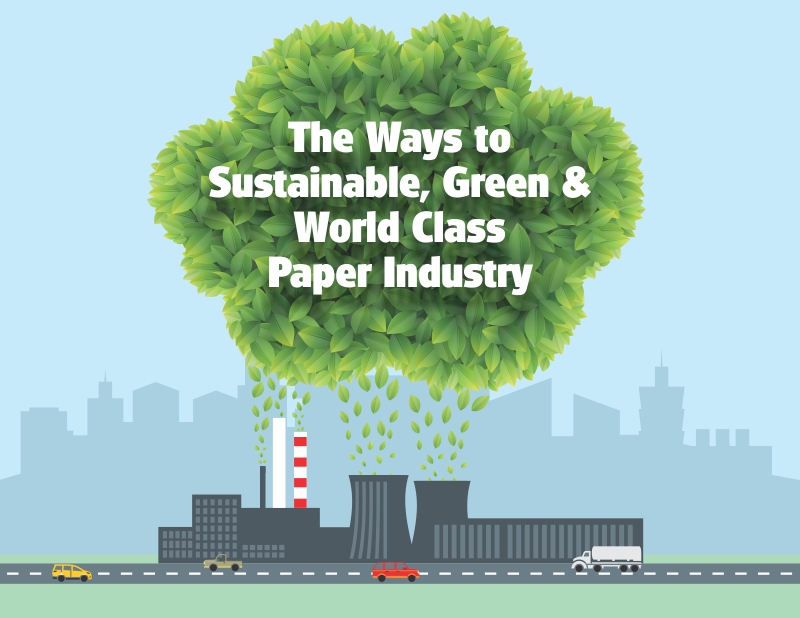
PaperTech 2016 again provided an impetus to a green movement that the Indian pulp and paper sector earnestly wishes to pursue in order to become economically viable and environmentally sustainable.
CII-Sohrabji Godrej Green Business Centre in partnership with Indian Paper Manu-facturers Association (IPMA) organized the 10th edition of PaperTech 2016 on August 22-23, 2016 at HICC, Hyderabad. CII-Godrej GBC with the support of all the stake holders of Indian paper sector has been helping the Indian pulp and paper industry to achieve the world class standards by facilitating its energy and environment performance improvement.
During the 10th PaperTech event, a good turnout of delegates from the paper industry vindicates that the initiative has been very well received by the Indian paper industry over the years. Among the principal objectives of the event were disseminating the information on latest technologies for energy efficiency, water and environment performance improvement; to facilitate sharing of best practices amongst Indian pulp and paper plants; involving more paper plants including small and medium plants in the activities related to ‘Make Indian Pulp and Paper Industry World Class’ for their benefit; sharing the best practices amongst the Indian Pulp and paper Industry, etc.
The event on August 22-23 tried to recapitulate the efforts by the paper industry in the direction of sustainability and resource conservation, and provided a momentum for future course of action on that front. A parallel between the cement and paper industry was drawn and a collaborative action was sought to address some of the common challenges faced by both the industries.
Making the Paper Industry Green
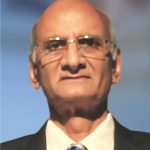
“In this conference, we will discuss energy, environment and water. Papertech is a forum for collective efforts and pro-active thinking.”
Opening the PaperTech 2016 with his address, Mr. K. S. Kasi Viswanathan, PaperTech 2016 & MD, Seshasayee Papers and Boards Limited, emphasized the urgency of events like this in the wake of CPCB’s new national charter for water recycling and pollution prevention in pulp and paper industry. He said, “The new national charter has much stricter norms for fresh water consumption, effluent generation, and quality of treated effluents. Tightened norms on water consumption will put tremendous pressure on us. As on one side, we have to reduce the water consumption, on the other side we need to reduce the concentration too. So, all these are big issues that need a lot of understanding and discussions to be solved, for example, we need to study how different mills are trying to tackle various issues.”
