////////////////////////////////////////////////////////////////////////////////////////////////////////////////////////////////////////////////////// Mr. R. Knop & Mr. D. Schepers*
In present scenario rod metering systems are the preferred metering systems in the paper and cardboard industry for the use:
– in film presses for surface sizing, pigment coating and coating
– in conventional applicator systems for pre-coating and back side coating of cardboard
In comparison to other metering systems e.g. blade coating – rod metering is characterized by a low susceptibility to failure and longer lifetime. Due to that rod metering systems are also especially suited for metering in online systems.
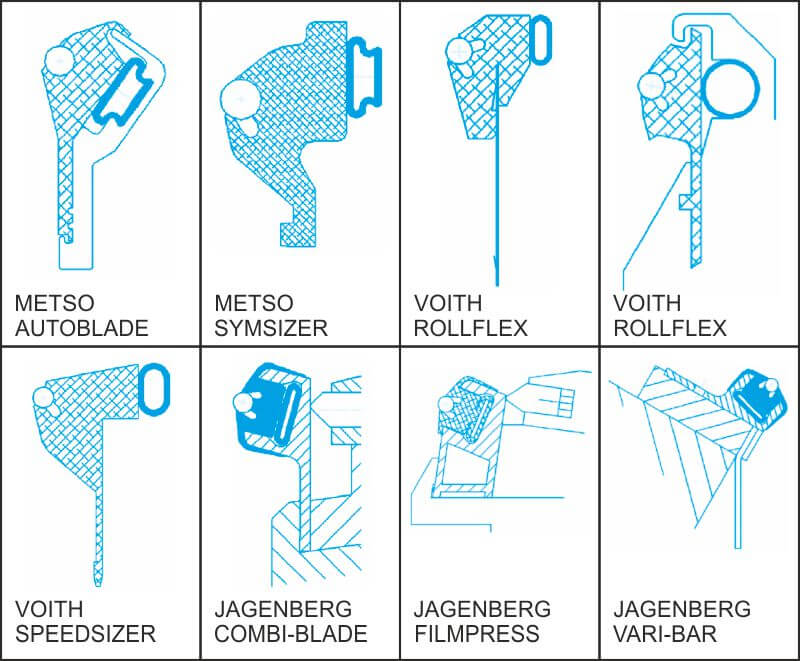
Figure 1 illustrates the design and the characteristics of conventional rod metering systems in applicator equipment of different manufacturers.
Surface sizing in a film-press
In case of surface sizing of paper or cardboard the profiled, chrome coated metering system is a better technology. For this application the smooth design of the metering rod is less suited due to the low viscosity of starch. Even at high operating speeds and large diameters the generated hydrodynamic pressure is not sufficient to guarantee a trouble-free metering.
With an optimized design of the metering system regarding diameter and profile a lifetime of approx. three to four weeks is attained in practice. Yet it is advantageous that starch is generally not classified as an abrasive medium.
In view of stated lifetime and trouble-free operation with profiled, chrome coated metering rods the metering of starch can be principally called an economical process.
An attainable improvement concerning the lifetime by using a ceramic-coated metering rod has not been proven in each case. In practice the advantage of an increased lifetime can be ruined due to damages of the metering system as a consequence of an operation failure (break, drive system) and/ or wrong treatment of the metering rod.
Despite the advantages of the profiled design in case of surface sizing volumetric metering have also its limits. A large alteration to the coat weight e.g. in case of changed paper quality is only achievable with a change of the profile meaning an exchange of the metering rod. The range of coat weight adjustable by the pressure is maximum 20% and is usually required for the compensation of the wear.
Pigment coating and coating in a film-press
In comparison to surface sizing the recommendation of an optimum metering system for pigment coating and coating is not as clear. Beside the suitability of the design with regard to the process the lifetime is the decisive criterion.
Using a profiled, chrome coated metering rod for the application pigment coating and coating a lifetime of maximum ten days is attained under optimum condition. Though in case of high abrasive pigments e.g. titanium dioxide the lifetime can be reduced to only a few hours.
The profiled, ceramic-coated design is a possible alternative, if the process can’t be done without volumetric metering due to technological reasons. In some productions an increase of lifetime from approx. 12 hours to approx. 5-7 days was attained changing the wear coat from chrome to ceramic.
An additional, if not preferred option for the application pigment coating and coating is the use of smooth metering rods with a large diameter in the range 20-38mm. In particular at high operating speeds and high solid contents the smooth design of a metering system is accepted. For this application lifetime of smooth, chrome coated metering rods is approx. two weeks and of smooth, ceramic coated metering rods approx. four weeks.
Though contrary to the volumetric metering using the smooth variant of a metering rod each disturbance concerning the hydro-dynamic is resulting in deviations with respect to the coat weight. The cause of the disturbances can be both fluctuations in the coat supply e.g. solid content, viscosity etc. as well as geometric deviations e.g. tolerances of the press roll, metering system etc.
Pre-coating and backside coating of cardboard
Although numerous coating stations for blade coating have been installed in the field of pre-coating and backside coating of cardboard in the course of the last years, the smooth metering rod is still the recommended system. The essential advantages of a metering rod in comparison to a blade, which are also resulting in an excellent suitability for online-systems, are as follows:
• Long lifetime
• Constant quality over running period
• Indifference with respect to streaks
A few coating systems are also operated with the profiled design of the metering system. The volumetric metering result in an even coat distribution referring to the thickness, which is similar to the contour coat of an air knife.
