Simon Taurer*
Paper industry is no exception and is under continuous pressure of increment in costs of raw material and energy. Evolution of efficient production procedures, environmental friendly manufacturing methods, keeps our industry growing. Mills are forced to use recycled fibres, add more fillers that are cheaper replacement of fibre and use other additives like sizing and coating chemicals to meet the quality and profitability.
With the gain, also comes some pain. Due to higher use of waste paper, fillers and chemicals, we are contaminating machine clothing, which leads to another serious problem “machine run ability”. If not addressed, it starts spoiling quality of paper, increases energy requirement and damage our environment. Contaminated dryer fabric acts as an insulator and limits the heat transfer to paper web. This means, higher steam consumption or reduced machine output. Solution of this problem to a great extend is to keep the permeability of dryer fabric same or close to the new throughout its life in the machine. This has to be done online and continuously. An ECOfficiency™ concept was developed to keep dryer fabrics clean using little water and air. This efficient innovation opened doors at another area in the machine “wet end”. Standard high-pressure showers at forming fabric and press felts are water-consuming monsters. By using ECOfficiency™ concept, we can bring down the water consumption in these area to as low as 1/10th and leave the rest 90 per cent water for others living on earth.
Problem – Changes of raw material and more additives and fillers
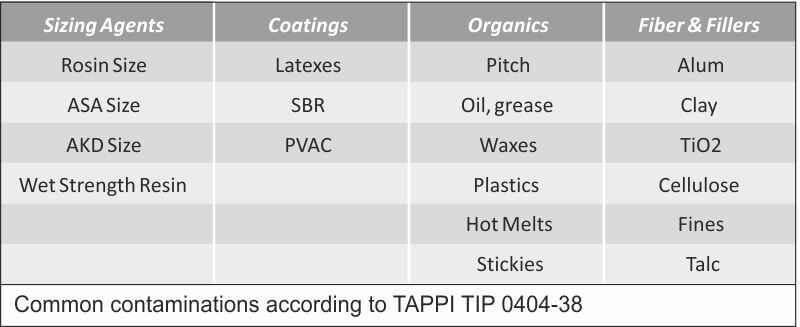
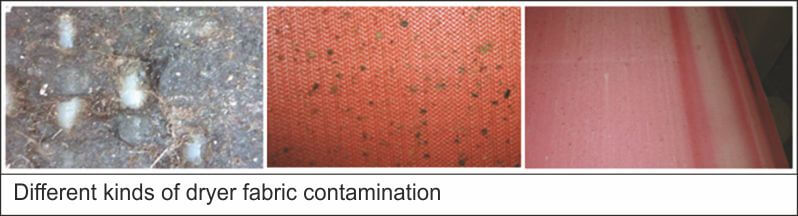
The main problem causing contamination on dryer fabrics is the compound of the raw material. It changed in the past years due to raw material cost, its availability and environmental issues. For example, the use of additives in the fine paper production is increasing. These additives are creating build up on the dryer fabric surface, which causes paper marking, moisture profile issues and an increase in steam consumption. Mills producing brown paper grades try to showcase themselves as environmental friendly by using recycled fibres to the extent of 100 per cent. This looks good and certainly is an act of philanthropy. But such goodwill comes at high price. These mills suffer the most in terms of less machine efficiency due to more paper breaks, poor machine run ability and higher energy costs due to contaminated dryer fabrics. The most common additives used in paper mills are
Solution – Fabric cleaner with the ECOfficiency™ concept
The RossJET system is designed for maximum efficiency achieved by very low energy input and by simple operation. It is very user friendly, as it contains few components that are easy to maintain.
RossJET cleaners consist of four main parts, which are:
1. Pump unit
2. Controls
3. Beam incl. wash station
4. Cleaning head with the ECOfficiency™ concept:
Pump Unit

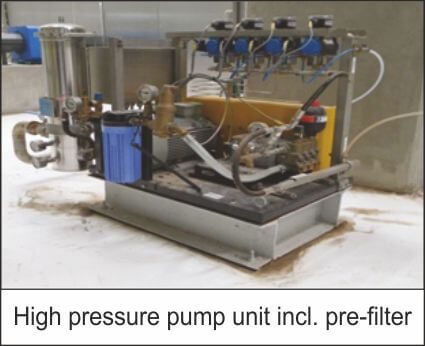
The pump unit contains all the necessary components to operate the hydraulic system in a safe way. The high pressure pump is a plunger pump with three pistons. This kind of pump produces the required pressure and flow by using low energy. For instance, a RossJET cleaning head containing 4pc nozzles with an orifice of 0.2mm operated at 220bar only needs a pump power of 0.54kW. One pump unit can handle multiple cleaning stations (up to 5 cleaning stations).