He said that in order to become green the industry would have to focus using less fuel and which can be achieved by using biomass and other renewable resources like wind or solar. “We have to be energy efficient if we have to become green. This will also lead to controlled COD. So, being green is another major focus area for our industry. Another major challenge is of technology upgradation and threat from imports,” said he. “In this conference, we will discuss energy, environment and water. Papertech is a forum for collective efforts and pro-active thinking. Here, we will talk and gather ideas from different experts to see what can be applied to our industry.
“We started this journey in the year 2007 and this is the 10th Papertech; we have come a long way. We have learnt from each other and implemented many good practices in our mills. We have adopted a variety of methods to induce this learning and sharing including missions, training programs and focused workshops. We organized international visits involving international agencies like SIDA, SEA and UNIDO; conducted many webinars, etc. Papertech has become an excellent example for ‘Learning through Sharing.”
Speaking on activities taken up in the year 2015, he said, “The activities facilitated learning through sharing among paper mills. We did advisory services like mandatory energy audits, PAT M&V studies along with life cycle assessment in paper mills. Then, a group comprising members of CII and UNDP was formed for GHG inventori-zation. They did an excellent job on carbon footprints and GHG emissions. Also, from all our features, we have implemented many good practices in mills. In fact, we have issued nine e-manuals which are available on the website in pdf forms for future references. In the last two years, we have also conducted many webinars and there have been a significant improvement in attendees of such webinars. It has now become easy to learn while sitting in the office itself and discussing these issues with other company’s experts. Webinars are an excellent example of learning and are becoming popular day by day.
“Then, there was Cleantech Innovation Programme with the involvement of SEA. The main objective of Cleantech Innovation Program was to facilitate ‘innovation acceleration’ in clean tech areas through partnership between Indian and Swedish companies. With the installation of Swedish technologies Indian mills came to know that there is something of that level available in the market, increasing their exposure to new technology. Some of the technologies relevant to the paper industry are Opcon – Low temperature Thermal Rankine cycle for Power generation; FOV and ED Biogas – Biogas production from organic waste; Sensic – Sensors for the measurement of SOx and Nox; Clean Combustion – Multi fuel Burners for lime kilns; Metrum – Power quality management tools; PPAM Solkarft – Bifacial Solar Panels; etc.
“Moreover, in continuation of the Indo-Swedish Cleantech Innovation Programme, lots of webinars and on-site visits have been conducted by Swedish companies. Recently, the Swedish delegation visited India in May 2016 and organized workshops in Mumbai and Chennai. These companies also paid a visit to ITC, BILT, IP, SPBL and TNPL.”
Mr. Viswanathan also outlined the future tasks and said that formation of core group during Papertech is next on the list. “The main idea behind forming the core group is to share best practices. The members are from leading paper mills – ITC, JK, BILT, SPBL and other prominent paper advisors. The major objective of the group includes sharing of best practices adopted by best performing plants, development of low carbon roadmap for Indian pulp and paper sector, and facilitate cross sector learning – cement industry, thermal power plants, sugar mills etc.,” said Mr. Viswanathan.
“This year, we have invited Mr. K. N. Rao from ACC Limited as a representative of the cement industry to facilitate cross sector learning. We also have parallel power sector meetings going on and we will have more opportunities to interact with other sectors on 24th as part of Energy Efficiency Summit,” concluded Mr. Viswanathan.
Strategies for a Green Industry
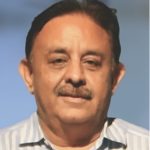
“We as an industry need to work together to make ourselves more saleable and environment-friendly because, as far as I think, paper industry is one of the most sustainable industries in long run.”
Mr. Sanjay Singh, Co-chairman, PaperTech 2016 & Divisional Chief Executive, ITC PSPD, briefed about the Strategies to Make Indian Pulp and Paper Industry Green. He said, “Since last few years, paper industry in India has been going through a rough patch. First of all, the image of the industry is nothing great as whenever you talk to someone they talk about paperless offices and things like digitization. In spite of all our efforts the image of paper industry continues to be a big myth.
