“With this cutting-edge Greenfield project, we are now the world’s fastest-growing aseptic liquid packaging company, with a year-on-year growth rate of more than 100 percent.”
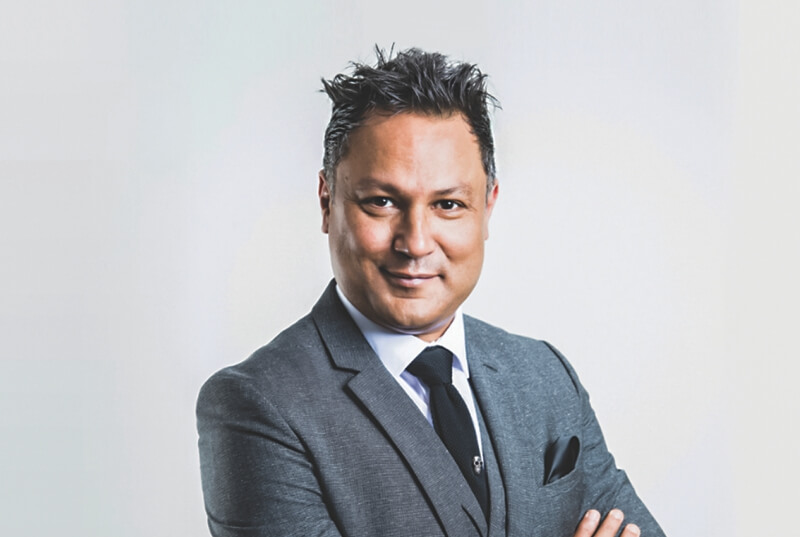
Asepto—from the house of Uflex Ltd.—is India’s first aseptic liquid packaging material with a state-of-the-art manufacturing plant in the industrial hub of Sanand in Gujarat. In a conversation with Paper Mart, Mr. Ashwani Kumar Sharma, President & CEO, Aseptic Liquid Packaging Business, UFlex Ltd. presents an overview of the brand, views on the aseptic packaging market, and the procurement of the paper used in this packaging. Further, he talks about the current size of the aseptic paper-based packaging market segment and their future roadmap.
Paper Mart: To begin with, we would like you to present an overview of Asepto – the first-of-its-kind liquid packaging brand in India and the market reach and growth the brand has attained so far? Also, how do you plan with regard to increasing your reach in the domestic and international market?
Ashwani Sharma: We identified the latent need to rejuvenate aseptic packaging which could give a new benchmark to achieve for companies using aseptic packaging. UFlex – India’s largest flexible packaging materials & solutions company is the first Indian company to enter into the aseptic liquid packaging sector under the brand Asepto, with an investment of INR 1500 crore in a phased manner. When we began our operational journey in Q2’17, the market was dominated by one global company with over 90 percent market share and a few Chinese players. Asepto’s entry transformed the market’s scope because it presented dynamic solutions that the market had never seen before.
With this cutting-edge Greenfield project, we are now the world’s fastest-growing aseptic liquid packaging company, with a year-on-year growth rate of more than 100 percent. We are proud to have captured around 20 percent of the domestic market share in less than four years, resulting in our existing full capacity utilization. In fact, we have already announced in January this year that we are doubling the aseptic plant’s production capacity from 3.5 billion to 7.0 billion packs annually. This will help us to continue to develop new customers around the world and meet their needs. We currently serve over 100 customers both in India and internationally. Our aseptic packaging material is being exported to many regions like Southeast Asia, Africa, Europe, and many more. The who’s who of the dairy, fruit beverage, and liquor industries are amongst our clients.
Innovation has always been our strong forte and the foundation stone on which Asepto is built. With a deep understanding of polymer science as well as printing and packaging expertise, we have contributed value in a variety of ways, resulting in Asepto becoming a frontrunner among businesses for their differentiated packaging needs. We are making the most of our in-house holographic and engineering prowess to stir up the monotony that has been set in the retail shelves of aseptic packs globally. Asepto introduced never-before-seen aesthetic features like foil stamping, holography, and 3D lens, elevating the face of aseptic liquid packs for the first time ever.