Controls
The control system consists of all the parts to handle the dryer fabric cleaner easily. Parameterising and operation are done by using an HMI (touch panel). Main functions like start or stop can be connected to the existing DCS by floating contacts. All the drives are operated by VFDs to make the system extremely flexible. To run and to use the system in the most economical and safe way, different features were implemented, like a maintenance reminder, an operator counter or a flow control, to detect plugged nozzle or leakages.
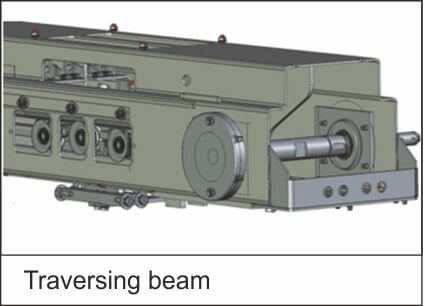
Traversing beam
The beam is made to fit in all positions by keeping the installation space as small as possible. The electrical components (drive and sensors) are mainly outside the dryer hood as well as the park position of the cleaning head. Thus simple maintenance jobs like replacing nozzles can be carried out when the paper machine is in operation. For general maintenance jobs easy accessibility is given by the beam design. A wash station for the cleaning head installed at the park positions completes the beam.
Cleaning head
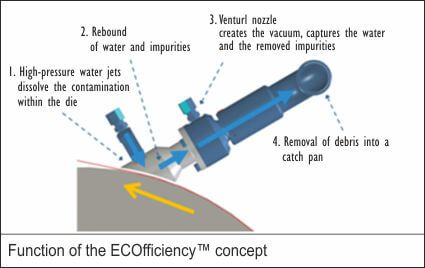
The ECOfficiency™ concept of the cleaning head is the latest development of the usual method to clean dryer fabrics by means of high pressurised water jets. The jets clean the fabric on the paper-side directly on a roll. The needle jet is still the most efficient way for cleaning, as it has the highest cleaning capacity by using low cleaning pressure and low water consumption. The rebound of the water jet from the fabric and roll surface carries the released contamination into the cleaning head. The vacuum created directly inside the head transports the debris further to the save all. The effort to produce the vacuum is the economical part of the concept. No vacuum lines, no additional vacuum pumps or water separators are required but only compressed air with low air consumption.
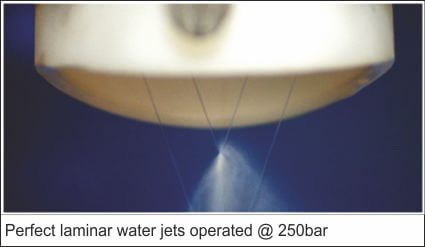
Head rebuilds: Several head retrofits prove the ECOfficiency concept. Head rebuilds were done with older RossJET versions but as well with cleaning heads of other installed units,
Advantages of such rebuilds are:
• Complete removal of contamination from the dryer fabric
• Possibility to install at any position due to the small head, higher suction level and air velocities within the head
• 40 per cent reduction in compressed air consumption compared to the previous head
• No vacuum pump or blower required
• No vacuum hose inside the beam necessary
• Low investment cost
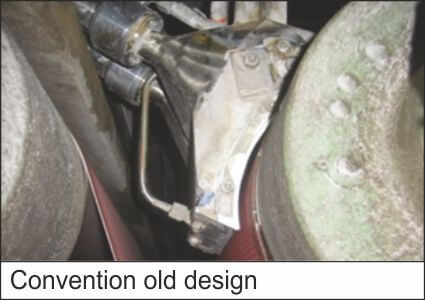
Comparison of water and power consumption at wet end (Forming Fabric and Press Felts) with Electromechanical Micro-travel HP Shower
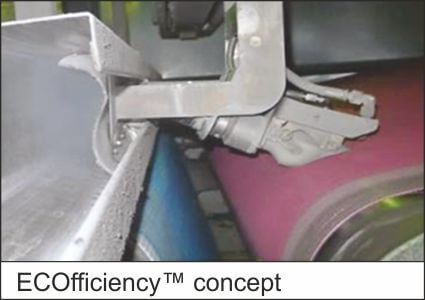
Case studies
• Fluting- 100-130GSM; 500MPM; 100% recycled fibres
Before the installation of a dryer fabric cleaner, the customer had to stop the machine every shift to clean the fabric manually. The fabrics were completely covered with debris. After the first generation of the RossJET was installed, the manual cleaning cycle decreased to once per week. Since the latest generation is installed there is no more need for any manual cleaning – the production time increased.