“Second major concern is the growth of eucalyptus in India. Lot of activities has been taking place to improve the forest cover in the country which is a positive sign. Recently, railways and National Highway Authority of India are working on increasing the forest cover. But, when we ask govt. or authorities to plant eucalyptus, they deny saying it’s not good for environment; talk about some other species. Although many articles have been published about eucalyptus not being harmful to the environment, there is not much change in that mindset.”
Speaking on the need to improve the image of the paper industry and instill its right identity among masses, he said, “We as an industry need to work together to make ourselves more saleable and environment-friendly because, as far as I think, paper industry is one of the most sustainable industries in long run. If we continue to focus on our core strength, we will definitely succeed. Good things, new ideas and technologies discussed at IIPTA and Papertech have helped us cut down the energy consumption considerably. But, these measures are not as good as the measures followed by the cement industry. So, we have Mr. K. N. Rao of ACC ltd. with us to share some energy saving methods.
“The third most critical concern affecting the pulp and paper industry is water consumption. Last year, many units and various suppliers have suffered from the shortage of water. This year we were all anticipating that there will be excess or above average rainfall in our country, but I read yesterday in the newspaper that excess rainfall is again proved to be a wistful thinking. Most of the paper industries are dependent on ground water which is not a healthy sign. In addition, we need to find out ways to rejuvenate ground water, otherwise at some stage it will hit us hard. CII’s Triveni unit is working along with us to educate people about current situation.”
Speaking on the strategies to make the Indian paper industry green, Mr. Singh outlined the efficacy of GreenCo rating system. He said, “Now coming to the issue of making the industry green, well, lots of us are already working towards it. Let me discuss the GreenCo rating system with you. There are basically six areas on which GreenCo rating system works or audits. These areas include energy management, waste management, material conservation, green house gas (GHG) mitigation, green supply chain and product stewardship; all these areas will make us more competitive.
“Though the customer will not pay you anything extra for doing this, but will definitely give you more suppliers, less or zero duty; these things will certainly make you more competitive. We have worked on two units Bhadrachalam and Kovai and after a tough journey both of these units now have platinum rating which is the highest rating in the system. All I can say is that our efforts have given us phenomenal success. Besides being money saving, it brings the unit together; our experience has been wonderful. When you have to achieve the standards for a rating, the employer, contractor, manager and the whole staff come together to set the targets and plan strategies to achieve the desired. I would request all the industries to go through GreenCo rating system. It may take 1 or 2 years in fully applying or realizing the rating system, but in long run this is going to benefit the entire Indian paper industry.”
Way Forward to a Sustainable Future
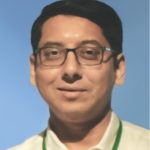
“My personal take on this is that whatever is green will be sustainable. Also, green means zero impact on environment.”
Speaking on the theme ‘Way Forward to Sustainable and Green Future for Indian Pulp and Paper Industry’, Mr. Pawan Agarwal, Managing Director, Naini Papers Limited, said, “I am representing a very small sector of the Indian paper industry, i.e. agro-based paper mills in northern part of the country. That region is known for its agro-based paper products including kraft, writing & printing paper and tissue. As per the topic, I will be talking more in context of agro-based industries which may or may not be applicable to the other sectors of the industry. Well, we have been hearing a lot about sustainability and perhaps this is the only thing we are going to hear in next 10 years. Also, this is the only thing that will make us survive in the next 20 to 30 years.
“My personal take on this is that whatever is green will be sustainable. Also, green means zero impact on environment. Today’s biggest sustainability criteria include assured supply of raw material on long-term basis. We have been discussing this on the past platforms – be it availability of wood, agricultural residue or even waste paper; so, assured supply is one of the basic aspects of sustainability. ITC has done a lot in terms of its program WOW. Another aspect in this scenario is continuous demand in growth of products. Why to produce and for whom to produce are the questions that will help us take care of continuous demand. Lastly, there should not be any adverse impact on environment and the ecology by any production activity.”