By being the first to provide these value-added features in aseptic packaging, we were able to carve out a strong market niche for ourselves. This breakthrough was used by our valued clients to not only identify themselves and stand out on crowded retail shelves but also to emphasize the safety characteristics of the aseptic packaging, such as duplication proof. Even throughout this pandemic, our never-ending focus on providing high-quality packaging solutions and doing-it-right-the-first-time has allowed us to establish ourselves as a strong player worldwide.
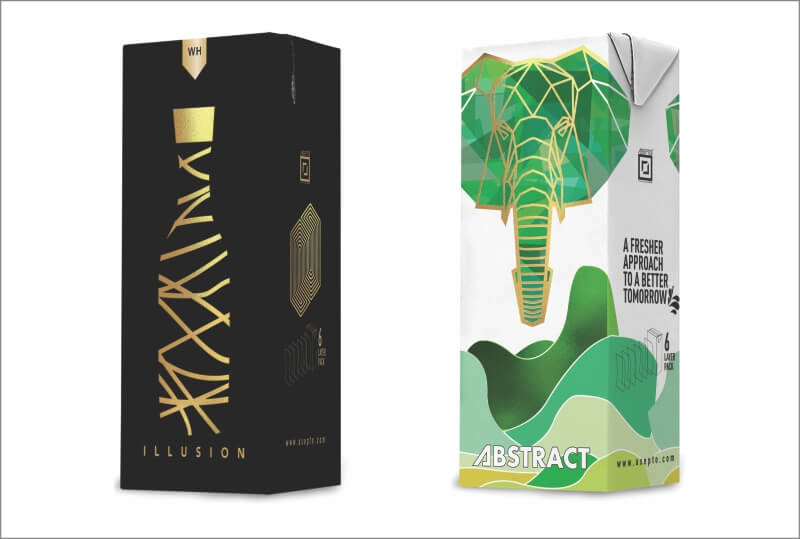
PM: What are your views on aseptic packaging, in particular the liquid packaging industry in India and how do you envision the further growth of the industry? Please describe the key trends and the growth-drivers of the industry.
AS: The Indian market for aseptic liquid packaging is currently around 12-13 billion packs annually, and it is increasing at a CAGR of 12-15 percent per year. The industry is being propelled forward by rising demand for food products with a long shelf life, no preservatives, and packaged in a safe and hygienic manner.
Businesses are progressively employing sustainable and efficient packaging solutions and production processes that appeal to consumers of all demographics. We’ve witnessed major changes in end-user purchase patterns, especially during this pandemic period, as they switch from loose to packaged products and choose better and safer eating and drinking options.
In my opinion, few key trends that will shape the industry dynamics in the near future are:
Packaging preference that is both safe and hygienic: Consumers are increasingly becoming more mindful of using a quality packaged product. They are aware and making judicious choices in favor of products, which are available in packaging that guarantees quality, safety and hygiene. Tamper-proof packaging has developed itself as a vital differentiating factor that resonates strongly with consumers’ changing buying preferences.
Consumers’ desire for nutritive value propositions: Thoughtful choices that go with the lifestyle, yet are good on palate and health have become the preferred consumer choice. A lot of emphasis is on packaging and processes that are closer to nature and offer natural benefits of the product inside. Thus, new-age aseptic packaging significantly helps brands offer their products at the optimum nutritional value, keeping the convenience factor in line with their needs.
Care for Environment: People are increasingly becoming aware of their responsibility towards preserving the immediate surrounding and environment. In that light, they are consuming smartly and the buying patterns have also been impacted. They are keen to know about packaging, its impact on the environment, and so on. Being critical of our carbon footprint is not only a practice for businesses; it is also becoming a thought for individuals. Therefore, packaging using safe and sustainable materials for production directly relates to the end consumers’ mindsets.
