The moisture profile stability provided by a Metso IQAquaPro has meant more uniform paper strength properties, fewer rejects and claims, and a handsome ROI.
The cross-direction moisture profile of paper and board is often the most critical quality parameter since it affects so many other sheet properties – strength, dimensional stability and, most importantly, how the sheet runs in customers’ printing and converting machines. Running at the right average moisture is important, but even point-to-point quality is the vital requirement.
So with improved customer quality and a good return on investment in mind, the Cascades East Angus mill in Québec’s Eastern Townships installed a Metso IQAquaPro CD moisture profiler on their number 4 kraft paper machine. The new moisture profiler and associated cross-direction controls were added to an existing Metso PaperIQ QCS and system and Damatic XDi DCS system.
Normand Langlais, Paper Mill Superintendent, provides statistics which show the good return on investment for the profiler and controls.
These include:
• Moisture profile rejects were reduced by about 84% in 2008 compared to 2007.
• The cost of claims was down by 40% in 2008 compared to 2007. This was mainly related to the IQAquaPro start up.
• Average sheet moisture increased from 5.0% to 5.7%.
• Steam consumption was reduced by about 2.7%, as a result of improved profiles and other dryer section improvements, and machine speed was increased about 2.9%.
On the all-important quality side, he reports much improved uniformity of paper properties – notably moisture and related strength properties – and Cascades East Angus’ customers have noticed the improvements.
Moisture uniformity affects strength uniformity
Langlais explains why moisture uniformity is so important to the mill and its customers. “A big difference in point-to-point moisture in a roll affects the sheet tear and tensile strength. Some of our clients slit our paper into 1 inch (2.5 cm) bands. If there is a big difference in moisture it is difficult to slit.”
Number 4 machine is a 122 inch (310 mm) trim specialty machine making about 55 kraft and recycled paper grades with grammage ranging from 37 to 120 GSM. These grades include kraft envelope papers, butcher wrap, grease resistant paper for pet food bags and extensible paper, which is used for construction. The machine is equipped with a Clupak unit for stretchy extensible paper and a size press for flat papers.
Stability needed quickly
With typically 4 grade changes per day, the machine is often in a state of transition and it takes some time to stabilize the process and product quality. Minimizing the time required to level the moisture profile and achieve prime quality is critical and that is why the mill needed a quick, responsive way to control. Adding the profiler and controls to the existing Metso equipment was a technically sound way to go, the mill staff reasoned. The new profiler was interfaced to the existing control system via a new metsoACN module.
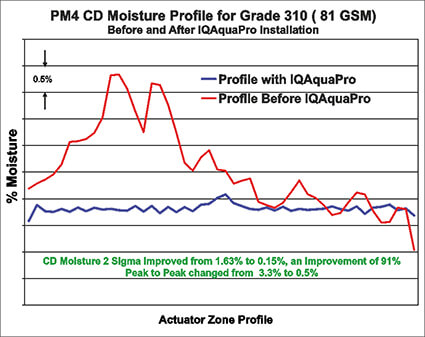
The expected ROI would come from reducing mill waste and customer claims. Also, some energy savings could be possible if the sheet could be run with higher moisture content. The mill had previously invested in machine upgrades to improve the moisture profiles and save energy – including a uni-run felt section, new siphons and changed press crowns. But Langlais says they needed to do more to get better results.
The IQAquaPro is located on the first top drying cylinder after the machine’s size press and Clupak unit. This location gives the moisture lots of time to penetrate the sheet before it reaches the reel. It was a tight fit in an older machine, but the installation logistics were effectively worked out by the mill staff & Metso. Felt roll positions were changed to maintain the same dryer felt length.
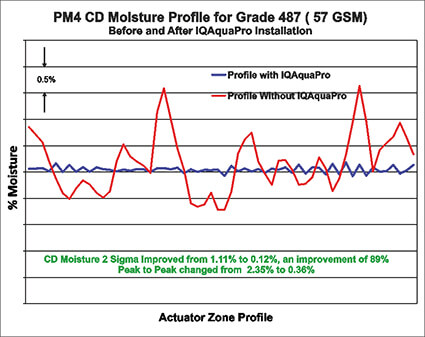
Serge Tremblay, project engineer, reports that the complete profiler support equipment package provided by Metso, including atomizing air and water supply and treatment equipment, helped to minimize the mill’s engineering requirements. “It was easy to connect; we just had to supply the platform,” he says. The profiler on the machine was installed during the Christmas 2007 shut and was up and running in early 2008. Tremblay reports the project was under budget.
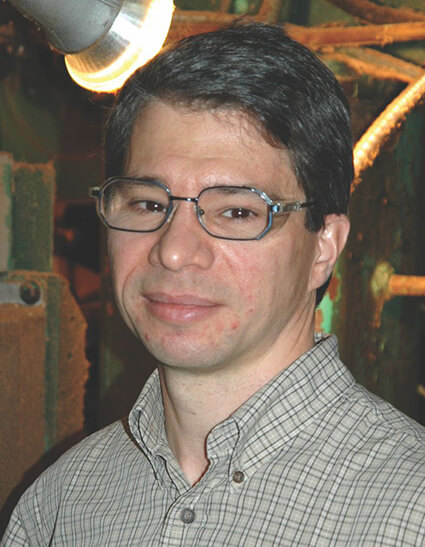
“Instant good results”
Normand Langlais says the results – much improved moisture profiles – were noticed almost instantly. “It has made a big difference in the control of the machine. The operators accepted the system very quickly“, he says. The operation of the unit is trouble free as no streakiness or dripping problems were noted after the startup.