Explaining the tremendous pressure agro-based fiber is under, he said, “Availability of bagasse and wheat straw is reducing day by day. I still remember there was a time, when we started this venture around 17 or 18 years ago, the whole pie chart representing the distribution or paper production in whole country, it was 1/3rd each raw material, viz. wood, agro-based, and waste paper. However, today it has totally changed as agro-based raw material has come down to less than 15 percent and recycled fiber has gone up to 55 percent.
Mr. Agarwal also explained why the agro-based paper production has been hit badly, coming down to mere 15 percent of the total paper production in the country. “There are certain reasons which account to this situation, viz. scarcity and transportation bottlenecks. Scarcity is because sugar mills have installed power plants to supply power to the grid thereby consuming all the left-over bagasse. Also, farmers are using “combines” to harvest their wheat crop thereby eliminating the generation of wheat straw. Moreover, increased transportation cost due to high fuel cost and poor roads has made the transportation of wheat straw and bagasse impossible from distant places. It takes around two days to travel a stretch of 500 km as the roads are bad.”
Taking stock of the environmental issues faced by agro-based paper mills, Mr. Agarwal said, “Among few challenges are high consumption of fresh water; improper cleaning of raw material resulting in high chemical consumption in bleaching stages, thus generating an effluent having high COD & BOD load; high consumption of bleaching chemicals due to lack of good cooking and absence of new technologies like ODL, ECF, etc; poor runnability of paper machine lead to high generation of effluent with high TSS loads; and many more such issues.
“We have known many mills since last few years consuming as high as 150 cm per tonne of paper. At a time, we used to have a paper break after every 20 minutes which means 72 breaks a day, indicating the poor efficiency of machine. In addition, we need to consider effluent treatment process at the end of each process rather than considering it as an end-of-the-pipe-solution. Under-designing of ETP’s was also a problem in most of the cases including ours. Lastly, the lack of trained manpower to operate the ETPs and run the environment lab also contributed to the increasing environmental issues.”
Mr. Agarwal spoke about the impact of Ganga River Basin Authority’s norms in addressing some of the environmental issues. “In 2012, we adopted the charter and this was a landmark year for paper industries in that region as we adopted the principle of benchmarking. We borrowed best available technologies available in the country in all the process and at every step. That was a period when all of us were facing challenges like closure of mills or notices for closure of mills. If you take care of environment, you have to take care of energy as well and for this we included some green technology in pulping,” he said. “We adopted wet washing of pulp and it was documented in the charter that every agro-based mill will have a pulp washing plant. Wet washing of raw material improves yield and reduces bleach chemical consumption. This further improves the performance of recovery plant leading to improved quality of pulp.”
Mr. Agarwal further mentioned the steps to reduce the environmental footprint of the mill as per the charter norms. He said, “The use of continuous digester for cooking for improving the yield and quality of pulp, installation of twin roll press or DD washer for brown stock washing o avoid the wastage of water, installation of chemical recovery plant, Oxygen Delignification – a truly green technology as it reduces kappa number of the pulp by 30 to 35%, elemental chlorine free bleaching, etc. were some of the steps taken by us to meet the charter norms and the results have been inspiring.
“Nowadays, few mills are adopting green bleaching and we are going way ahead. We are working in association with CPPRI and paper research Institute to add ozone stage in one of the stages with per-oxide bleaching which will help in closing of back water circuit in bleach plant. This will tremendously cut down the pollution load on ETP plant. The effluent will have very low COD and BOD load.
If a paper machine is less efficient, or has poor runnability, or it is consuming high energy and high steam, it is also a major issue with the paper mill, said Mr. Agarwal. “So, we concentrated on paper machines as well and what we formulated is that today’s sustainable paper machine comes with features such as minimum fresh water consumption in fabric cleaning, maximum dryness out of the press section, the best evaporation rate in the dryer section (1.4 Ton or more evaporation of water per Ton of steam), and minimum breakages on the machine (maximum close draws),” he added.