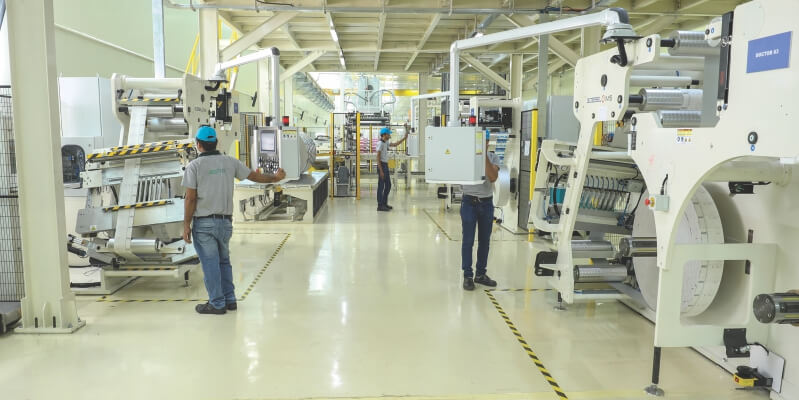
As we see it, there will be enormous growth opportunities in the beverage business, particularly in aseptic packaging, such as:
Dairy Category: We are the world’s largest milk producer, with milk output of around 200 million tonnes (MT) in FY21, However, when we look at the dairy category’s share in aseptic packaging, it’s abysmally low. Aseptic processing (UHT) and packaging for white milk and milk products such as ghee, buttermilk, lassi, drinking yoghurt, milkshakes, and flavoured milk among others, have enormous potential not just in the native market, but also in countries with a sizeable Indian diaspora. Without the use of preservatives, aseptic processing and packaging provide significant benefits in terms of extended shelf life and preserving the product freshness which is paramount for a perishable product like milk. For a period of 6-9 months, the milk or milk product remains as good as fresh and free from any contamination.
Alcoholic Beverages: This category has already begun to make a big positive impression not just on the business but also in the minds of consumers; based only on the fact that the product in aseptic packaging cannot be duplicated and is tamper-evident. End-users are becoming more aware of the advantages of aseptic packs over glass/PET bottles, which will undoubtedly have a spilling effect on other categories too.
New Categories: Many new categories in the fruit beverage market have emerged, including energy drinks, ready-to-drink ORS, and plant-based beverages, to name a few. They’ve carved out a niche for themselves across the country, and are making significant contributions to the growth of the aseptic liquid packaging business. Another prospective category to watch is aseptically processed and packaged mineral water. This category is currently awaiting approval from the concerned regulatory bodies. The best mineral water companies in India are focusing on augmenting their market shares by implementing effective marketing strategies and attractive packaging. According to a report by Market Research, the market reached INR 160 billion in 2018 and it is expected to grow annually by a CAGR of 20.75 percent and reach INR 403.06 billion by 2023.
PM: The aseptic cartons are made of materials that together result in a very cohesive, efficient, safe and light-weight package – what is your approach with regard to producing a packaging material with optimal properties and excellent performance characteristics?
AS: Convenience, safety, quality, and ease of use are all important features of effective aseptic packaging. All our raw materials are sourced only from top-of-the-line manufacturers that are known for their quality and reliability worldwide. Our cartons are made of high-quality paperboards sourced from industry-leading Scandinavian manufacturers which guarantee consistency in terms of quality. The long-fiber paperboard used in the Asepto package provides strong bonding, high tear resistance, and bursting strength. As a sealing layer, only the highest quality PE/mPE is used since it offers a strong bond between the paper and the other layers of the packaging material. Aluminum foil – functions as a strong light and oxygen barrier, eliminating the need for refrigeration and preventing spoilage of the product inside without the need for preservatives. The metal (aluminium) is also used as an induction sealing agent in the aseptic filling machines.
This multi-layer structure necessitates a robust printing, extrusion, slitting, and doctoring process, which is possible in our highly automated, state-of-the-art manufacturing facility in Sanand, Gujarat. Inline defect detection systems are placed on all of our machines, and they are capable of detecting and labelling even the tiniest deviation from the standard specifications. All of this automation ensures that the packaging material we provide to our valued customers is not only of the highest quality but also that this best quality material is delivered consistently.