• VAC compact in operation
• Coated Test liner – 120-230GSM; 1000MPM; 100 per cent recycled fibres
The main issue was the lifetime of the dryer fabrics due to the contamination. The lifetime could be increased by 50 per cent for the first dryer section and 100 per cent for the fabric of the second dryer section. Furthermore, the customer reported less paper breaks and an improved sheet transfer.
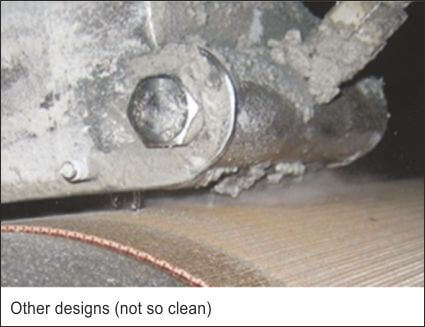
• Writing and Printing – 60-120GSM; 1100MPM; 100 per cent virgin pulp (wood-free eucalyptus)
Contaminated dryer fabrics caused increased steam consumption of 0.1t per ton of paper. Calculated with the annual output the cost for the additional steam is about € 450.000, per year. The RossJET keeps the permeability of the dryer fabric at a high level and thus the steam consumption is kept low – nearly like with complete new dryer fabrics with 100 per cent permeability.
• Writing and Printing – 50-75GSM; 800MPM; 100% virgin pulp (bleached hard wood pulp)
As outlined above, it is mainly an energy consumption issue. The steam consumption increases by approximately 4 per cent when the dryer fabrics are polluted. This amounts to an additional cost of € 100.000 per year. Apart from saving this loss by RossJET, improved quality (no spots due to stickies) is not counted but must be considered too.
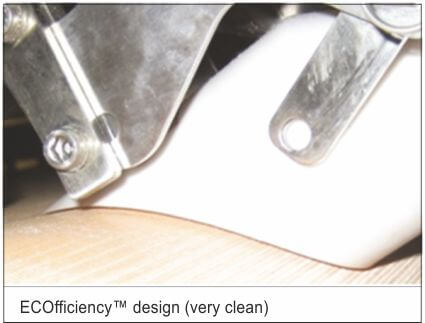
Conclusion
New cleaning concepts, such as the ECOfficiency™ concept, are an important factor for today’s paper production. Previous cleaning devices removed the contamination but were not able to discharge the released debris completely from the fabric surface. Not 100 per cent clean fabrics, rusted or dirty leading rolls and dryers and high consumption of air and water were very common. It is very important to remove the dirt from the fabrics, but making it possible with less air and water is the key. The ECOfficiency™ concept combines both – efficient cleaning and an economical way to do it.
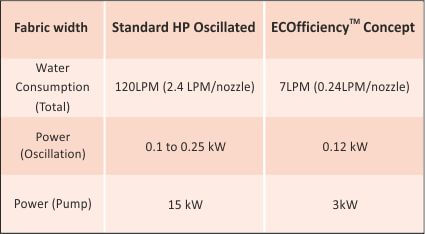
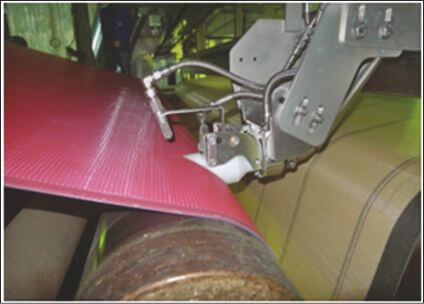
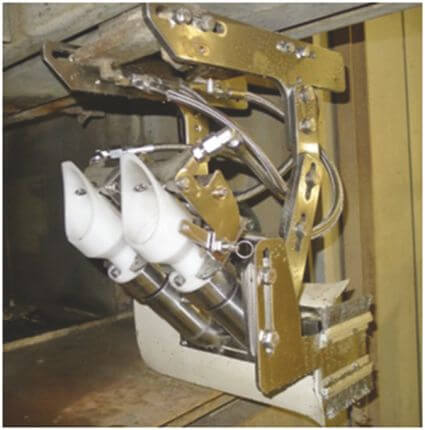
*Mr Simon Taurer serves as
product manager for online
cleaning equipment within
IBS paper Performance Group.