“We at Naini Paper Mills have got a machine which was designed for 125 mpm; but last week, it was running at 635 mpm and now we are planning to take it to 650 mpm. Earlier, it had 30 breaks a day, but now it has 2 to 3 breaks a day. So, we are looking to achieve such runnability in future machines,” said Mr. Agarwal. “The machine drives, vacuum systems and other machine auxiliaries should have minimum energy consumption. Machine should have a highly efficient dryer hood and air ventilation system. It should have minimum quality variations with online QCS along with the optimization of finishing losses.”
“I can only say that we have to have this holistic approach, indulge in conservation of resources like fiber, water and energy, use green technology in pulping and bleaching and maximum automation for better quality & process control. We have installed automation in our ETP also. We should try for maximum possible recycling of waste generated at various stages. Thereafter, the effective treatment of effluent will further minimize the impact on environment. Even waste treatment can give opportunities for making profit,” he added.
At the end, Mr. Agarwal cited a short story where a man had to take a chance or make a difficult choice for a result which was better and sustainable in long run. Through the parable, he exhorted the paper industry not to shy away from investing in good technology and sustainability, which will bear fruit in times to come.
Low Carbon Roadmap for the Pulp & Paper Sector
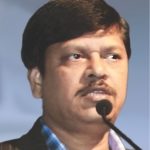
“Coming back to our relation with the pulp and paper, I will emphasize on the fact that you have lime sludge which is an alternative raw material for us. If instead of limestone we use sludge, then we won’t produce CO2.”
Mr. K. N. Rao, Director – Energy & Environment, ACC Ltd. gave a complete idea of what the cement industry is doing on sustainability and resource conservation front. He started his address with giving a brief about the cement industry in the world and cement industry in India. “Cement industry in the world produces around 5 billion tonne of cement annually out of which 50 percent is produced in China that is around 2.5 billion tonne. India has around 350 million tonne of installed capacity, actually producing around 260 million tonne. We see that China and India are similar in terms of country-wise size and population, but our per capita consumption is 1/8th of China when I try to compare other products like per capita paper consumption, steel consumption or power consumption. These are the key indicators of country’s economy and overall progress. Here I can say that paper industry and cement industry are on the same boat as when per capita consumption is compared to the benchmarks we are far behind,” said Mr. Rao
He added, “Ultimately, we need to do everything in a bit different way than how it is done in the rest of the world as we have very little land and little amount of water with respect to the percentage of population. So, this is a kind of trigger for cement industry to think about how to grow to 2.5 billion tonne by 2050 within limited resources. Also, we need to implement sustainable practices.”
Citing few of the challenges that the cement industry faces, he said, “Similar to the raw material required by pulp and paper industry, our limestone resources are very limited. As per what I have understood from previous presentations is that you have already learned and are using sustainable alternatives like 55 percent of your raw material is coming from recycled paper. But, as far as we are concerned, to make cement, we take limestone from mother earth and convert that into cement. So, anything that comes from natural resources is limited and will exhaust soon.
“Also, as per the current consumption of limestone in the country, our prediction is that most probably by 2030 or 2040, the nation will not have limestone and India might have to import limestone like petrol and oil. The mineable limestone might be available deep below the forest. Some of it might be below sea and some under the mountains, but those cannot be mined out. In this situation, raw material security is a big challenge.
“And another dimension is even if you get the limestone, CO2 emission is a challenge. In the cement manufacturing when we do the calcination of limestone, we are actually releasing CO2 as calcium carbonate decomposes to calcium oxide and ultimately CO2 gas comes out, leaving silicates behind as calcium silicate, which is basically the cement. So, you can make out very clearly that your future is not secure and limestone reserves are very limited. But, when a country needs to grow, it would need infrastructure. Keeping this in mind, we have to come up with low carbon roadmaps and I will now talk about what cement industry has thought about it and what are our challenges.
“The moment you talk about mining you have challenges like biodiversity and deforestation, which are also the common challenges for every industry. Besides, CO2 emission due to the combustion of high carbon fuels combined with the production of CO2 from the process is yet another dimension. We are also very high energy-intensive in terms of fuel and electricity. Earlier manufacturing cement was a wet process, so looking at the fuel and water intensiveness, the industry needed to relook whole thing in totally different way. We had to find out different ways of manufacturing, we needed to do process innovation including product innovation.
