Essity’s mission to produce more-from-less drives an effort to integrate more “circularity” into its business: from responsible raw material sourcing to more efficient production with a smaller climate footprint. The latest example is its innovative project to convert agricultural residue into a bleached pulp and utilize it in high-quality tissue products. ANDRITZ is a technology partner in making this happen.
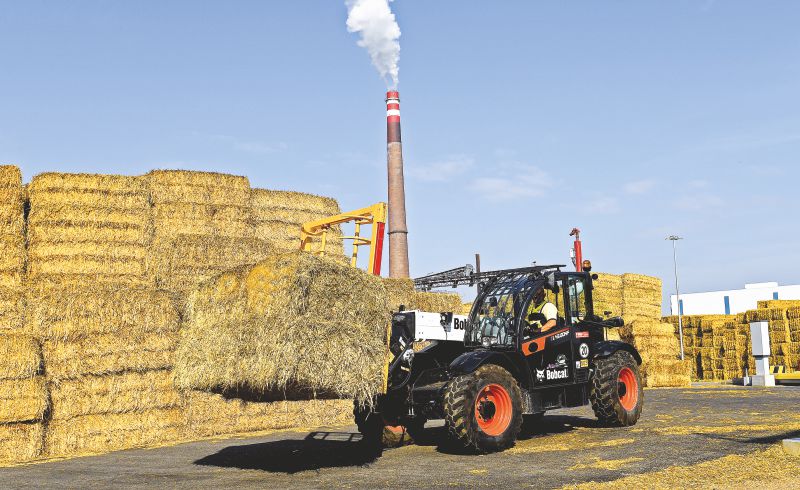
Mannheim Mill Embarks on a Unique Project
Essity’s Mannheim mill is the company’s largest tissue facility in Europe with a capacity of 283,000 t/a. The mill, which was founded in 1884 as a producer of packaging products, has a long and storied history. The mill has for decades produced sulphite pulp on-site, which is unique in its own right. Adding to its uniqueness, the mill has recently started up a new pulping process that will convert 70,000 t/a of regionally sourced wheat straw into 35,000 t/a of bleached pulp.
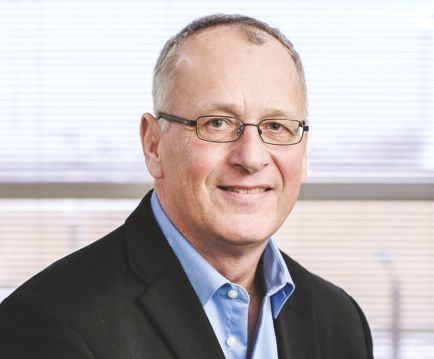
“Wheat straw pulping is certainly not new,” says Mr. Jim Haeffele, Essity’s Vice President Technology, Material Breakthrough. “What is unique here is that this is the first large-scale use of bleached wheat straw for tissue production in the world.”
“By converting agricultural residue into high-quality bleached pulp, we become more circular and can offer our consumers a tissue product with less climate impact”, says Mr. Jim Haeffele, Vice President Technology, Essity.
The wheat straw pulp is blended with the 220,000 t/a of long- and short-fiber wood pulp to produce a full range of tissue and towel grades, including the company’s Zewa brand which is a leading brand in Europe. Tissue and towel products are manufactured on Mannheim’s five tissue machines (four conventional and one TAD machine).
Watch: IVAX Paper Chemicals Interview
Sustainable Fiber Source
Essity signed a license agreement granting exclusive rights with an American company, Sustainable Fiber Technologies (SFT). SFT developed a proprietary process (the Phoenix Process™) for pulping non-wood raw materials in a way that is environmentally friendly and delivers quality comparable to the wood-based pulp at a competitive cost. In this way, Essity can reduce its climate footprint and utilize a material formerly considered to be waste.
