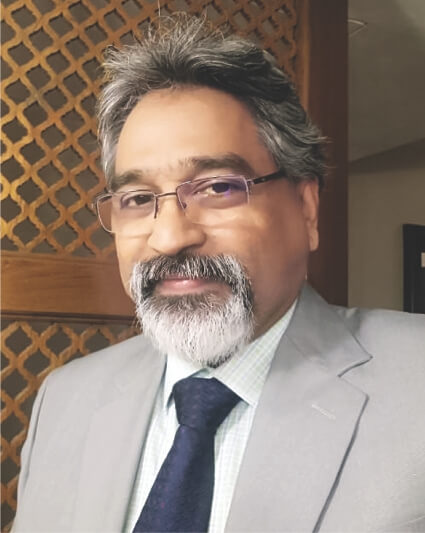
With its first unit commissioned in 1985, Tamil Nadu Newsprint and Paper Limited (TNPL) is one of the prominent bagasse-based paper manufacturers across the globe. TNPL’s vision is to adopt state-of-the-art contemporary technology and be the world’s most sustainable brand to manufacture eco-friendly paper and paperboards. The company has recently started up its own hardwood pulp mill, Unit II, with a capacity of 1,40,000 TPA, which has made TNPL self-sufficient in terms of hardwood. In a recent interaction with Paper Mart, Mr. SVR Krishnan, Executive Director, Tamil Nadu Newsprint and Papers Limited shared about the company’s recent developments, current challenges faced by the Indian pulp and paper industry, how to overcome them, water conservation initiatives by the pulp and paper industry, TNPL’s sustainability initiatives and Mr. Krishnan’s message to the industry.
“The money spent for protecting the environment is not expenditure, but an investment for protecting the future business.”
Paper Mart: Kindly tell us about the latest developments at your company.
SVR Krishnan: Our latest development is the start up of our hardwood pulp mill Unit II in December 2022, which was inaugurated by the Hon’ble Chief Minister of Government of Tamil Nadu , Mr. M.K. Stalin along with other senior ministers, at our Mondipatti plant. The capacity of the plant is 1,40,000 TPA, a chemical recovery island and a 20 MW turbo generator (BHEL) and other auxiliaries like chippers, auto conveying systems, fully integrated Chlorine Di-Oxide plant, Oxygen, Nitrogen plants along with an elaborate effluent treatment plant. That unit initially depended on the Kagithapuram unit or overseas supply to get hardwood pulp. However, we have replaced it now and are self-sufficient in terms of hardwood. Secondly, we have put a very elaborate effluent treatment plant to take care of the existing operations in Unit II. So we are performing as per the TNPCB and CPCB guidelines.
Watch: JMC Paper Tech Launches New Subsidiary JMC Papers
PM: What are the current challenges being faced by the Indian pulp and paper industry?
SK: A big challenge being faced is that after witnessing a peak of 200% to 300%, prices for raw material, pulp, coal and chemicals are now falling down. The final price of the paper and paper board is also coming down. This has created a big challenge as the paper mills are struggling to protect the margin. The orders are consistent, but the price table is very low, along with low incoming materials and raw materials. Moreover other problems are the shrink in the international FMCG usage and consumption, due to which the packaging requirements have come down by almost 15% to 20%. In these conditions, the niche segments have to open up and a lot of product development activities have to happen rather than depending on the traditional writing & printing paper. Though the ban on single use plastic due to its irresponsible usage and disposal has opened up opportunities for the pulp and paper industry, yet it poses some challenges too at the same time. Plastic used to be very user friendly, convenient and cheap, and now we face a challenge to make paper boards meet the utility point of plastics. That is where the pulp and paper industry has to meet the barrier requirements of the LDPE and HDPE films and also make it more affordable and economical. Even today, the paper bags, the paper board bags and the other biodegradable carrying items are costlier than plastic by at least two times. Additionally, there are challenges while using secondary fiber/recycled fiber for making food grade packaging grades, with respect to the control on odor, dioxin, toxin and heavy metal content levels etc. The waste water streams treatment also gets complicated due to higher TDS and conductivity, etc, for which the industry is working very hard with the chemical suppliers and machinery manufacturers. These are the challenges that the Indian pulp and paper industry is going through.
PM: How can the Indian pulp and paper industry overcome these challenges?
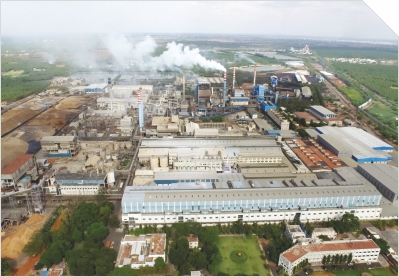
SK: We need to work intensively on imparting barriers to paper and paper board through various chemicals. These chemicals are all aqueous emulsion based coatings and these coatings give the water barrier and the oil and grease barrier. We at TNPL have also taken various initial trials and the results are encouraging. We are awaiting the certificates and clearance from CIPET and TNPCB for the compostability and biodegradability. Once received, we will launch the value of coated paper in another 2 to 3 months.
PM: What initiatives is the Indian pulp and paper industry taking in relation to water consumption?
SK: There’s a lot of good work which is done in the Indian pulp and paper industry on water conservation. Nowadays, all the units or machines available in the market are water efficient. Earlier, overall per day water consumption of mills used to be in the level of 60,000 m3, whereas today the good mills operate at 25,000- 30,000 m3 water consumption per day and when you talk about the specific consumption, it’s around 25 to 30 m3 per ton in integrated paper mills. If you talk about a stand-alone paper machine or a board machine, they are operating less than 8 m3 or 7 m3 per ton of paper or board produced.
PM: What steps is TNPL taking towards sustainability?
SK: We have embarked on the journey of manufacturing excellence, which is a tailor-made program encapsulating the 5S concept, the total productive maintenance (TPM) concept as well as the waste elimination concept. We have taken the positive points from these schemes and we have tailored them to manufacturing excellence, which is practiced on the shop floor, and has given a lot of benefits in improving the internal efficiency and the overall equipment efficiency of the plant operations. Moreover, our main focus is now on people’s development. We spend a lot of time on people development, building up the team and building up the knowledge base. We strongly believe in the 3P concept, which states that take care of people, people will take care of the planet and when people and planet are both taken care of, the profit is automatically taken care of.
Also Read: A Surge in Paper Imports: Dwindling the Indian Paper Industry?
PM: What message would you like to share with the Indian pulp and paper industry?
SK: The industry has to work on the sustainability part of the process today. When we say green and blue, green is for maintaining the flora and fauna and protecting the environment for future generations, whereas blue means to make the area pure, make the air breathable and be sustainable with respect to a lot of analysis and action plans. The action plans have to be irreversible and sustainable. Secondly, this is the right time to do some minimum spending to protect the environment and to make the business sustainable. The money spent for protecting the environment is not expenditure, but an investment for protecting the future business. It is the investment we make for sustainability for the long run in the business. And the third message is that internal efficiencies ought to be focused, which will help us do our best in the industry. Therefore my simple message is to shift the gear from managing to controlling.