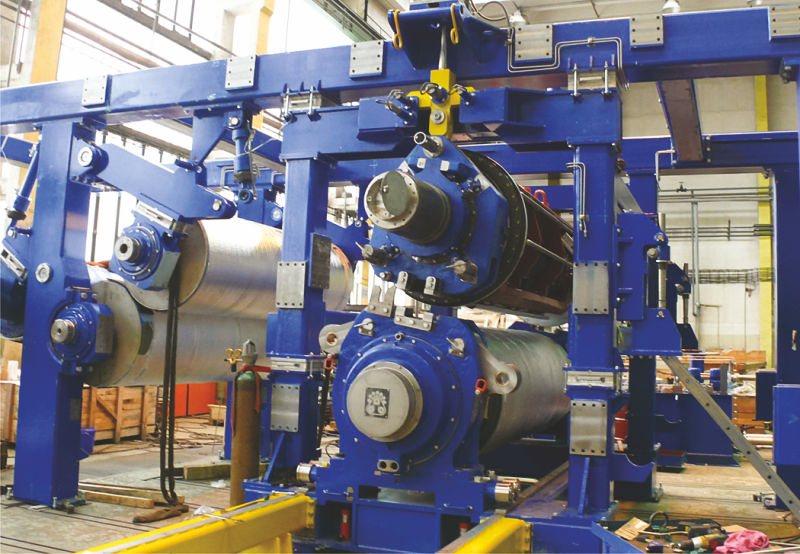
In 2014, PAPCEL Group Czech Republic signed a contract to supply technological parts for PM 1 for the paper concern Mariyski CBK, Russia. PAPCEL is realizing a reconstruction of the PM wet part for production of fluting/liner papers & bag papers to increase the machine capacity to 187 tpd for packaging papers and to 144 tpd for bag paper. New parts are constructed for the speed of 800 m/min. The existing press part, consisting of four continuous presses with felts on bottom rolls, will be completely replaced with a new press part, consisting of a combi press with two nips in the first position (picking up from the wire part with help of a pick-up roll) and a Shoe press with a bottom and a top felts in the position of the second press. The new press part is supplied as a complete set, including a supporting structure, press and guide rolls, doctors, felt washing, stretching, automatic regulation of felt run, water off take tanks, service bridges. Washing of all the felts is done using low-pressure and high-pressure oscillation tubes, cleaning of felts surface is assured by suction tubes with ceramic lining. Threading from the wire part into the first press is by a pick-up roll, threading from the first press into the second press is by an air threading scraper, threading from the second press is by a dry transfer roll into the drying wire and into ropes of the rope threading of the drying part (circuit of the first drying section – the customer will add the rope threading in the drying part). Pressing of the press rolls is hydraulic. The equipment is controlled from a separate control desk connected to the central DCS.
Besides the press part, PAPCEL realizes an overall completion of the wire table and a modification of the machine drying part where it is installing new stabilization boxes, doctors for drying rolls and drying fabric stretching. The machine MCC system will be completely modified within new supplies.