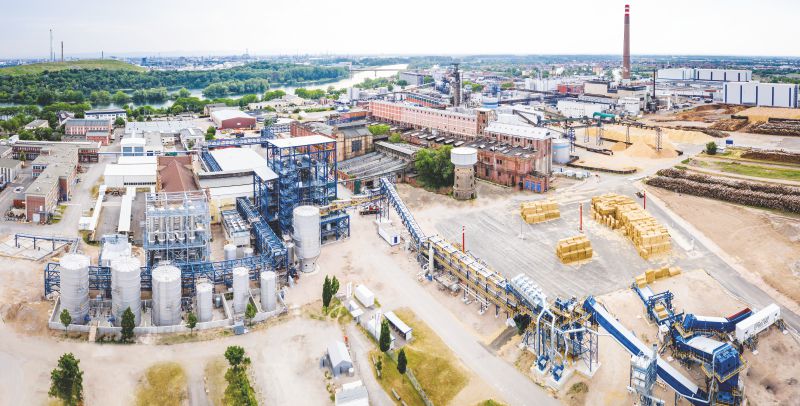
ANDRITZ has been working with SFT for a number of years, supplying equipment for SFT’s pilot plant and some of the company’s commercial applications. As Mr. Markus Pichler, Vice President for Mechanical Pulping Systems with ANDRITZ’s Paper, Fiber and Recycling Division, explains, “We have done extensive lab trials with SFT for various alternative raw materials at our pilot plants in Austria and the USA. That has led us to exclusively employ the Phoenix Process for pulping non-wood raw materials.”
That is why it was a “natural choice” according to Mr. Martin Wiens, Factory and Project Manager for Mannheim’s wheat straw plant, to select ANDRITZ to supply the main equipment.
This includes screening, cleaning, dewatering, chemical mixing, heating, bleach tower discharge, and refining systems. Mechanical installation, commissioning, and start-up supervision were also the part of the scope of supply.
“We have developed unique processing technology that does not exist anywhere else in the world,” Mr. Wiens says.
“The design is based on the SFT/ANDRITZ pilot work and together we managed to go from concept to reality in a little over two years. That is really impressive!”
Bleached Quality for Tissue
For the uninitiated, wheat straw is considered an “agricultural residue” – cellulosic material that remains in the farmer’s field after a grain harvest. Up to about one-third of the residue can be tilled back into the field to maintain soil integrity, but what to do with the rest? A portion is used for such things as animal bedding.
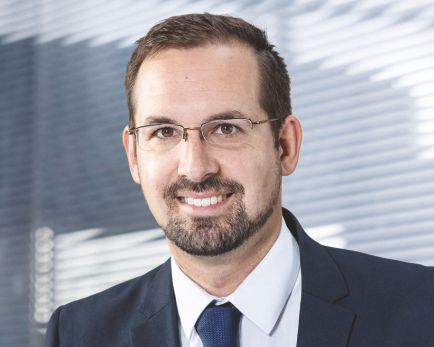
Mr. Haeffele and his colleagues began discussions with SFT in 2017 because Essity was looking to secure wheat straw pulp to replace OCC due to instabilities in the recycled market at that time. “Unbleached wheat straw pulp was being produced at commercial scale primarily for packaging grades, but the more that we discussed the process with Mr. Mark Lewis (Founder and CEO of SFT) the more we began thinking about installing our own line for bleached wheat straw pulp,” he says.
“The raw material is so different from wood fibers that it behaves differently in every machine from what was expected. We had to confirm our assumptions about pulp properties and fiber development for each process step,” says Mr. Markus Pichler, Vice President for Mechanical Pulping Systems with ANDRITZ’s Paper, Fiber and Recycling Division.
