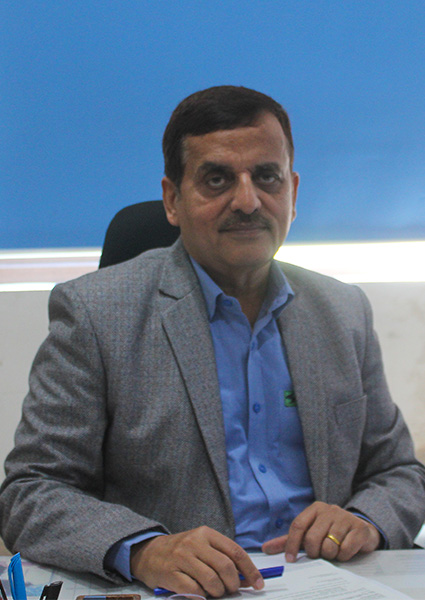
Paper Mart: How do you implement the water treatment process to facilitate the recycling of water and what are your different wastewater treatment strategies?
R. K. Bhandari: Paper industry is one of the most water-intensive industries and both the Government as well as the industry are well aware of their responsibility to the society to use this rare natural resource to its optimum level. Ours being an integrated wood and agro pulp and papermaking plant; we have three types of effluent streams, i.e., Black liquor, Wheat Straw Wetwash, and Bleached Pulp Wash effluent.
- Black liquor, which is regarded as the highest pollutant effluent in the paper industry, is completely burned in specially designed Chemical Recovery Boiler and the smelt is used to produce value added product – Sodium hydroxide which is recycled for the cooking of Raw Materials.
- The raw material washing effluent is also used for recovery of the energy in terms of methane (Biogas) which is used for burning in the boiler, thus, reducing the fuel consumption and also reducing the carbon emission. This effluent is treated in UASB-Based Bio Reactors followed by HRSCC, first stage Aeration with Jet Aeration system, followed by MBBR technology and then, it is finally sent to second stage combined aeration process.
- Bleached pulp mill wash effluent is treated in conventional two stage activated sludge process to achieve the prescribed norms of SPCB in final discharge.
Final treated effluent is discharged onto the plantation area where approximately 600 acres of eucalyptus plantation is developed to consume the total quantity.
Water Conservation
The water conservation is an ongoing process at SIL and a number of water conservation schemes have been adopted to save water at the process level. As a result of these efforts, SIL has achieved water consumption of 35-40 m3 per ton of finished paper and after expansion; the target is to achieve water consumption below 30 m3 per ton of Paper. The lowering of the consumption has been achieved by taking the following steps:
Pulp Mill:
- TRP (Twin Roll Press): Pulp consistency increases from normal 10-12% achieved in unbleached washer to 30% which reduces pollution load in bleach effluent and increases total solids as well.
- The foul condensate generated from evaporation of black liquor is utilized for the washing of unbleached pulp at BSW No. 4.
- Changes in size of spray nozzle diameter in pulp mill and paper machine: Lesser diameter and high pressure reduces freshwater consumption.
- Chlorine dioxide, alkali extraction & peroxide stage generated filtrate is used for dilution in same stage before washing.
Power Plant:
- Condensate from paper machine is re-circulated back over 90% to the boiler to replace freshwater consumption for steam generation.
Paper Machine: Utilization of backwater to recirculate, reuse and replace of freshwater:
- The generated back water from paper machine is used for pulp dilution to make thick stock to thin stock, (TSS level of water is 1500-2000 ppm)
- The machine back water is pumped into save-all for fiber recovery and clear water is being used in pulp dilution (TSS level of water 150-175 ppm)
- The industry has already installed two disc filters for the treatment of excess back water to reuse in pulp mill for dilution, pulp washing and further treatment in micro drum filter (TSS level of water is 150-175 ppm).
- This disc filter will give four types of outputs like — Recovered fibre, cloudy water, clear water and super clear water
- Super clear water from disc filter is treated here to give less than 5 ppm TSS, thus, it replaces freshwater in low pressure showers at paper machine, pulp mill washers, and chemical preparation. (TSS level of water is 5-10 ppm)
PM: What kind of investment has been put into the company’s water treatment infrastructure?