Though in this case special requirements with regard to the usable recipes of the coat have to be considered. Furthermore an economic operation (lifetime) is generally only possible with a wear coat in form of ceramic.
An additional development in the application field of pre-coating and backside coating of cardboard is the use of smooth metering rods with a large diameter. After standard diameter has been in the range of 10-12mm for decades, due to the objective of higher coat weights an increasing number of systems with a diameter up to 25mm are in use. Yet the knowledge made at pigment coating and coating in a film-press are just transferred.
Developments and prospects of rod metering
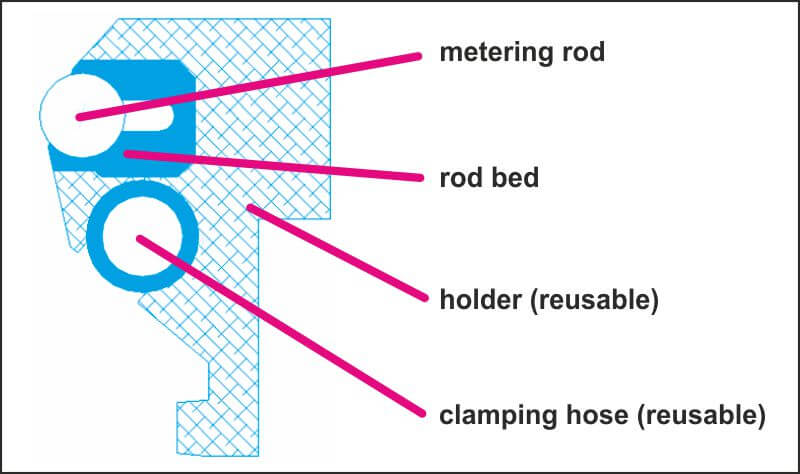
Beside the fundamental technological suitability for various applications the economy of a metering system is of decisive significance.
Against this background the increase in the lifetime and the reduction of costs of the system are a basic objective. According our experience in a lot of productions the potential is yet not completely exploited.
In the course of the last years optimizations referring metering system e.g. design, wear coat, diameter etc. resulted in a significantly increase of the lifetime. A further cost reduction was achieved by a decreased price level for metering rods due to optimized manufacturing methods and production conditions at the suppliers.
An innovation in the field of rod beds is the COMBI-System according fig. 2, which is applied for an international patent.
The COMBI-System is a compatible replacement of conventional rod beds. The modification of the holder system to the COMBI-System doesn’t require any alteration with respect to the coating equipment. The metering point and the setup of the coater station are kept unchanged.
The characteristics of the COMBI-System are changeable, small rod bed (seat of metering rod), which is the actual wear part, and a reusable holder with a clamping hose. The COMBI-System unites major advantages concerning costs and handling. In comparison to conventional rod beds the COMBI-System is combined with a cost reduction of about 50% due to the material saving design of the wear part. The defined guidance of the metering rod and the adjustable sealing between rod bed and metering rod by the clamping hose results in a trouble-free operation. The reduction of setup times as a consequence of the simplest replacement of the wear part are leading to another indirect positive effect on the economy of the system.
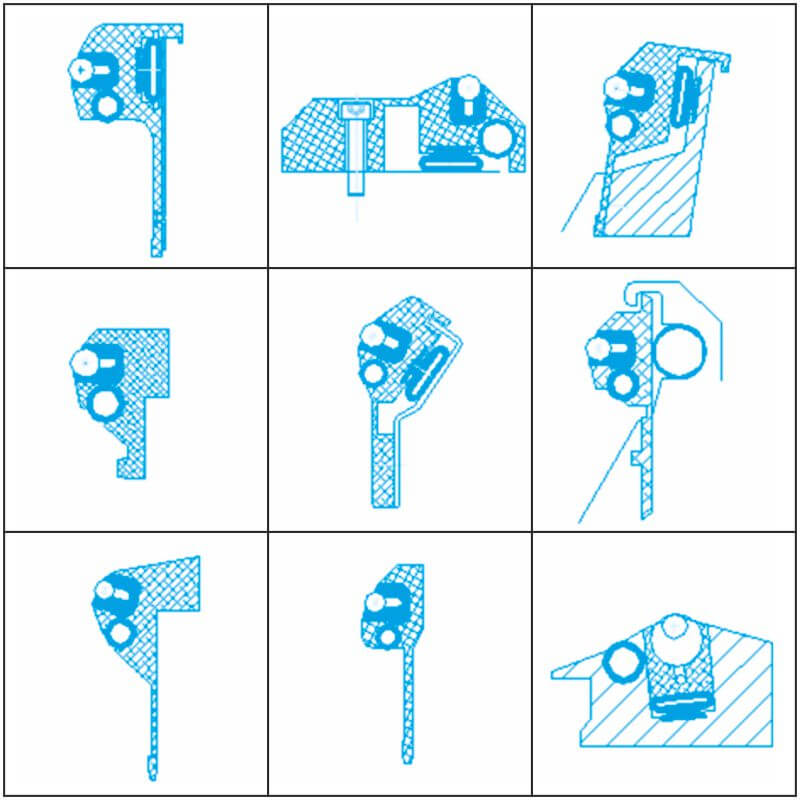
An overview about the different coating stations of various equipment manufacturers, in which the COMBI-System has yet been repeatedly proved and successfully employed, describes fig. 3. The development and introduction of the COMBI-System for other designs of coating stations is going to be effected in the course of the next months.
———————————————————————————————————————* HORST SPRENGER GmbH