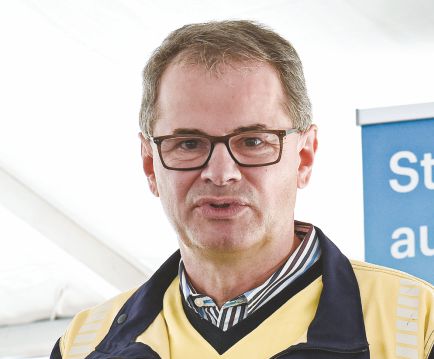
Lewis was excited by the idea. “We looked forward to working with Essity and ANDRITZ to prove out the pulping and bleaching processes on a large-scale,” he says. “Pulp produced with our Phoenix Process has characteristics comparable to virgin hardwood pulp and superior to recycled fiber. The process uses significantly less energy, water, and chemicals than conventional wood pulping and is sulfur-free.”
Timeline
The €40 million investment in the wheat straw plant was approved by Essity’s board of directors in 2019 and construction began in May 2020. The plant started up in August 2021. Project activities were performed in parallel, Mr. Wiens explains, to keep to an aggressive schedule. “We already had started erection while we were still finalizing procurement of some of the equipment such as piping, equipment, etc.,” he says.
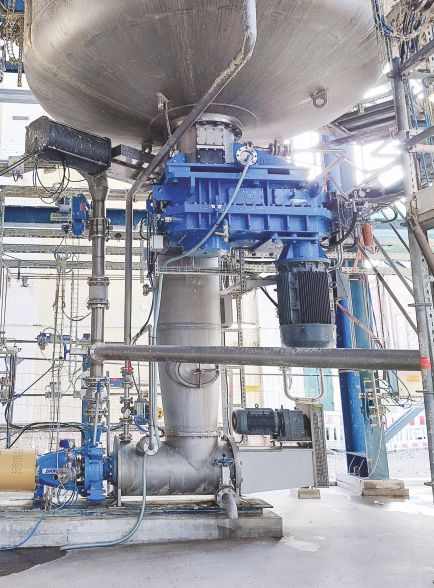
“The design is based on the SFT/ANDRITZ pilot work and together we managed to go from concept to reality in a little over two years. That is really impressive!,” says Mr. Martin Wiens, Factory and Project Manager, Essity Mannheim mill
As with virtually every project, there were daily surprises in erecting and starting up Mannheim’s straw pulp plant. “This mill has been in existence since 1884 and in excavating the site chosen for the wheat straw plant, we found old foundations, tunnels, and other structures which had to be removed and filled in,” Mr. Wiens says. “Construction occurred during the hottest summer and the coldest winter that we had experienced in Germany in many decades. Just to add to the challenge, we worked through the COVID-19 pandemic as well. Throughout it all, we prevailed and ANDRITZ was a very professional and flexible partner.”
“Straw is not wood chips”
In the run-up to the project, several trials for dewatering, refining, bleaching and the mixing behaviour of wheat straw were conducted at ANDRITZ’s fiber preparation pilot plants in Austria and the USA. Mr. Pichler of ANDRITZ notes, “We were of course familiar with the SFT process, but most of our trial work was at small scale. We needed to do extensive testing of the wheat straw to specify the correct machine sizing. We had to confirm our assumptions about pulp properties and fiber development at 100 t/d scales.”
“The raw material is so different from wood fibers that it behaves differently in every machine from what was expected,” Mr. Pichler explains. “We had to confirm our assumptions about pulp properties and fiber development for each process step.”
Straw pulp was shipped from SFT’s pilot plant in the USA to Graz (Austria) to run dry-crepe and structured (TAD) tissue trials at ANDRITZ’s PrimeLine Tissue Innovation and Application Center, the world’s most modern tissue pilot plant. “This facility brings together customers, suppliers, and R&D institutes in a very special way to create solutions,” Mr. Haeffele says. “ANDRITZ’s approach to R&D is very sophisticated and professional.”
Even with the trials and pilot plant work, there have been surprises – some positive and some challenging.
“Producing bleached wheat straw pulp of tissue-grade quality is complicated,” Mr. Haeffele explains. “Achieving wood-like characteristics for brightness and drainage from wheat straw is not a simple matter. It sounds simplistic, but straw is not wood chips. It has been a learning curve for sure.”