The standardization of the entire process ensures smooth runability in the customer’s aseptic filling lines irrespective of its model and speed. Our aseptic packaging material is 100 percent compatible with all roll-fed aseptic filling machines.
PM: What is the ratio percentage of the ‘paper’ used in the aseptic packaging unit? Also, please talk about the quality of the paper used in aseptic packaging and the procurement of the same at Asepto – whether it is from the domestic paper mills or is it imported.
AS: The majority of our packaging is made up of paper i.e., paperboard makes for 75 percent of an Asepto pack, while the remaining comprises aluminum (6%), and PE /mpe.
Asepto package is light, portable, and recyclable as a result of its construction. The high-efficiency paperboard provides the required solidity and strength to the packs, as well as a good surface for clear design printing. We source our paperboard from renowned Scandinavian manufacturers. These multinational organizations provide the paper that complies with all international regulations, including Forest Stewardship Council (FSC) certification (chain of custody) and strict global manufacturing processes.
PM: Since packaging functionality has to be balanced with the cost and sustainability aspects emphasizing the need for a holistic approach; what is your viewpoint on developing innovative and sustainable packaging in order to enhance competitiveness in the industry?
AS: UFlex follows the philosophy of achieving operational excellence while being socio-environmentally responsible. We take great pride in being a world-class player in our industry segment in terms of technology, innovation, product development, and sustainability. As an organization, we are motivated to operate and contribute to society in an environment-friendly manner. Therefore, we strongly believe that all packaging solutions must meet the standards of recycling and circularity.
Keeping that agenda as the core of our operations, our aseptic liquid packs are made up of 100 percent renewable and recyclable paperboard (FSC certified) that can be recycled to help make the world a better place. With the motto of ‘RECYCLE, REGENERATE, and REVIVE’, we are constantly striving to make sustainable efforts.
We strongly believe that zero waste – in production, consumption, and reuse without discarding anything – is a moral, cost-productive, and visionary approach that all manufacturers can employ. Furthermore, while outright zero waste may not be conceivable, but with the help of our zero waste controlling standards and the methodologies, we execute to get ourselves closer to a genuinely zero-waste process. It is only possible when the entire value chain of packaging waste is collected, sorted, and recycled on a large scale.
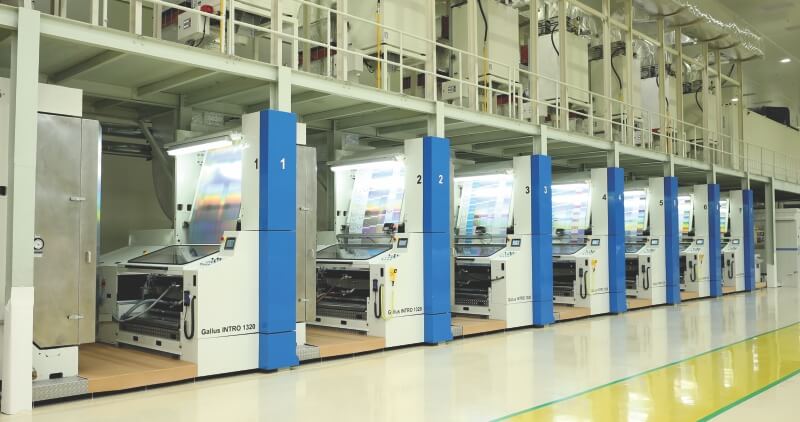
To achieve our waste management goals, we are associated with organizations that are collecting Post-Industrial Wastes (PIW) for recycling and transforming them into utility products.
We are currently using the Compression Moulding technology to recycle all our PIW and the Post-Consumer Waste (PCW) which are made available to us. This technology recycles all the waste into products used in domestic as well as industrial applications. Garden benches, doors, pallets, panel boards, and 10s of 1000s of a variety of other useful items are produced from waste, allowing us to remain in circularity.
