Effluent from Bagasse wet bulk storage and wet washing are treated in the Biomethanation plant before going to ETP and the recovered Biogas is used as a fuel in the boiler. COD reduction – 80% and BOD reduction – 90%.
Use of ETP treated effluent after Secondary stage for wet washing of raw material and wetting of Bagasse wet bulk storage:
- 100% reuse of treated secondary stage ETP effluent for wet washing of raw material and wetting of Bagasse wet bulk storage i.e. 4000 m3/day reductions in freshwater consumption.
Other measures undertaken by the company includes:
- Counter-current washing in the unbleached section of pulp mill.
- Approximate 70% counter-current washing in the bleached section of the pulp mill.
- Pulp mill unbleached section’s gland cooling is carried out with ETP treated effluent.
- Use of foul condensate from Soda Recovery Plant on ODL washers for pulp washing.
- Installation of Reverse Osmosis (RO) system followed by MVR (Mechanical Vapour recompression) system – Capacity 2000 m3/day
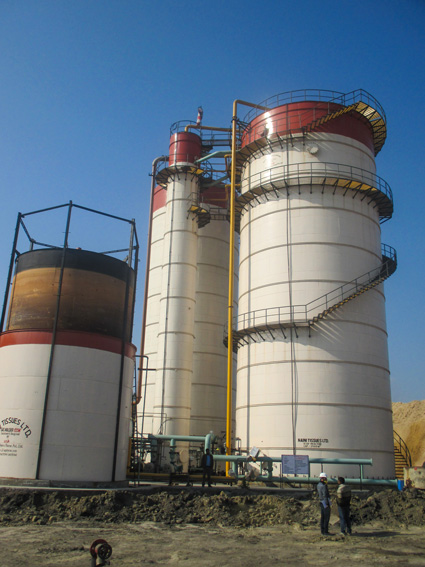
Following the ZLD concept, after ETP tertiary treated effluent we have installed single stage RO followed by MVR for reject handing of RO system. The reusable water recovery (TDS<100 ppm) from the complete system will be 98%. The technology is completely new since the opex is very less as compared to conventional ZLD systems. However, the same is under fine-tuning stage. Moreover, there has been construction of gabion structures going on in the rain drains for high recharge of rainwater.
PM: What kind of investment has been put into a company’s water treatment infrastructure?
DJ: Factors influencing the cost of water treatment includes quality of the raw water, degree of treatment, the volume of water, size of the water treatment plant, treatment process & technology, regulating agencies and norms, recycling water quality, personnel, research gap, equipment, resources and financial status.
Naini Tissues’ investment in the water treatment infrastructure includes:
ETP 10 MLD – Aerobic, anaerobic and tertiary treatment.
- Capex – Rs. 10 crores
- Opex – Rs. 1.25 lakhs/day
Recycling of ETP treated water 2 MLD – RO followed by MVR and ATFD.
- Capex – Rs. 7 crores
- Opex – Rs. 0.8 lakhs/day
Save-all and clear water tank for recycling of paper machine backwater in pulp mill.
- Capex – Rs. 0.40 crores
- Opex – Rs. 0.2 lakhs/day
RTMS system Installation at ETP
- Capex – Rs. 20 lakhs
- Opex – Rs. 1 lakhs/annum
NABL-approved Effluent Testing Laboratory at ETP.
- Capex – Rs. 10 lakhs
- Opex – Rs. 2 lakhs/annum
PM: Could you highlight the pivotal technologies and measures undertaken to minimize the consumption and reduce and treat large wastewater discharge?
DJ: Technologies and measures undertaken at Naini Tissues to minimize the fresh water consumption and reduce waste water discharge include:
Installation of Efficient IBS showering system on paper machine, wet end to reduce water consumption drastically:
- Water consumption reduced to 2200 m3/day from 2900 m3/day after installation of IBS showering system i.e. 700 m3/day reduction.
Complete recycling of paper machine effluent to pulp mill by passing through Saveall:
- 100% recycling of Paper machine back water to pulp mill by passing through Saveall and settling in clear water tank i.e. 2200 m3/day reduction in fresh water consumption.
Use of ETP treated effluent after Secondary stage for wet washing of raw material and wetting of Bagasse wet bulk storage:
- 100% reuse of treated secondary stage ETP effluent for wet washing of raw material and wetting of Bagasse wet bulk storage i.e. 4000 m3/day reduction in fresh water consumption and almost equivalent reduction in waste water discharge.
Other measures undertaken by the company includes:
- Counter current washing in unbleached section of Pulp mill.
- Approximate 70% counter current washing in bleached section of Pulp mill.
- Pulp mill unbleached section gland cooling is carried out with ETP treated effluent.
- Use of foul condensate from Soda Recovery Plant on ODL washers for Pulp washing.
- Installation of Reverse Osmosis (RO) system followed by MVR (Mechanical Vapour recompression) system – Capacity 2000 m3/day

Following the ZLD concept, after ETP tertiary treated effluent we have installed single stage RO followed by MVR for reject handing of RO system. The reusable water recovery (TDS < 100 ppm) from the complete system will be 98%. The technology is completely new since the opex is very less as compared to conventional ZLD systems. However, the same is under fine tuning stage. With the implementation of the mentioned technologies and practices, we have been able to reduce the freshwater consumption to 30m3/ton of paper and wastewater discharge is 25 m3/ton of paper.
PM: Could you tell us about the recent developments taken place in your plant with regards to water management and treatment? What path-breaking steps have you taken to minimize your environmental impact and make your mill environmental-friendly?
DJ: The Company has installed the Reverse Osmosis (RO) system followed by MVR (Mechanical Vapour recompression) system – with the capacity of 2000 m3/day. Following the ZLD concept and after the ETP tertiary treated effluent, we have installed a Single-Stage RO followed by MVR for the reject handing of RO system. The reusable water recovery (TDS<100 ppm) from the complete system will be 98%. The technology is completely new and the operating expense is very less as compared to conventional ZLD systems. However, the same is under fine-tuning stage.