One of the most positive learnings so far is that the wheat straw pulp has excellent strength characteristics. “We originally thought that it would be more of a hardwood replacement,” Haeffele explains, “but because of the high tensile characteristics, it is a suitable softwood replacement.”
Also Read: Haber: Size-Press Automation through eLIXA®
The new cellulose made from straw is as soft, tear-resistant and highly absorbent as conventional cellulose made from wood fibers. The pulping process uses less water, chemicals, and energy than wood fiber pulping.
Valuable Byproducts
A byproduct of the wheat straw processing at Mannheim is lignin (minus the sulfur that is present in wood-based lignin which is produced via standard pulping technologies) that is valuable as a feedstock to produce biopolymers. These biopolymers can replace oil-based chemicals in dust abatement, corrosion inhibitors, binders, feed, cement additives, and other speciality chemicals.
“This fits our more-from-less philosophy completely,” Wiens says. “We don’t waste anything. We take what used to be agricultural waste and make tissue. From the byproducts, we could even make the packaging for our products – bio-based, biodegradable, compostable, and recyclable. This is a real circular economy.”
New Infrastructure Requirements
In developed countries, there is significantly more agricultural biomass available than wood biomass. In Europe, Essity estimates there exist about 15 million tonnes of wheat straw each growing season.
Mannheim is receiving its raw material from about a 300 km radius around the mill, the same radius that they source their wood fiber, according to Wiens. “Since this is a new fiber source for us, and since the fiber procurement is done once per year, we had to develop our own infrastructure for the centralized purchasing, gathering, storage, and transport of wheat straw,” he says.
The mill keeps about 1500 tonnes (5-day supply) at the mill site. The remaining supply is stored at special facilities nearby.
Security and Flexibility
“There are many benefits to this project in terms of having an alternative fiber source that meets our sustainability ambitions while reducing our climate footprint and improving our cost efficiency,” Mr. Wiens says. “Adding to our existing expertise in processing sustainable wood-based fresh fiber and recycled fibers, our growing expertise in processing alternative fibers gives us much more security and flexibility in sourcing. This will allow us to capitalize on fiber availability and pricing in the future.”
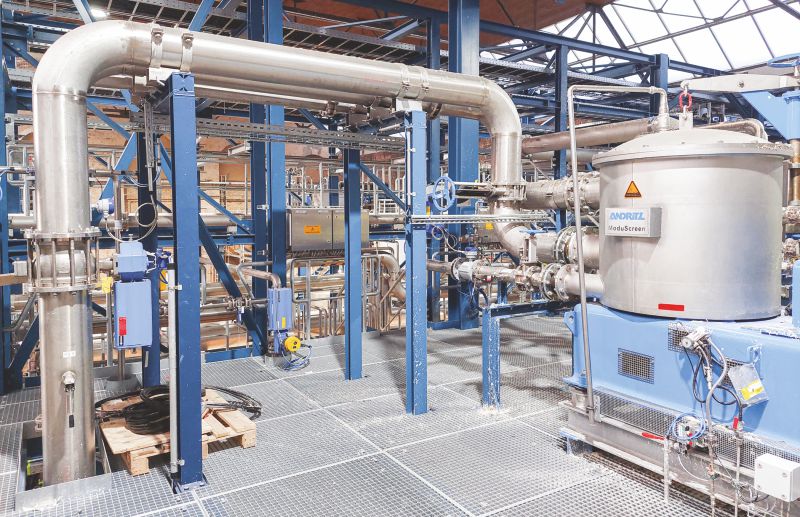
“Globally, half of all straw goes unused,” Mr. Haeffele adds. “By converting agricultural residue into high-quality bleached pulp, we become more circular and can offer our consumers a tissue product with less climate impact. Mannheim is showing that there is an alternative way to produce tissue. The world needs alternatives to meet the increasing consumption demands in developing countries.”