“Unlike the paper industry, the cement industry does not face any threat from import and raw material cost fluctuations. In that way, we are secure that cement is something that cannot be transported over long distances and thus eliminating the import threat. The paper industry however is facing more challenges than cement industry in terms of inputs and raw material costs. When you try to look into the whole issue to become countable nationally and internationally, you need to reduce the manufacturing cost along with that you need to bring down the fuel cost, raw material cost and lastly handling cost. Also, we need to bring down CO2 footprints with that to become sustainable.
“So, keeping all these in mind, we in the cement industry were trying to see what can be done as an industry together. So, this is a 350 million tonne capacity industry and these are the numbers from the leading companies, which are the members of cement industry sustainability drive. We tried to find out how to develop a low-carbon roadmap for the Indian cement industry, not only for individual company, but for all the companies in India. We formulated technical papers to support the roadmap with the help of many reputed associations including Indian Financial Association and International Energy Agency. The roadmap attempted to identify the key levers, technologies, necessary policy and financial support. The roadmap envisioned the emission reduction from 0.712 t CO2 / tonne of cement in 2010 to 0.35 t CO2 / tonne of cement in 2050 under 2 degree scenario.
“We have developed approximately 28 technology papers. These papers are not only for how to improve the current assets, but also on how to build future assets and technologies and what are the products we need to develop in future by using the natural resource intensity. Keeping this process side innovation and product side innovation, we could ultimately come out with few levers which helped us to come out with our alignment in terms of how we can reach the 0.35 tonne.
“For paper industry, I would like to say if you want to do benchmarking, firstly study the benchmarking done across the world. Also, measure your footprints before making benchmarks like we did benchmarking after knowing where we are currently and what the total production is. And, we found out that our cement installed capacity is 238 million tonne; total cement produced is 217 million tonne; the clinker to cement ratio- is 0.74; electricity intensity/ tonne of cement is 80 KwH; thermal intensity/ kg of clinker- is 725 Kcal; alternative fuels used (as a share of thermal energy consumption) is 0.60 percent; and the current CO2 emission is 0.712 t/t of cement.
“We made the questionnaire and sent it to all the companies through CII so we could measure the footprints and do the benchmarking. Then, we tried to find out gap that we had and ultimately work to remove it. Furthermore, we did a prediction on the population growth and GDP growth that what numbers is India going to hit. So the prediction was that in 2050, India may have a situation of 1.36 billion tonne of cement against a 350 million tonne of cement where consumption is hardly 230 or 260.”
Through a table, Mr. Rao tried to explain the set targets for the cement industry to be achieved by 2050, including some intermediate targets. He said, “This table will give an idea that cement production will go from 217 to 1361, per capita consumption will go from 188 to 812 kg, clinker-to-cement ratio will go from 0.74 to 0.58 (amount of clinker in per tonne of cement) and then electric intensity goes from 80 to 70 kWh/t cement, thermal intensity of clinker production goes from 725 to 678 kcal/kg cement. Finally, if we use alternative fuel the share of thermal energy consumption goes from 0.6 percent to 25 percent by 2050. These are our set targets and we have kept some intermediate targets for 2030 and 2040 too.”
Mr. Rao also sounded pleased at what the cement industry has achieved in terms of the targets it has set for itself. “Whatever were the global targets for cement industry, India has already achieved it they were the base line for India but now situation has changed. The only place we are lagging is the use of alternative fuel. Thermal and electrical energy in Indian cement industry is the best in the world; also we found that India is already best in terms of energy efficiency and energy performance. We are just not good in using waste material for fuel in the kiln; that is one area where we found the gap and trying to cope up with it,” he said.
He added, “With the assistance from finance ministry regarding financial barriers and environment ministry regarding rules and regulations, we have been able to achieve our set targets for 2015; we have also over-achieved some of the targets as compared to the base line of 2010 benchmark. In total, the benefit of this is that every company is ready to bring down their manufacturing costs, reduce their energy consumptions and also the fuel consumption. We have a fuel security with our raw material security which can together help our industry to improve.”