UFlex is also working on a technology of upcycling the paperboard component of the post-consumer Aseptic waste. The process employs an Enzymatic De-lam Technology to separate the paper portion and convert it into paper-pulp. This upcycling technology is not only unique but an example of sustainability in the real sense.
The pre-consumption and post-consumption wastes need a robust waste collection system to increase the recyclability process. Furthermore, in India, the Municipal Corporation’s ongoing agenda recommends that citizens separate their household waste into a dry waste bin (for dry recyclable waste such as paper, carton packages, plastic bottles, and so on) and a wet waste bin (for food waste) so that the recyclable waste can be successfully recovered in a clean/dry state by waste-pickers and sent to the appropriate recycling stream. These initiatives and attempts will certainly ease the entire process for a sustainable solution contributing to a circular economy.
Our responsible actions today will help us in preserving and protecting our resources for ourselves, and for future generations.
PM: What is the current size of the aseptic paper-based packaging market segment in the country? Also, please outline the present consumption of paper as a material in the market segment.
AS: As previously stated, the Indian market for aseptic liquid packaging is currently around 12–13 billion packs per year and rising at a CAGR of 12-15 percent per year. According to many research sources, this industry is likely to double in size in the next 4 to 5 years, to roughly 25 billion, as several new categories and new players contribute to its growth story.
The beverage segment (which includes juices, nectars, still drinks, and other fruit-based beverages) accounts for almost 50 percent of the current market size. The liquor segment (which includes IMFL like whisky, rum, and country liquor) is the second-largest, accounting for around 35 percent of the domestic market. The dairy segment contributes to the remaining 15 percent (which includes products like white milk, buttermilk, lassi, flavored milk amongst others). The existing aseptic packaging material industry consumes approximately over 100,000 metric tonnes annually.
PM: Since the usage of paper-based materials as the go-to substrate in packaging is gradually increasing; what are the different opportunities in terms of co-designing additives that are easy to separate from paper, in order to reduce fiber losses during recycling?
AS: Today, various advancements are being made to improve the quality of paperboard, which eliminates the need for co-designing additives like PE and aluminium, reducing the difficulties of recycling paper and fiber loss. High barrier paperboard is available, with strong qualities such as barrier, sealing, and product integrity protection.
There are paper companies which have come up with breakthrough technology and developed high barrier paper that doesn’t need PE coating as the barrier layer or sealing layer. Such products do exist in the market as we speak and these products can directly go for recycling without any problems of separating polymer (PE coating) and paper. Therefore, paper cups (for coffee, teas, colas, etc) can be made out of such barrier cupstock paper.
In fact, we believe that in the future, high barrier paperboards with strong sealing and protective capabilities will be able to be employed as a single component perhaps in aseptic packaging as well. However, there will be a technical transition in both the sides of manufacturing from paperboard suppliers and on the existing filling technology to implement this single component paperboard modification.
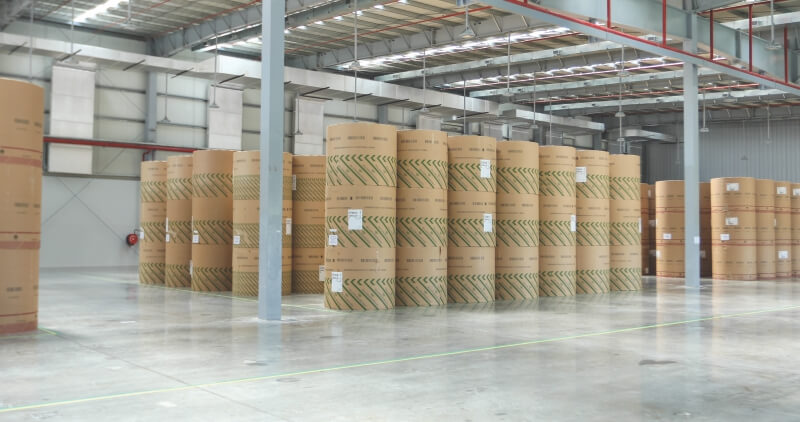
PM: Going ahead, what are the future plans of the Company in terms of product development and further augmentation of manufacturing capabilities?