RKB: Water consumption after expansion — SIL has ambitious target to improve efficiency of the water treatment to further reduce water consumption below 30 m3/ton of paper by effecting recirculation wherever possible as explained in following steps:
SIL proposes to install UF-RO System for recycling of 3000 m3 of treated effluent initially to further reduce the freshwater consumption and we are exploring different technologies for their technical and commercial viability. The tentative cost of this plant will be INR 4 crore and we are working out the recurring cost on account of power, membrane replacement and how to handle the heavily loaded reject.
The following modifications has been brought in ETP to reduce pollution load and improve the treatment efficacy –
- The industry has commissioned a new Clarifier in the wet washing plant to reduce organic load in to Bio Methanation plant at a cost of INR 1.5 crore. The TSS load has been reduced by 2600 ppm to 2000 ppm (Approx. 25%).
- Increasing hydraulic load of COD/BOD in both streams to control the outlet of Biogas Plant- COD/BOD, the industry will introduce one more High Rate Solid Contact Clarifier (HRSCC) after anaerobic treatment at a cost of INR 0.5 crore.
- The industry has introduced primary aeration at a cost of INR 0.75 crore after anaerobic to reduce COD/BOD load on secondary effluent treatment plant.
- The industry has introduced primary aeration at a cost of INR 0.6 crore after anaerobic followed by MBBR technology to reduce COD/BOD load on secondary effluent treatment plant.
- MBBR and all aeration tanks are equipped with Surface Jet aerators at a cost of INR 1.0 crore to increase standard oxygen transfer efficiency.
- Addition of pure oxygen injection system through Jet aerators in aeration tank for better organic reduction and it will increase SOT efficiencies.
PM: Could you highlight the pivotal technologies and measures undertaken to minimize the consumption and reduce & treat large wastewater discharge?
RKB: The high-water consumption has been well controlled by SIL as the initial water consumption which was 65-70 m3 per ton of paper a few years back have been brought down to almost 40 m3 and after the expansion, it will be less than 30 m3 per ton of paper. We have consistently been on the path where we’ve been making efforts in the direction of lowering the water consumption to make it one of the lowest in the industry.
We have explained the total pollution load generated in different streams and the technology used for handling that. SIL always keeps in touch with the leaders in this field to further improve the techno-commercial aspect of these technologies. We were the first in India to have Anaerobic treatment of black liquor in 1995 when there was no such technology to handle wheat straw black liquor because of silica issues and the low scale of production. We had put up our Chemical recovery plant in 2006 which has been upgraded three times till now and a bigger soda recovery boiler was installed when we had increased our agro/wood pulping capacity.
PM: Could you tell us about the recent developments taken place in your plant with regards to water management and treatment? What path-breaking steps have you taken to minimize your environmental impact and make your mill environmental-friendly?
RKB: As we have already mentioned the steps taken for water management and treatment; now, we shall explain the steps we have taken to manage the environmental impact with respect to air pollution. All our boilers’ (Power boiler 50 + 90TPH and recovery boiler 80TPH steam generation capacity) emissions are controlled by providing four field electrostatic precipitators (ESP) at a cost of INR 20 crore with a target to achieve particulate emissions below 30 ppm whereas SPCB/CPCB standards are less than 150 ppm. The values which we’re achieving in particulate emissions are 80% less than standards.
SIL uses only rice husk in its existing boilers for making steam and no fossil fuel is burnt. We are starting a new boiler in December 2020 which shall use all kinds of biomass, especially the rice straw burnt by farmers in the fields, that is, the most aggravating source of air pollution. We are planning to further reduce our CO2 emissions by using the stack carbon dioxide in our proposed PCC plant which is under construction.
SIL regularly keeps a watch on its carbon footprints by getting GHG emissions study done by an independent agency based on ISO 14064 guidelines and then, we analyze where best we can work to reduce it. The current focus is to use minimum possible Grid electricity, reduction in the use of Furnace oil in Recovery boiler and effective management of 600 acres of Eucalyptus plantation for maximum possible sequestration.