Explaining the similarities in the challenges faced by both the industries, he sought collaboration between the paper and cement industries to mitigate these challenges. He said, “Coming back to our relation with the pulp and paper, I will emphasize on the fact that you have lime sludge which is an alternative raw material for us. If instead of limestone we use sludge, then we won’t produce CO2 and also I don’t need to mine limestone. This is one of the areas where we can work collaboratively and this is the reason why groups like Emami, Orient, and Century have the cement business along with the paper business.
“Another area is cement kilns which we operate at very high temperature, i.e. around 1400 degree Celsius. If you are able to use these thermal transforms in the kiln and fire a liquid waste through the burner into the burning zone, we drop the temperature by huge extent bringing down the value of NOx. Currently, the Govt. of India has stated the norms related to reduction of NOx; so working collaboratively will help in reduction of NOx levels.
“Also, today I can say that paper industry has become carbon-free industry and this is something cement industry can never dream of. We were only thinking to bring down 700 to 350 but the amount of social forestry which you are doing, amount of recycled paper you are using; there is a chance for you to become carbon positive in terms that you are able to use the energy and then offset the energy by doing plantations and tomorrow people should not say paperless office as more paper means more greenery, more plantations and more aforestation.”
Carbon Constrained Economy, the Future
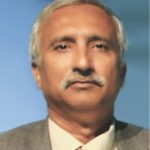
There is a huge possibility in pursuing low carbon roadmap for the pulp and paper industry. Excellent work has been done in the cement industry and similar thought process can be applied to the pulp and paper industry
“Raw material sustainability continues to be the fundamental priority for pulp and paper industry and another wonderful effort done in the state of Telangana includes Haritha Haram Scheme launched by Telangana government on July 11,” said Mr. S. Raghupathy, Deputy Director General, CII – Sohrabji Godrej Green Business Centre. “It is a massive plantation scheme across the state whose focus was to have 25 lakh plantations in Hyderabad only. Mr. Sanjay Singh along with ITC planted 8.5 lakh plantations in one day and this represents our industry’s involvement with the government. As a partnership plan, the state in total has achieved a target of 35 lakh plantation. So if all of us can plant together, I think tremendous achievements are possible.”
He further said, “There is a huge possibility in pursuing low carbon roadmap for the pulp and paper industry. Excellent work has been done in the cement industry and similar thought process can be applied to the pulp and paper industry. You decide for yourself and as the Europeans say carbon constrained economy is what we should focus on as carbon content emitted will determine your production levels.”
“GreenCo is doing extremely well on international levels as today we are a group of 200 companies working in this direction and enormous benefits have been shared by GreenCo companies. Also, we have achieved 54 crore of saving with very negligible investment. Last but not the least, this point can have future impact on how green is the Industry 4.0 which is being talked all over Europe, US as well as India also. Manufacturing 4.0 and Industry 4.0 works on the concept of cyberisation of entire thing and how internet of things (IoT) can integrate individual missions to achieve the best performance.”
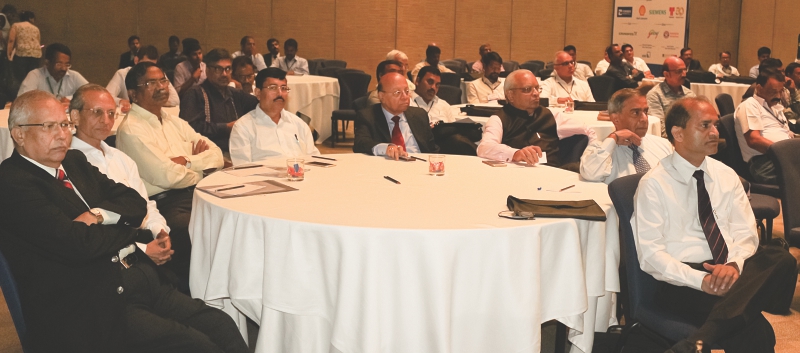