AS: Asepto was conceived as a brand that would consistently innovate. Asepto introduced first-of-its-kind next-generation technologies of holography, foil stamping, and 3D lens for the global market. These technologies, which used captivating effects to attract attention, enabled brands in carving out a position for themselves on crowded retail shelves by displaying differentiation. It offered them a fresh identity. As a result, the market can anticipate and experience several of the new developments that are in the making and will provide value to brand owners over time.
Our proactive drive to innovation didn’t stop at aesthetic renewal; as a powerful backward integrated company, our solutions provided our customers (manufacturers) with reliable aseptic filling machines. We have now established ourselves as a total system supplier, in addition to aseptic packaging material.
In the domestic market, our multiple filling machines with speeds ranging from 7500 to 8000 packs per hour have already been installed. We are now developing high-speed machines capable of producing 10,000 packs per hour, which will provide brand owners with greater flexibility. The machine features a cutting-edge servo drive mechanism that smoothly drives the station and ensures high performance.
This revolutionary filling line, with a changeover time of approximately 3-4 hours, can pack multiple format groups (pack sizes) such as 100ml-125ml and 160ml-200ml. And there will be around 12-13 hours when the format changes from smaller packs to larger (100/125-160/200ml). This mechanism provides the unit with a high level of flexibility, a short changeover period, and a low total cost of ownership.
This will be a significant benefit for our customers that want to offer a diverse portfolio of formats to their end consumers. The first of these filling machines is already built and being tested at our Noida engineering site. Following the debut of this machine, there will be many more new launches to meet the other demands of the market.
On the manufacturing front, we’re working on a number of initiatives that will shift the market’s perception of Asepto. Aggressive work is underway to take Asepto global. The first step has been taken through our recent expansion announcement that marks a significant move to expand the brand’s horizons to other continents.
The initial phase of growth focuses on adding new machines to the existing line, which includes Germany’s best-in-class next-generation printing line (DAVIS STANDARD). This cutting-edge equipment includes advanced features and is loaded with sophisticated advanced technologies that make it incredibly efficient and safe and sound in operation. The machine prints at a speed of 500 MPM (meters per minute). Another high-performance slitting line has been introduced, which is superfast and produces at a speed of 1200 MPM. In addition, we have included doctoring line and additional tools for designing new formats in order to match the expectations and demands of our client’s diverse portfolio.
The expansion measures we’ve taken so far reflect Asepto’s strong market position and pragmatic outlook for the future. Needless to say, it’s the result of ever-increasing aseptic packaging demand. With this forward-thinking attitude, we intend to establish more factories in India as well as outside the country to meet market demand in the future. Today, we are certainly well-positioned and prepared to drive the aseptic packaging industry to new heights of supremacy. Our journey has just begun!!!
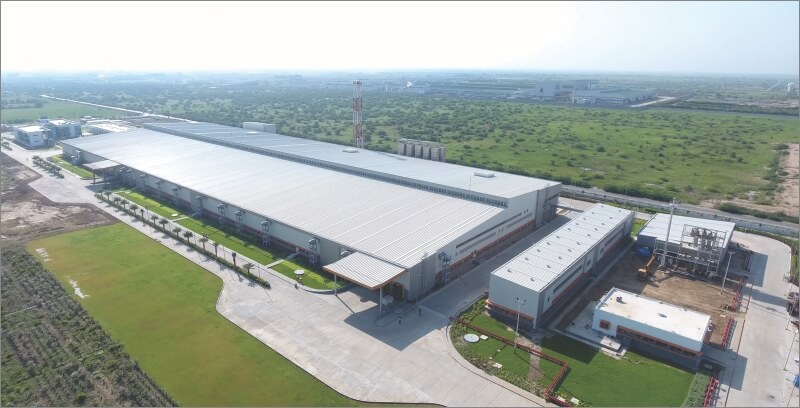