Metso guaranteed the control performance on certain key grades. The results are shown in Figure 1.
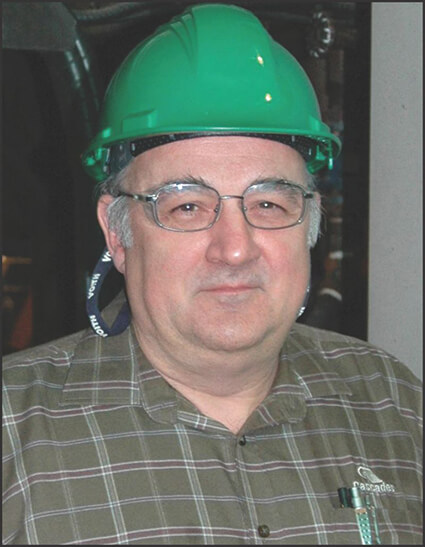
2-sigma CD moisture variation has been reduced by about 90% on two key grades. Most importantly, the peak to peak variation has been reduced to 0.5% or under. This means the sheet strength properties across a small span are uniform as well. And, as the final proof of perfor-mance, that uniform sheet runs well in customers’ converting machines.
Normand Langlais “The results – much improved moisture profiles – were noticed almost instantly. “It has made a big difference in the control of the machine. The operators accepted the system very quickly, “he says.
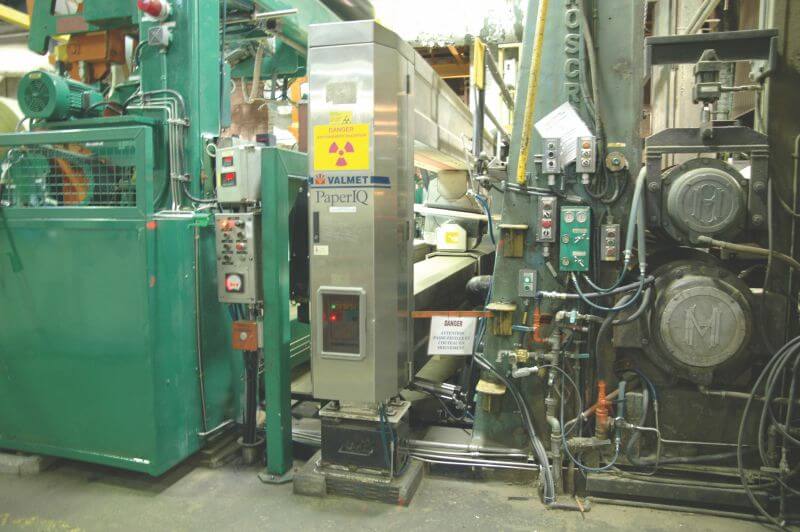
The new moisture profiler and associated cross-direction controls were added to an existing Metso PaperIQ QCS and system and Damatic XDi DCS system.
Serge Tremblay reports that the complete profiler support equipment package provided by Metso, including atomizing air and water supply and treatment equipment, helped to minimize the mill’s engineering requirements. “It was easy to connect; we just had to supply the platform,” he says.
IQAquaPro control hardware is located in cabinets on the machine drive side.
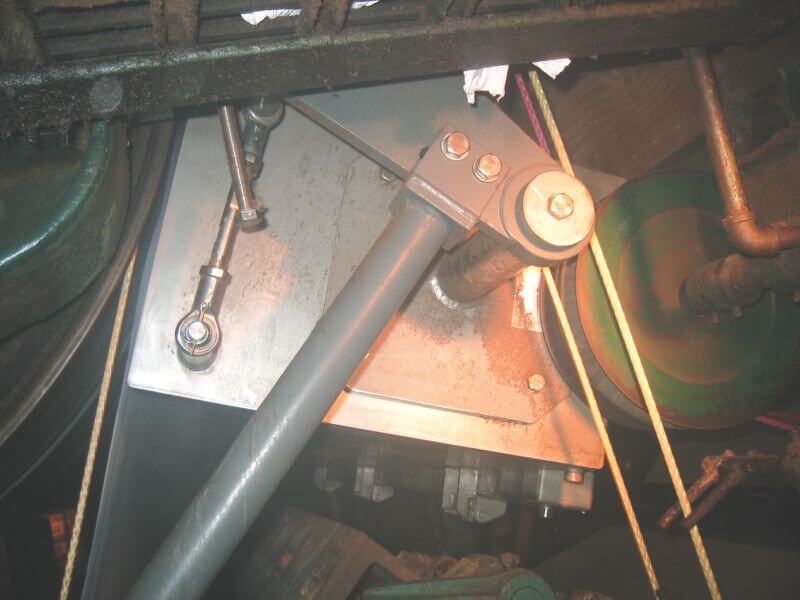
The IQAquaPro is located on the first top drying cylinder after the machine’s size press and Clupak unit. This location gives the moisture lots of time to penetrate the sheet before it reaches the reel. It was a tight fit in an older machine, but the installation logistics were effectively worked out by the mill staff & Metso.